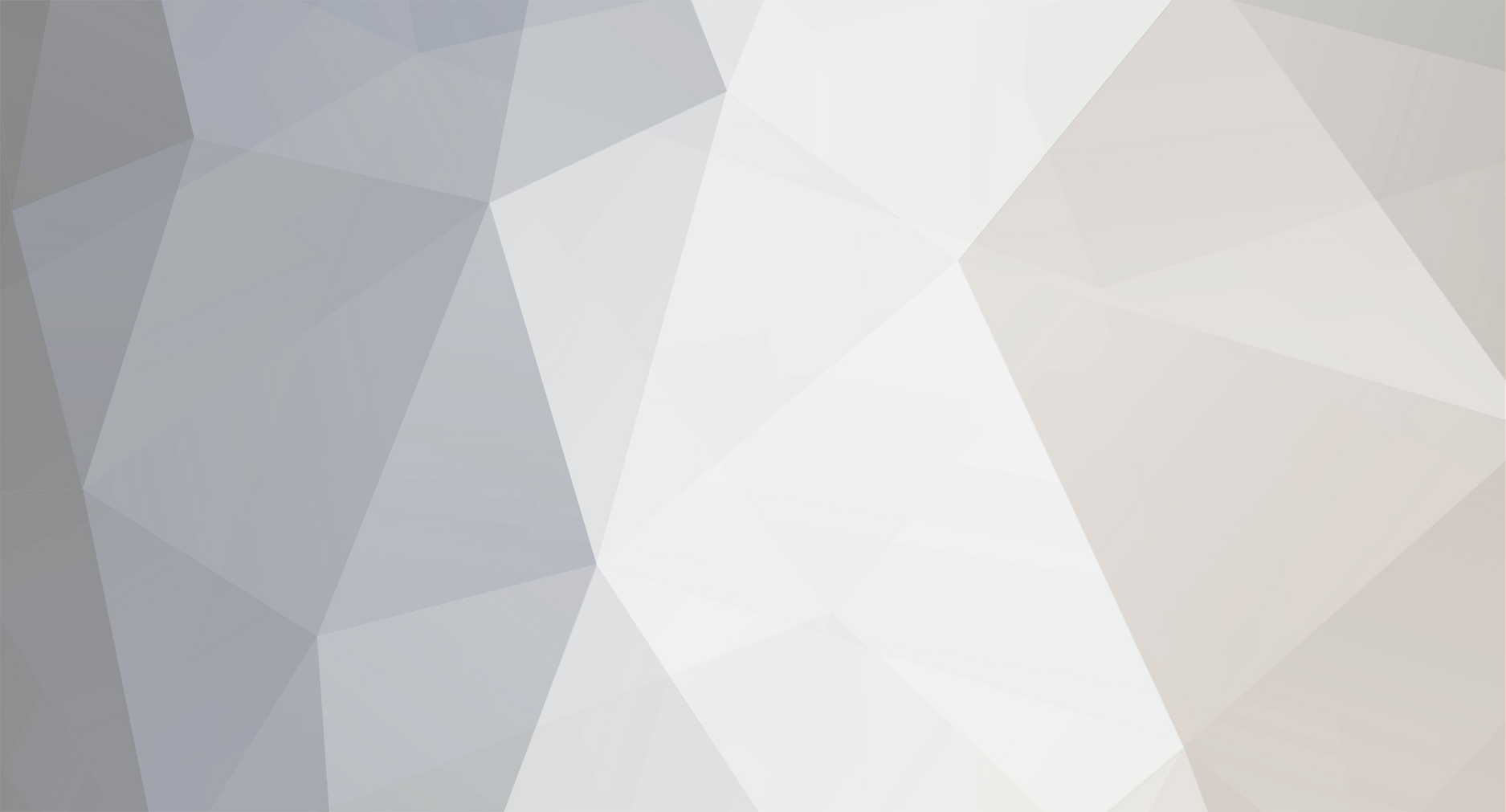
burn4005
Members-
Posts
544 -
Joined
-
Last visited
-
Days Won
5 -
Feedback
0%
Content Type
Profiles
Forums
Events
Gallery
Media Demo
Store
Everything posted by burn4005
-
Borg Warner EFR Series Turbo's V 2.0
burn4005 replied to Piggaz's topic in Engines & Forced Induction
Nope. 9280 will do 110lb/min all in and its as big as they get. If you're staying with efrs you're going twins. And it's probably a better idea anyway. -
Single turbo upgrade - sizing options for a mild 2.6
burn4005 replied to shodan's topic in Engines & Forced Induction
I can recommend JHHs 1000hp ati balancer with integrated trigger wheel. they have a motec 36-2 wheel welded on the back of them along with a hall effect sensor and bracket. very impressed with mine and a lot less f**king around than some other alternatives that require timing gear replacement and oil pump cutting. timing is now rock solid, it was abysmal with the cam trigger setup under heavy loads. let me get a good 3 degrees more timing into it at high loads (~30psi) which is LOTS of free power. -
Borg Warner EFR Series Turbo's V 2.0
burn4005 replied to Piggaz's topic in Engines & Forced Induction
it looks like they may be evaluating options or doing mockup/fitment. but surely dual 7670s aren't going to make the quoted 1600hp so maybe not. and its footage of two different engines, as the Agera RS and one:1 engines definately had precision snails on them. here are a couple of screen grabs for the Jesko video... EFR is on one side of the motor, precision is on the other? (ps that finish on the investment cast efr turbine housing is NICE.. like the early ones before they changed to a cheaper sand casting method) -
Limits of stock 5/16" (8mm) fuel lines
burn4005 replied to 5-0 Ignite's topic in Engines & Forced Induction
I'm making 500awkw on e85. stock fuel lines, stock nissan fuel filter, stock rail, tomei type-L and bosch 1650s. single in-tank pierburg L3LM @ 17.5v (boost-a-pump), range rover PWM pump controller and an aftermarket fuel hat. holley hydromat on tank floor. very efficient pump at high pressures. can only just hear it prime before starting the car. once engine running its effectively silent. not sure on pressure drop but don't care either. ECU uses injector delta pressure in model. -
this is one of the dumbest f**king things I've ever read. the only thing that might make sense here is you are actually Japanese and are running all your answers through google translate into english. the reason you are being attacked is you have been unable to convey any coherent concept whatsoever but are still somehow attempting to claim the intellectual high ground here.
-
holy f**k Slap you did not take my advice. the knock sensor is a microphone. it generates an AC wave. that is the sound of the motor. taller wave = louder. spacing of the waves = frequency. its not a DC voltage. a sound wave can have many many many frequencies. it is continuous, not discreet. you only care about noises in the frequency range the engine vibrates at when it knocks. a decent ecu will filter that noise to a particular "band" of frequencies (say 6-7khz). the peak Amplitude of that signal is your knock level. it can be in volts, it can be in ADC counts. if your engine is not knocking it will be quiet in this range. LOW VOLTAGE. if it IS knocking it will be loud in this range HIGH VOLTAGE. a shit ecu will not filter the frequency, which is ok if your sensor is resonant to your engine knock frequency. but for a wideband sensor. the voltage you are reading will be the PEAK voltage seen by the ecu, and probably have a peak/hold circuit that gets reset after a delay. now for this to be useful, you need to know: is your sensor wideband or resonant? does your ecu do bandpass filtering on that signal? the voltage you are looking at is an indicator of the VOLUME of the noise the knock sensor (microphone) is picking up. that is NOT usefull if you have the following: wideband sensor with no bandpass filter (this will be all the engine noise) this IS useful under the following: wideband sensor with bandpass (this is knock frequency only) resonant sensor with or without bandpass (if sensor is resonant to the frequency your engine knocks at) if you want to know how LOUD the signal is, you can use a peak/hold multimeter. this will just tell you maximum volume, it could be at 100hz or 15khz. it won't tell you about knock. if you want to know what FREQUENCY the knock is occuring at you will need a scope. you need both the frequency and amplitude of the signal to work out if its actually likely to be knock or just loud noises at frequencies you don't care about. to understand what is happening you really need to plug the knock sensor into a usb soundcard and use some spectrogram/ real time fourier (frequency) graph software. something like this: https://digh.com/product/deka/ some free software I use is this which works great. http://www.sdradio.eu/weaksignals/spectran.html
-
Slap, type less statements ask more questions. I have a Billy Madison quote here but I'll just say I award you no points, and may God have mercy on your soul.
-
Borg Warner EFR Series Turbo's V 2.0
burn4005 replied to Piggaz's topic in Engines & Forced Induction
Geoff I'm curious about how the 8474 is being marketed by Borg warner against the 9174. Or is is replacing it in the lineup going forward? -
Borg Warner EFR Series Turbo's V 2.0
burn4005 replied to Piggaz's topic in Engines & Forced Induction
Swap to some Denso IK01-24 or NGK R7434-8 plugs and you won't look back. oh wait, are you still talking evo or RB? -
buy a set of inconel T04 flange studs and you'll never have to worry about it.
-
and if you REALLY need it to sound fully hectic bro these guys can do a compressor cover mod for you https://www.t51r.com/
-
more on this, if the ramps meet at what looks like a 90 degree angle its just a nissan lsd: if the ramps are much more shallow are more like a 135 degree incident angle like this then its a nismo diff.
-
I hope you're using a power FC too, the pinnacle of japanese performance. looks like a colossal waste of time and money to me. this is HKSs own literature.. find a used T51r SPL and stick that on instead if you're chasing a period-correct 1990s power curve.
-
Planning RB28 build need suggestions!
burn4005 replied to etang789's topic in Engines & Forced Induction
Emtron KV8 is the correct answer. -
Borg Warner EFR Series Turbo's V 2.0
burn4005 replied to Piggaz's topic in Engines & Forced Induction
Wow what a torque slab! what size motor is that on and how much head work? -
Single turbo upgrade - sizing options for a mild 2.6
burn4005 replied to shodan's topic in Engines & Forced Induction
8374 because eventually you'll want e85 and 480kw+ I had 400kw, got over it and now I have 500kw. I like 500 better. -
dual vs single entry fuel rail
burn4005 replied to Murray_Calavera's topic in Engines & Forced Induction
my Damper is only a small OEM style bosch one with an adjustable pre-load installed just before the fuel rail that I'm sure is quite compressed at elevated pressures so would have little effect in high boost high power operating zones. i was only concerned with low pulse widths at relatively low fuel pressures, which is where you were seeing your issues. I'm also using a progressive cavity twin screw pump that provides very linear fuel delivery, whereas a turbine style pump will struggle a bit with very choppy fuel pressure. the walbros really do not like being run slowly, whereas the Pierburg stays very linear in its supply. there is no manifold reference line on my FPD, and I still have a few meters of Gates rubber line in my fuel system that would also provide a dampening effect. I use the VP M2 additive that seems to keep the rubber in good condition and I never leave E85 sitting in it for extended periods. and yes, running all solid line would certainly provide a much noisier fuel pressure do to the lack of elasticity. -
dual vs single entry fuel rail
burn4005 replied to Murray_Calavera's topic in Engines & Forced Induction
Eh, overrated. I have added a pulsation damper to the pre rail feed at the 1650cc inj are pretty choppy though. And ecu uses live rail pressure measured at the regulator in the fuel model I'm at 500awkw on e85 in an r34 gtr. stock lines, stock filter and stock rail. I have an egt sensor on each cylinder and they're all flat on a long pull. Not sure where this pressure drop issue comes from I mean it is a physical effect but your fluid velocity would need to be massive for it to be important over a 1m long straight rail. Yes, the rail pressure will be higher than what the regulator sensor sees due to fluid flow mechanics, and the effect gets stronger the high the bypass rate but low viscosity warm fuel travelling in a straight rail this gradient will be very small. The twin entry rails with very high fuel demands introduce strong turbulence at the centre return affecting the two centre cylinders. It's better to have the fuel travelling in one direction. A large enough rail with a bore size to suit the delivery (should be larger than the hose used to feed it so no supply issues exist) is more than adequate. I just did a quick calc and the drop accross a 1m long straight extruded tube of 15mm diameter with a flow of 10l/min of room temp ethanol is 0.145psi. The real effect will be even less as at high duty cycles you are dropping roughly 1/6 of the flow as you cross each injector so the differential decreases. This is one of those mates brothers cousins dogs auntie said things but until someone puts a sensor pre and post rail to prove it I'm a non believer and am feeding my engine well over 800hp worth of e85 without an issue. -
Emtron do a Kv8 plugin for skyline gtrs. Worth a look.
-
Ok so this is how this thread will go down. I and everyone else is going to say go a split pulse manifold at a 1.05a/r rear on it as you'll choke it. Then an American is going to come in here and say nah he made X power with the 0.92 and a war will break out with Dyno sheets and Aussies calling American dynos shit.. Basically go a 1.05. I did and made 492kw at the treads and the turbo is at Max speed. 127,000rpm.
- 5 replies
-
- 4
-
-
-
- borg warner
- turbo
-
(and 3 more)
Tagged with:
-
Borg Warner EFR Series Turbo's V 2.0
burn4005 replied to Piggaz's topic in Engines & Forced Induction
You can do a fair bit of testing around engine pressure ratios with an orifice plate or butterfly as a restriction in the exhaust. Every psi of extra pressure post turbine will be likely ~3x that amount in the exhaust manifold when you factor in the operating turbine expansion ratio. -
Borg Warner EFR Series Turbo's V 2.0
burn4005 replied to Piggaz's topic in Engines & Forced Induction
Euro 7? Life racing's charge temp correction and transient enrichment/decay is far too simplistic for that. there is zero chance they are using their ECU in an OEM situation and meeting that standard. a one-off non-performance tune of a car to scrape through euro6 maybe. but oem e7, nah. enough internet debate, and I know you love them as a dealer/partner but they're just another option in the middle of a sea of many. -
Borg Warner EFR Series Turbo's V 2.0
burn4005 replied to Piggaz's topic in Engines & Forced Induction
sorry I assumed the max speed for a 9180 was ~1119/120k rpm from where you've started blanking out. discovered now its 116k so you can see where I was coming from. -
Borg Warner EFR Series Turbo's V 2.0
burn4005 replied to Piggaz's topic in Engines & Forced Induction
as with anything, shit in = shit out. if you have enough fit for purpose sensors (fast response, high accuracy) that are correctly calibrated, know your injector flow ACCURATELY (which is the difficult part of this) there is no reason to doubt the result. A VE model is just an abstracted correction function using physical models. you could convert all the corrections to ms and have no difference, and would suit your "motosports". they're fully interchangable. the advantage of a VE model is you can have single variable corrections as things are coupled in the model, whereas in a ms map they would be multivariate. sure, its not going to be within 0.01%, but in a dynamic real time system its not neccessary to go to that, its only a compressor map, and its a visual tool. The log I have above, the compressor stonewall flow vs turbo speed matches to within 0.8% of the BW supplied compressor map. if you are telling me that isn't useful data then by all means keep "intending" to set up a test bench. OEM manufacturers go to extreme levels to accurately model engine characterists because they REQUIRE it. emissions are getting incredibly tight. motorsport engine control is basic stuff by comparision, especially on the fuelling side. those advanced motorsport ecus aren't doing anything clever, they are just very reliable, don't change constantly, come with excellent datalog analysis and professional support, and often retardedly complicated licencing requirements on top of the hardware cost, but that's another story. the torque control and gear shifting is what you're paying for. the Bosch motorsport ecus (even as old as MS5's etc) use a relative fuel mass to lambda target, the air temp correction is based in a NTP relative ideal gas model and the final fuel charge is converted to an injection time later from the Q-stat flow so get off your high horse.