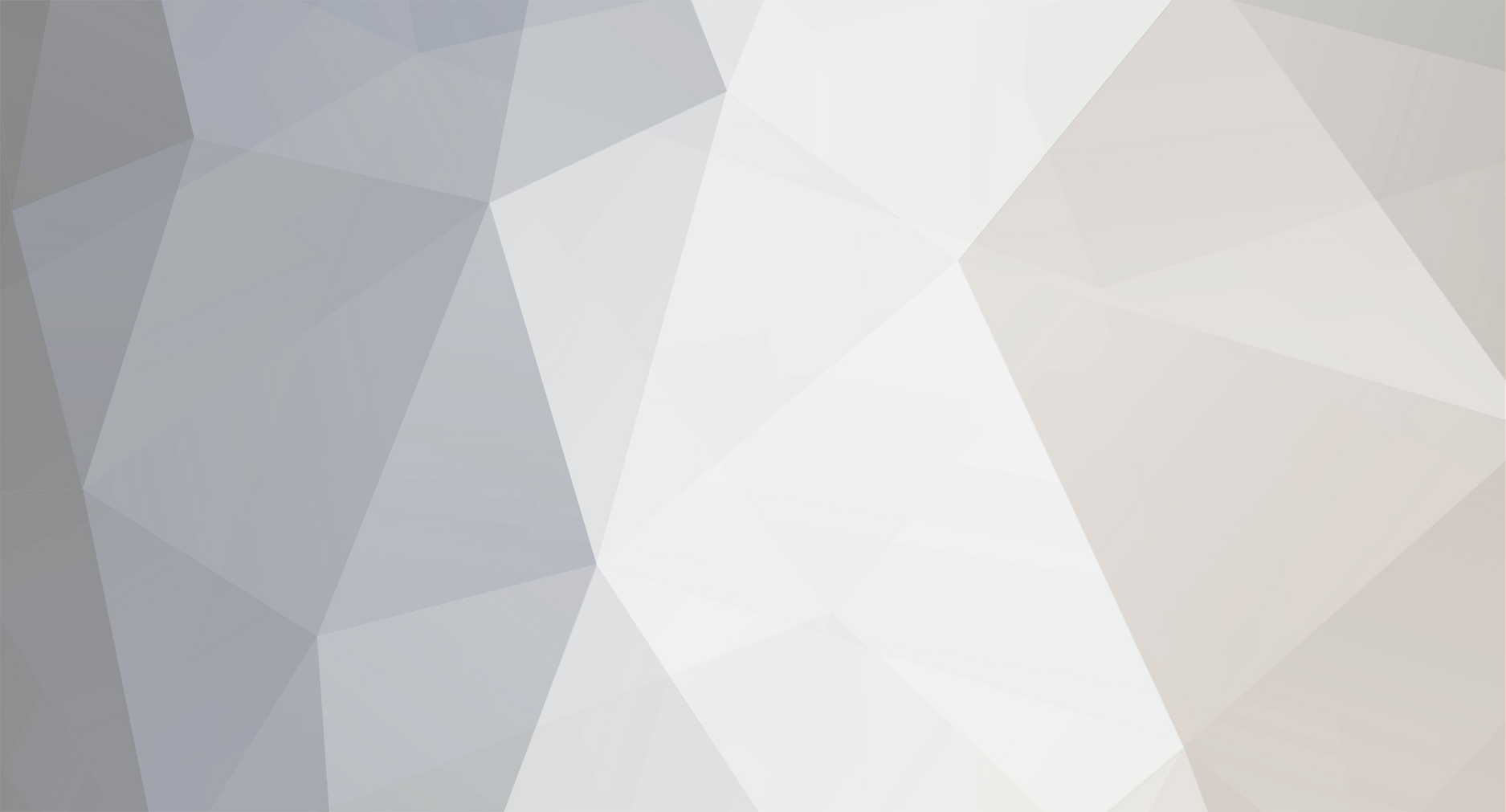
shanef
Contributor-
Posts
12,027 -
Joined
-
Last visited
-
Feedback
100%
Content Type
Profiles
Forums
Events
Gallery
Media Demo
Store
Everything posted by shanef
-
Yep i've never put one in a car so never had to worry about it. I cant see it being a huge problem though, worst case it may need a few 'hollows' filled with weld on the inside of the wings for the head of the bolt to seat against. I'll find out soon though
-
1 problem i see with running a rubber hose from there would be that it wont last too long with all the heat from the manifold. Should really run a drain form the back of the head
-
Actually, another way would be to get some 12mm solid tube and bash it into the existing holes instead of welding
-
Easily done. Just weld up the original holes, bolt on the backing plate and drill the new holes. I'd probably use some cap head bolts aswell
-
have a search on gtr.co.uk/forum dave, i remember seeing atleast 1 setup on there. but form what i recall its like the kakimoto hi-deck where its a compression deck with liners
-
Damn you, now im going to have to go up the back and fit a box to the dummy engine now to check. i'll be back...
-
The ones on the wings? Slot the wings, or if ur pedantic fill the old ones and re-cut them.
-
nope, rb30 block is taller by 38mm
-
10mm, same thickness as the normal adapter plates For someone to replicate something like these girdles from scratch they are going to have to spend the same sort of coin, u cant just look at a few pics, knock one up and expect it to fit. If you were to hand out the models then thatd be a different story
-
By all means fire away rob! Id rather get every bit of criticism now and make changes to it than to find out the problems down the track.
-
this has bene said alot lately but i'll say it again. the head makes the power, so u cant really fairly compare a std head with a modified head
-
yeh, like none
-
No no testing yet, very soon though.
-
the 30 would have loads more midrange though, and itd carry that peak power (or similar) right to redline. so say redline on the 20 was 7500 and on the 30 it was also 7500, the 20 would only have a peak power band of 1000rpm, whereas the 30 would have a peak powerband of 2900rpm i dont understand the way ur thinking about that
-
Hmm you've got me intrigued on the o-ring idea. I've got access to a spintron so i might look into setting an engine up on it and letting it run to see how it holds. Yep knew it'd be that much of a pita, hence i ruled it out. Your probably actually losing money on them too with the man hours involved.
-
who'se head is better though? (shutup they are both mangled) and ur gtrs' were red r racing spec apples with apples?
-
rich as a mofo. would be robbing quite a bit of power
-
U say ur not super brainy but theres a great idea right there. It wouldnt be hard at all to o-ring it, and without looking at one on a block i think theres enough room too. Saying that have you tried it on any of your adapters? The only way i could see doing the internal pickups was to get the bends custom mandrel bent, i couldn't work out a way to get the angle low enough out of the block so a)it wouldnt hit the tube and b)u could get a nut/bolt into the flange. I raise my hands in praise to yours and rob's efforts on that lol
-
Intercooler Clamps......not The Average Sh!t
shanef replied to N1GTR's topic in Engines & Forced Induction
The main difference between the cheaper 'wiggans' style joiners and the proper wiggans joiners is the angle of flex that is allowed in the pipes. The wiggans have a flex angle of upto 30deg and the cheaper ones only have a 5-10deg flex. So the cheaper ones would be very similar to just welding all ur pipes together The other problem u could come across is the fact that some of the pipes maybe coming together at an angle, and not directly square to each other, that angle could cause the clamp to not give a 100% seal. How often do you guys properly pressure test ur intake system? i.e hooking an air compressor upto the air intake and feeding pressure into the system (making sure all obvious breathers etc are blocked off) This is a very easy way to make sure your coller pipes dont blow off and tracing any annoying air leaks. they are the ones noel was talking about earlier -
Epic post jesus Heres a question i have for those brainy ones out there and for all to discuss: With the aftermarket girdles and the adapter plates, where/who would you get in contact with to make some proper gaskets? It would save the hassle of using damn sealer all the time. This would also be handy for the aftermarket girdles as an un-even thickness could play with the clearances.
-
Well i'll start with my adapter plate kits, exactly the same as the rips or pro-engines one except i'm not including a pickup, too hard to do as i cant weld and can't find someone local to do them. Reason its too hard is the pickup on the rb30 sits in the centre of the block, which is exactly where the axle tube sits in the 4wd sump. You could do it easily if u used a ~15mm adapter plate, but then youd have cross member clearance issues. The pickup on the rb26 sits at the front of the engine, away from the axle tube. So all my kits are sold with the plate which is fully cnc machined from 5083 ally (has a higher silicon content so aids in thread strength) with the edges chamfered, high tensile cap head & hex head bolts, washers, template to bolt to the block to drill & tap the extra holes & notch the block on the diff side & of course instructions. Priced at $650 retail. Pics: Next are the billet girdles. I started work on these approx 18months ago with the first design being a 2 piece. It consisted of a piece of billet approx 40mm thick which mated to the std main caps that were machined down to suit, this was much similar to the way rob does his aftermarket girdles with individual caps but his being billet (and of course alot stronger). It went into a local circuit raced gtr and there were no issues what so ever after a tear down was down when a turbo let go. Along the way a few people raised the question of whether a 2 piece girdle like that would actually induce cap walk, being that there were now 2 plates holding the bearings in place, turned out there wasnt an issue and i see rob has gone an extra step with adding 2 extra high tensile cap heads per main cap that bolt the adapter plate to the billet caps (nice thinking rob). I then started with the single piece design and was contacted by a workshop over christmas which gave me a hurry up to get the design finished and the prototypes made. There are alot of unknowns and unanswered questions that need be figured out with the test car, so these wont be ready for sale for a few months yet. Price for these are $2250 for a rwd girdle and $2450 for a 4wd girdle. Basic design is to give maiximum strength across all 7 caps by leaving as much meat in the end wings as possible and tie it to the side of the block. Started by getting both the block and std girdle digitised and then designed it from there. We also did some stress analysis to check where the critical areas were and made the appropriate changes to suit. Next was material selection, which ended up being 7075 alluminium which probably is overkill, but its better to have it stronger than its needed. Fitment wise is much the same as rob explained earlier with all the casting dags being removed, and in my case the std oil pickup tube mahinced off. To leave it there would weaken the middle cap more than what would be acceptable. Mainstuds are still the std M10x1.5 arp issue, but this time using a full set of the longer studs as found in the std arp kits. Recesses are cut into the top face to suit. The cap faces are faced dead square to both top and bottom decks, and 15thou is left on the tunnel. So the block being used needs to be line bored to suit, and this part is essential that it is done 100% accurate, any wobble in the boring machine will give incorrect clearances. Also when its line bored, radius' need to be put onto the bearing edges. We are unsure of what clearances we are going to start off with as we dont know what role thermal expansion differences will play, short life but tear downs will give us the answers. Enough babble and on with the pics: Early 2 piece setup: New single piece setup:
-
Sorry rob while u were busy working i was just sitting on my bum on the computer as only a good aussie does so i thought i'd reply on your behalf. Pass that sarcastic face please Re the sealer drying 'issue', i'm half looking into getting gaskets cut to make that process alot easier. Then thatd also give a consistant thickness so it wouldnt affect the clearances with the aftermarket girdles. Have u thought about doing something like that too? I'll put that idea into the adapter plate thread so it can be discussed there too
-
well why dont u stop fluffing about and put the damn parachute on, hell i'll send mine down if you want.
-
Ahh k gotcha, yeh they do make the normal sump adapters
-
maybe?...