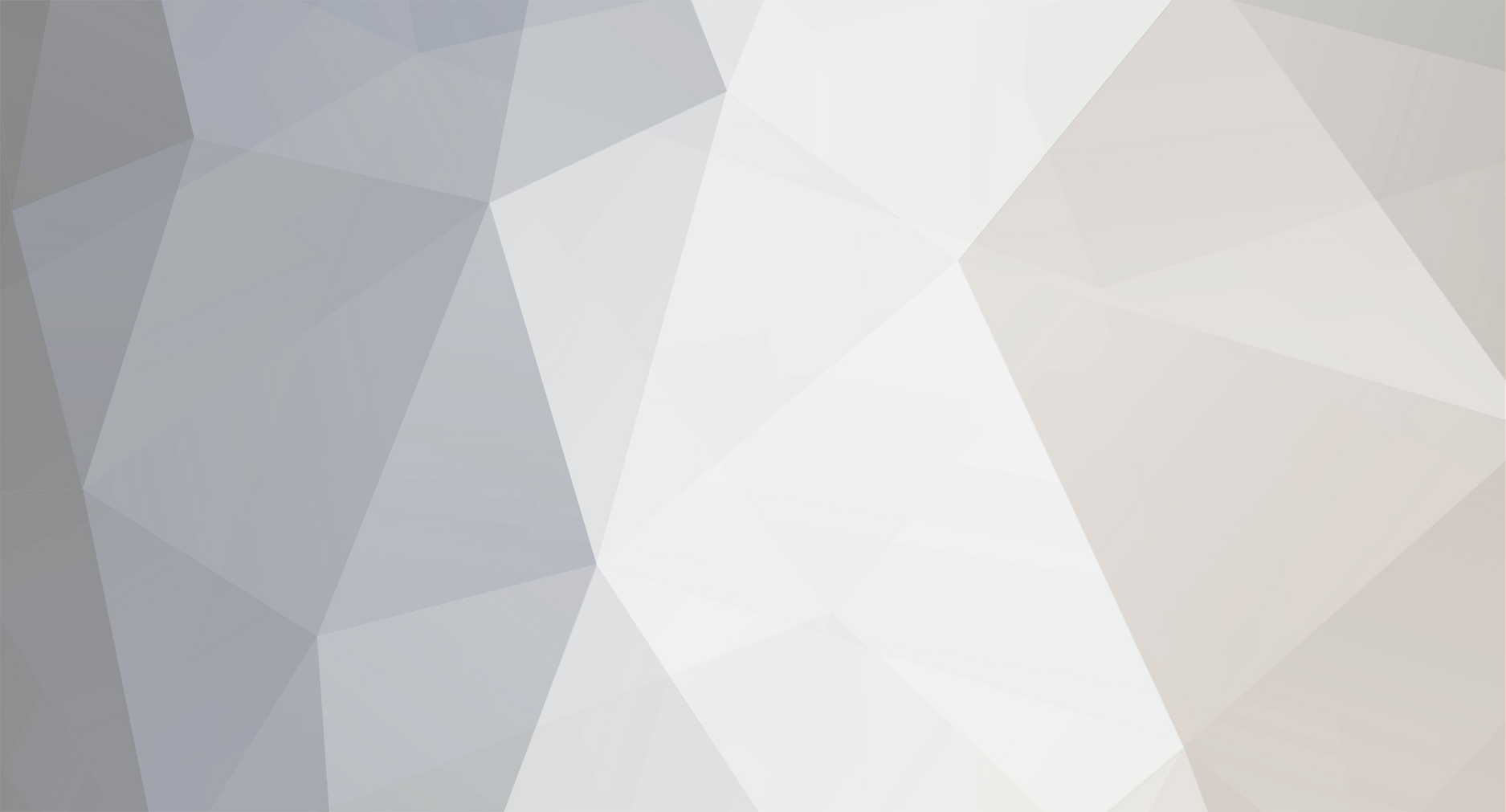
burn4005
Members-
Posts
544 -
Joined
-
Last visited
-
Days Won
5 -
Feedback
0%
Content Type
Profiles
Forums
Events
Gallery
Media Demo
Store
Everything posted by burn4005
-
I demand an update. Has anyone wound up the boost (25+psi) on e85 with these yet? Im very interested in the 63's on the 2.6..
-
Rb26 Turbo Upgrade, All Dyno Results
burn4005 replied to SLY33's topic in Engines & Forced Induction
Yea, 18ish psi on dash 5s is bang on 450hp/338kw. -
Hi Guys, I've gone a slightly different route with boost control on low mounts and am using a pair of turbonetics 30326 dual port wastegates on my HKS2530s and a 4 port MAC valve to suit. idea is I can run very low boost pressure in Mrs/valet mode (preload will only be around 7.5psi) but can wind in 26+psi on E85. also, having the 4 port solenoid will assist in keeping the gates clamped closed until the ECU says otherwise. my options for the boost source for the solenoid (which is located on the passenger strut right beside the turbos) are: 1) Tap each turbo and join with a Y piece into the wastegate solenoid. 2) Tap into the intercooler piping just after the twin-turbo pipe (which has the splitter mod done) 3) Just use the signal from the intake manifold pre-throttle plates. my considerations are: shorter hose length and closer to the turbos = better control. I figured the faster pressure response would be a good thing when the solenoid is directing pressure to the back of the actuators to keep them shut during spool the idea is to obtain optimum boost control with agressive ramp-on. inter cooler is a 120mm Greddy unit, so I'm not expecting significant pressure drop over it. boost control is being done per gear, with the TPS% position generating a MAP target with an Ethanol content modifier. so 100% thottle may be 20psi on petrol but 27psi on E85. that map target is then used in a target MAP vs RPM table that dictates the waste gate duty cycle to achieve pressure target. also under WOT conditions closed loop correction activates using PID control for minor corrections. the ultimate would be to use two separate solenoids, one for each turbo with its own reference but you would need to monitor turbo speeds to make the most of it I think.
-
My issue with the dominator 1800s is the clause: "Pump gas compatible for intermittent or under 90 degree F (32 deg C) ambient temperature use." 32 degrees is pretty damn low.
-
ECU Engine protection functions > Gauges Do the defi units have an auxillary 0-5v output?
-
Going E85 - Fuel Tank Saddle Transfer Hose For Jet Pump
burn4005 replied to burn4005's topic in Engines & Forced Induction
Gates barricade MPI. It's a brand new engine so its getting new fuel hose. 16 year old factory ones are not worth the risk of a split/leak and its a few hours to do (including fuel pump and submersible hose) -
Hi Fellas, Going e85 in my r34 gtr and am changing all the normal fuel line hoses, but noticed there is a hose that goes from the passenger side saddle of the fuel tank up to the jet pump in the fuel tank cap. Have peole been changing this to ethanol compatible hose or is it ok? I'm not sure if it's rubber or plastic... It looks like you'd have to drop the tank to get to where it goes into the saddle, or is there another way?
-
pardon my ignorance, but how you open injectors for more than 100% of the time? is it calculating say a 36ms required pulse width when the cycle time is only 30ms, but in reality, the injector has saturated?
-
Rb26 With Twin Hks Gt2530 Wont Make Power
burn4005 replied to avoiee's topic in Engines & Forced Induction
Something is up for sure... I made 550hp at the wheels on 23psi with a 2.5 inch to 3 inch twin front pipe and a 3 inch blitz nur spec catback. Didn't have a cat though. So exhaust size isn't your issue. Bigger is always better, but its not choking you at that power level if its a healthy flow path. Collapsed cat? Power fc,700+cc injectors, decent fuel pump and z32 afms should be on your shopping list for sure. Those turbos are a waste without suporting gear at the least. -
aux output using a 500-1500hz signal to the Fuelab pump is needed, varied duty cycle. 20% is the minimum, the pump will shut off if its lower than this according to the manual. a user defined 2D table attached to the aux out channel using duty cycle would be the best solution if your ECU is capable of defined table axes. otherwise a MAPXRPM table, but this effectively resolves into a duty cycle as that is the actual fuel demand. at 100% TPS at 2000 rpm you're only going to need 25% of the fuel compared with 100% tps at 8000rpm. so i think map would be better for a 3d table. just remember you want to be ahead of the curve as far as pump speed vs fuel demand. the engine is capable of changing MAP very quickly, and there will be a slight delay for the fuelab to react, so running the pump at 10-20% faster than is required will mean you will always have some returning to tank, and also remember the jet pump on the return line that transfers over the saddle in the fuel tank will only work when you have decent return flow.
-
Rb26 Fuel Pressure Sensor Tap Location?
burn4005 replied to etang789's topic in Engines & Forced Induction
you'd be surprised. ethanol (@ 1.2cP) at 400lph in an 2.5m x 8mm pipe with a typical surface roughness is more like 4-5psi. add things like bends and it's even higher. if you are using a fuel modelling calc in the ecu that requires injector pressure delta, a 10% error is certainly significant. example, courtesy of fuelab: -
Rb26 Fuel Pressure Sensor Tap Location?
burn4005 replied to etang789's topic in Engines & Forced Induction
not actually true. you will have pressure drop over the fuel line from the pump to the rail, which is exacerbated the smaller the diameter it is and the higher the flow. if you have to mount sensor before rail, put it as close as you can to it. after rail position is less important. anywhere between rail and reg is fine. -
there was a lot of mis information here.. and a note, if you solder each wire individually before you join them all you will get much better heat penetration. basically running high-Z injectors with the ballast meant that your injector circuit impedance was higher. this was extending the dead time of the injectors as your injector coil current was lower so they take longer to open before fuel delivery actually begins. without correcting for this, your effective fuel delivery pulse would have been shorter, and at idle pulse widths (~1.5-2ms) may not have opened at all. re wiring fuel pump shouldn't affect anything as long as your regulator is large enough to bypass the entire fuel pump flow. it just maintains your base pressure regardless of flow. if you get your injector scaling % and dead times correct it should run perfectly. the 1000cc aren't too bad as far as low pulse width flow linearity so if you are only driving to the tuners like a grandma, bugger all Throttle and staying away from any positive pressure and only low revs you can have it as lean as it will run happily. if it hunts around just richen it up a bit by reducing the scaling value. the narrowband Voltage/reading should give you enough information at cruise conditions to know when you're in the ballpark (more than 0.6 or so volts). a good way (if it starts) is to let it get to a stable idle (post start enrichments over), then raise the scaling value until it hunts or your narrowband value drops below 0.2V (you'll be around 15-16 afr) ... then go in the other direction until it gets a bit rough. you'll be around 10/11.. split the difference, that'll be good enough. you'll have no load on the engine while you do this, and it wont take long at all. so you won't damage anything. if it's a new engine with new piston rings i would be much more careful, as your bed in procedures require good AFRs so I wouldn't take the risk. you need to know what the flow and dead time details for the injectors you have just replaced are so you can make the corrections. Apexi Docs: If changing 440[cc/min] to aftermarket 600[cc/min] 440 / 600 = 0.73 Enter the value "0.73" for each cylinder. Bolt-on turbo spec. POWER FC applications assume that the injectors have been upgraded. This is why "1.000" is not entered as the starting data for the injector values. Injector Lag Time Setting The POWER FC includes factory vehicle injector data. If you switch to any other type of injector, be sure to perform the calculations below and input the correct values. Changing the factory 440[cc/min] with 0.78[msec] injector lag time to an aftermarket 600[cc/min] injector with 0.85[msec] injector lag time is: "Injectors to be used" - "Factory Injectors" = "Correction Value After Changing" 0.85[msec] - 0.78[msec] = 0.07[msec] Enter "0.07" into the [msec] parameter for each cylinder. *If the aftermarket injectors have a shorter lag time, add a "-" (minus) before the value. Factory injectors are 440cc @ .772ms. for your reference: Bosch 1000cc ev14 deadtimes @ 43.5psi: 8v 2.35ms 10v 1.72ms 12v 1.22ms 14v 0.86ms 16 0.68ms
-
look good and that's a great price. is that trade or did you just email them? did these come with a flow test sheet? and do these have the 6 hole diffuser plate on the bottom or has it been removed and only the single orifice is visible? I'm guessing they are the 0 280 158 040 injector with the diffuser plate removed sorry for the 20 questions but I'm just about to pull the trigger on a set myself, and that's an awesome price.
-
[Closed] Borg Warner Efr Series Turbos
burn4005 replied to Lithium's topic in Engines & Forced Induction
Hi Geoff, Have you had any results with the EFR 9174 hybrids? i've read the spool performance is only 50-100rpm down on a 8374 but your compressor efficiency moves up the revs a fair bit. also, i remember seeing spool diverter valve a while ago. is there any plans for Borg Warner to release it for the larger frame exhaust housings? -
Under Bonnet Temperatures Causing Heat Soak
burn4005 replied to edizio's topic in Engines & Forced Induction
It's a bit late but I thought I'd share an intake temp sensor I have found that fits in the stock position m12x1.5 It's long enough to stick out in the air stream and has an open element so reacts quickly. http://www.finjector.com/verkkokauppa/eng/intake_air_temp_sensor_long_25_mm_open_type_fast_element_for_turbo_engines_m12x1_5-p-531991-28/ -
Yep, the newer baps are 17-20v I think. Older ones had an adjustable gain knob starting at 0% so would do 13.5v and up.
-
Kenne Bell have said that the walbros fail with sustained use at 17v and above from their own testing. I only need 420lph or so on e85 at 28psi and 8300rpm if my VE map is accurate, so 16v should do it. I suspect the VE will fall away above 24 or so psi due to the small turbines on the hks2530s, so it will probably end up being less.
-
yea, for that cash a pwm fuellab is the ticket. you need to be a bit careful if you use the electronic regulator. for cars that snap on boost very suddenly with a big jump in injector flow the pump can be a bit slow to react and you see a pressure dip. better to map a aux pwm output on a 3d load table from the ecu to pre-empt instead of react. i've got a boost-a-pump and a 20khz capable solid state relay, will report how a walbro 460 goes at 16v or so on a pwm drive. i've heard numbers like 568l/hr for a 460 at those voltages being thrown around, compared to 389l/hr at 13.5V.
-
Im interested, because the REAL Bugatti pump (ti automotive L5LM) requires a brushless motor controller to run. and is bloody difficult to find a supplier, they're around the $700-800 USD mark. plus you need a brushless VSD controller flows tremendous amounts at high pressures and low current levels. its a progressive cavity screw pump. there is also a DC version that is similar form factor but only flows ~330lph that will be the pierburg others are referring to. generally is shown with a blue band around the body. found this place selling the real deal for USD$795.... it flows 458l/hr at 5 Bar (72.5psi), at only 10.5 amps. http://www.jayracing.com/fuel-pumps-c-2_5/jay-racing-pro-series-l5lm-veyron-brushless-screw-fuel-pump-p-52147.html
-
[Closed] Borg Warner Efr Series Turbos
burn4005 replied to Lithium's topic in Engines & Forced Induction
No, two boost controllers will give instability as the integrals will fight each other. One solenoid goes to the two actuators. They should have the same preload so their opening characteristics are the same. Usually you wind up an air compressor regulator and make sure they move in unison. -
[Closed] Borg Warner Efr Series Turbos
burn4005 replied to Lithium's topic in Engines & Forced Induction
Any dual port actuator on a 4 port solenoid should be able to hold it shut. -
[Closed] Borg Warner Efr Series Turbos
burn4005 replied to Lithium's topic in Engines & Forced Induction
That's a fantastic result then, I was just having trouble reconciling the speed axis on that to RPM mathematically... an EFR8374 is definately on the cards for me in the next year or so. Having Matchbot and all the turbo maps available is definitely a huge plus for the Borg. I can't make an educated decision on a 6262. its just "yea mate they're good for an RB26".. I'm yet to stretch out my 2530s on E85, but I can't see them being as good.