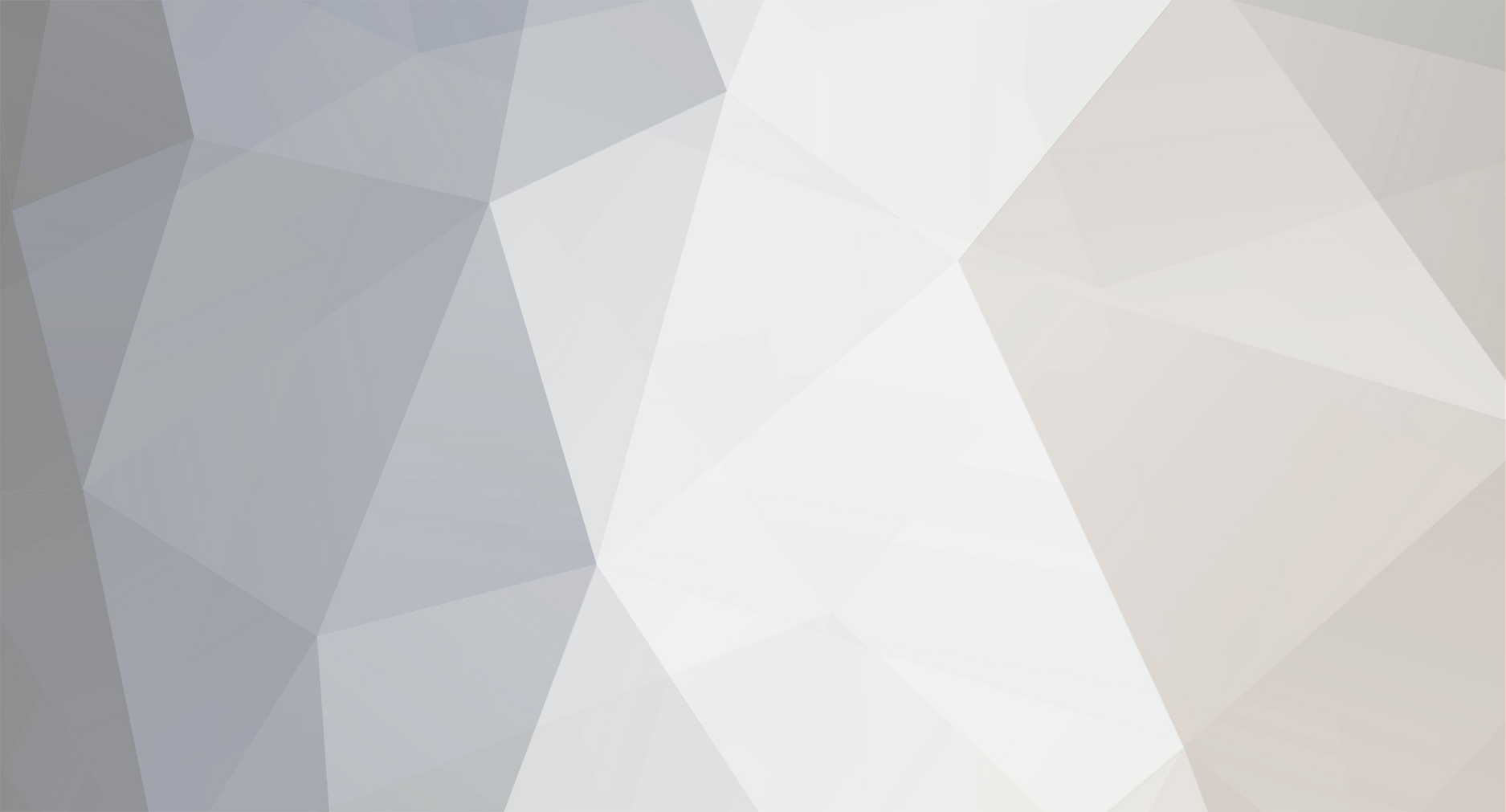
joshuaho96
Members-
Posts
2,059 -
Joined
-
Last visited
-
Days Won
5 -
Feedback
0%
Content Type
Profiles
Forums
Events
Gallery
Media Demo
Store
Everything posted by joshuaho96
-
R32 gtr hood latch support/lock part number search
joshuaho96 replied to eli995's topic in R Series (R30, R31, R32, R33, R34)
65601-05U00 is the hood latch. 62550-08U31 is the support that holds it to the radiator core support. They are all super discontinued so I don't really have any great leads on how to source this stuff. -
RB25DET Engine Oil Dipstick Length
joshuaho96 replied to DraftySquash's topic in General Maintenance
AA000 is for R34 GTT. 11140-05002 is not a part number that exists in Nissan's parts catalog. R33 GTST is 11140-21U00. 11140-05U02 is for the RB26. -
Oil Control In Rb's For Circuit Drag Or Drift
joshuaho96 replied to Sydneykid's topic in Engines & Forced Induction
Bumping this thread yet again, has anyone ever tried putting yet another vacuum regulating valve on the hose that goes between the turbo inlet? Something local owners have mentioned is the Radium breather pipes de-restrict the valve cover but it actually produces an undesirable outcome in practice, way too much air is sucked out of the crankcase and a ton of oil comes with it as well. As far as I can tell the PCV diaphragm in these modern euro wet sump performance engines is active during boost as well, there's just a check valve to block boost from entering the valve cover and crankcase as there's no inherent check valve function in these diaphragm-type valves. Hopefully I'll be able to try some of this out soon. The Volvo XC90 4.4 V8 has a nice external version of these things. -
AFAIK does the base map for Haltech even have the 4D compensation enabled? It's been a while but when I looked at it I remember it was actually using pure TPS as one load signal and MAP for another. Seemed workable but not ideal by any stretch. A lot of people have "make the event-itis" which leads to stuff like this happening.
-
It's weird to me that you say this because I'm pretty sure locals with relatively standard standalone tunes (boost/barometric compensated alpha-N) still have driveability issues when they pop intercooler hoses. Maybe with enough data I can just train some kind of model that spits out an expected grams/cyl given every sensor input except MAF like what FCA did with their Pentastar 3.6 ECU logic. Basically stock everything. The main motivation honestly is to have a sensor that can be a decent baseline source of truth. In scenarios you're describing obviously it won't work every time but it seems to me the number of corner cases that exist in MAF load is maybe not as severe and difficult to manage vs ITB alpha-N with some MAP/barometric compensation.
-
Is MAF load really that bad? I'm not trying to do big power, my only real desire is VCAM and flex fuel support so I'm not terrified of blowing my engine apart from CA's appalling 95 RON "premium" fuel. Stuff like playing with closed loop boost control and really dialing in my transient fueling and ignition are frankly just to prove to myself I remembered something from uni.
-
Right, but I thought the problem has been for a while now that even if you know manifold pressure + throttle position you still have non-linearity and aliasing issues vs actual engine load? One way I can see things simplifying is going DBW, then all air going into the engine is represented by the throttle position. As opposed to a random bimetallic strip vaguely linked to engine temperature opening and closing a shutter or some random power steering air valve suddenly allowing a bunch of bypass air. But the same throttle position/RPM at ~atmospheric MAP in different gears is not guaranteed to be same engine load? Honestly, ITBs are of such dubious value IMO. I don't know why these things are hyped up so much. The main benefit as far as I can tell is you reduce the likelihood of cross-cylinder EGR scavenging with significant cam overlap at idle. I would absolutely run speed density and be done with it if not for this fairly esoteric control problem.
-
You're not wrong, but this is one of those things I need to learn the hard way. I really, really dislike alpha-N for ignition or fuel load and I don't feel like pulling apart the manifold again for single throttle body conversion any time soon. I might be tempted to buy an Emtron for the throttle mass flow setup though, that might work well enough to get me off of this whole factory MAF setup idea but the way I see it the end result is still going to be scaling the load axes in cylinder airmass regardless.
-
The general simplicity of the generic conditions/triggers in Haltech kind of drive me nuts. For mysterious reasons I felt like trying to replicate OEM catalyst light-off ignition timing but there's no reasonable way of doing any kind of math like finding the delta between IAT and CLT at engine start to set a flag that indicates cold start. Stuff like that is easy with Link. On the other hand, Link straight up doesn't support dual MAF load on the RB26 so...
-
Wasn't there some discussion of how the Hypergear high flow actually has different dimensions so it's not a true bolt-on replacement? Honestly if that's the case I would consider just going true twin scroll and go down a massive rabbit hole of getting all that to package as close to stock as possible.
-
1. Factory knock sensors for now, honestly the RB26 OEM knock sensors seem ok as they're flat response instead of resonant type but they appear to be internally grounded to the block. If I do replace the sensor it would just be to get ones that are not internally grounded so a differential input can be used to reject common mode noise. Definitely plan on fixing this as a part of the tuning process. 2. Never deliberately induced knock, though I guess I could try that experiment if I really wanted to. 3. All of this is basically on a stock engine + ECU, only modification is HKS GTIII-SS turbos and a Nismo plenum. Currently I run it with the wastegate solenoid unplugged so it won't try to raise boost past wastegate pressure.
-
Are the factory timing tables actually that far off the mark? Even on CA ~95 RON I don't hear any gravel in a can. I do get some vibration around 1200 rpm just off idle and a light grumbling noise, but even when I've filled up with 106 RON fuel at 4.24 AUD/L none of that goes away. ECU also has never showed signs of switching over to knock maps. My plan was stick to factory timing up until it's at the last load column and ask for a trusted RB tuner to handle the rest. Probably not exceeding 1 bar on 95 RON, but we get E85 here so flex fuel should make it safe enough to run basically MBT timing considering I have no plans to bump the compression ratio over stock.
-
You're not wrong, but more than a few times I've heard of people running into issues where their injector characterization isn't quite right and that approach works for that specific configuration but once they switch over to a new set they discover a whole bunch of stuff wasn't set up correctly. It's slightly more annoying to reverse engineer the OEM MAF transfer function but you already have the sensor wired up to the factory harness so keeping it around for a few weeks more while you figure out the tune is easy enough. I've seen GM also use a combination of both MAF + MAP in their ECUs before, MAF is for steady state and a calculation of the cylinder VE to correct the base VE table, then in transients it uses that calculated VE + raw MAP to determine cylinder filling somehow.
-
Honda's hybrid system can be easily scaled up to PHEVs. Series hybrid at low speeds, at higher speeds the engine directly drives the wheels but there can still be some power bled off to charge the battery + the electric motor can still provide parallel assistance too. It's really only a question of will at that point. Toyota's PHEVs are selling incredibly well at the moment because of the flexibility. You can run on EV mode when it makes sense, but if you're planning on doing a long highway drive you can still fire up the gas engine and not have to worry about dealing with the rather miserable state of public charging infrastructure.
-
Only reason to keep a MAF on your RB25 is to be able to easily calculate true VE if you know what the factory voltage curve represents in grams per second of flow. Also allows you to do things like pull the original OEM ignition + AFR target tables and use those as a starting point for your base map. Once you're well and truly done tuning though there's no need to retain the MAF.
-
RB20DET lean on cold start
joshuaho96 replied to MidnightR32's topic in R Series (R30, R31, R32, R33, R34)
I don't know, honestly. Easier to just use a CAN wideband with the Haltech so you can get the ECU to control the wideband in the manner described. -
Now that the break-in period for both clutch and transmission is nearly over I'd like to give some tips before I forget about everything that happened, also for anyone searching up how to do this job in the future: You will need at least 6 ton jack stands at full extension. I would go as far as to say maybe consider 12 ton jack stands because the height of the transmission + the Harbor Freight hydraulic platform-style transmission jack was enough that it was an absolute PITA getting the transmission out from under the car and back in. The top edge of the bellhousing wants to contact the subframe and oil pan and if you're doing this on the floor forget about trying to lift this transmission off the ground and onto a transmission jack from under the car. Also do not try to use a scissor jack transmission lift. You have to rotate the damn thing in-place on the transmission jack which is hard enough with an adjustable platform and a transmission cradle that will mostly keep the transmission from rolling off the jack but on a scissor lift with a tiny non-adjustable platform? Forget it. Use penetrating oil on the driveshaft bolts. I highly recommend getting a thin 6 point combination (box end + open end) wrench for both the rear driveshaft and front driveshaft and a wrench extension. These bolts are on tight with very little space to work with and those two things together made a massive difference. Even a high torque impact wrench is just the wrong tool for the job here and didn't do what I needed it to do. If your starter bolts aren't seized in place for whatever reason you can in fact snake in a 3/8 inch ratchet + 6 point standard chrome socket up in there and "just" remove the bolts for the starter. Or at least I could. It is entirely by feel, you can barely fit it in, you can barely turn the stupid ratchet, but it is possible. Pull the front pipe/downpipe before you attempt to remove the transmission. In theory you don't have to, in practice just do it. When pulling the transmission on the way out you don't have to undo all the bolts holding the rear driveshaft to the chassis like the center support bearing and the rear tunnel reinforcement bar but putting the transmission back in I highly recommend doing this because it will let you raise the transmission without constantly dealing with the driveshaft interfering in one way or another. I undid the bottom of the engine mount but I honestly don't know that it helped anything. If you do this make sure you put a towel on the back of the valve cover to keep the engine from smashing all the pipes on the firewall. Once the transmission has been pulled back far enough to clear the dowels you need to twist it in place clockwise if you're sitting behind the transmission. This will rotate the starter down towards the ground. The starter bump seems like it might clear if you twist the transmission the other way but it definitely won't. I have scraped the shit out of my transmission tunnel trying so learn from my mistake. You will need a center punch and an appropriate size drill bit and screw to pull the rear main seal. Then use vice grips and preferably a slide hammer attachment for those vice grips to yank the seal out. Do not let the drill or screw contact any part of the crank and clean the engine carefully after removing the seal to avoid getting metal fragments into the engine. I used a Slide Hammer and Bearing Puller Set, 5 Piece from Harbor Freight to pull the old pilot bearing. The "wet paper towel" trick sucked and just got dirty clutch water everywhere. Buy the tool or borrow it from a friend and save yourself the pain. It comes right out. Mine was very worn compared to the new one and it was starting to show cracks. Soak it in engine oil for a day in case yours has lost all of the oil to the plastic bag it comes in. You may be tempted to get the Nismo aftermarket pilot bearing but local mechanics have told me that they fail prematurely and if they do fail they do far more damage than a failed OEM pilot bushing. I mentioned this before but the Super Coppermix Twin clutch friction disks are in fact directional. The subtle coning of the fingers in both cases should be facing towards the center of the hub. So the coning on the rearmost disk closest to the pressure plate should go towards the engine, and the one closest to the flywheel should be flipped the other way. Otherwise when you torque down the pressure plate it will be warped and if you attempt to drive it like this it will make a very nasty grinding noise. Also, there is in fact an orientation to the washers for the pressure plate if you don't want to damage the anodizing. Rounded side of the washer faces the pressure plate. The flat side faces the bolt head. Pulling the transmission from the transfer case you need to be extremely careful with the shift cover plate. This part is discontinued. Try your best to avoid damaging the mating surfaces or breaking the pry points. I used a dead blow rubber hammer after removing the bolts to smack it sideways to slide it off the RTV the previous mechanic applied. I recommend using gasket dressing on the OEM paper gasket to try and keep the ATF from leaking out of that surface which seems to be a perpetual problem. Undoing the shifter rod end is an absolute PITA. Get a set of roll pin punches. Those are mandatory for this. Also I strongly, strongly recommend getting a palm nailer that will fit your roll pin punch. Also, put a clean (emphasis on clean) towel wrapped around the back end of the roll pin to keep it from shooting into the transfer case so you can spend a good hour or two with a magnet on a stick getting it out. Do not damage the shifter rod end either because those are discontinued as well. Do not use aftermarket flywheel bolts. Or if you do, make sure they are exactly the same dimensions as OEM before you go to install them. I have seen people mention that they got the wrong bolts and it meant having to do the job again. High torque impact wrench makes removal easy. I used some combination of a pry bar and flathead screwdriver to keep the flywheel from turning but consider just buying a proper flywheel lock instead. Just buy the OS Giken clutch alignment tool from RHDJapan. I hated the plastic alignment tool and you will never be confident this thing will work as intended. Don't forget to install the Nismo provided clutch fork boot. Otherwise it will make unearthly noises when you press the clutch pedal as it says on the little installation sheet in Japanese. Also, on both initial disassembly and assembly you must follow torque sequence for the pressure plate bolts. For some reason the Nismo directions tell you to put in the smaller 3 bolts last. I would not do this. Fully insert and thread those bolts to the end first, then tighten the other larger pressure plate bolts according to torque sequence. Then at the end you can also torque these 3 smaller bolts. Doing it the other way can cause these bolts to bind and the whole thing won't fit as it should. Hope this helps someone out there.
-
Major thread necro but how bad of a job is it to DIY? Looking at it online it looks like if you reuse your ring and pinion as long as those are in good condition it should be fine to just pull the axles/front cover and replace the diff that way? Or should I be replacing everything and doing preload measurements/gear mesh testing like the factory service manual mentions for the rear diff?