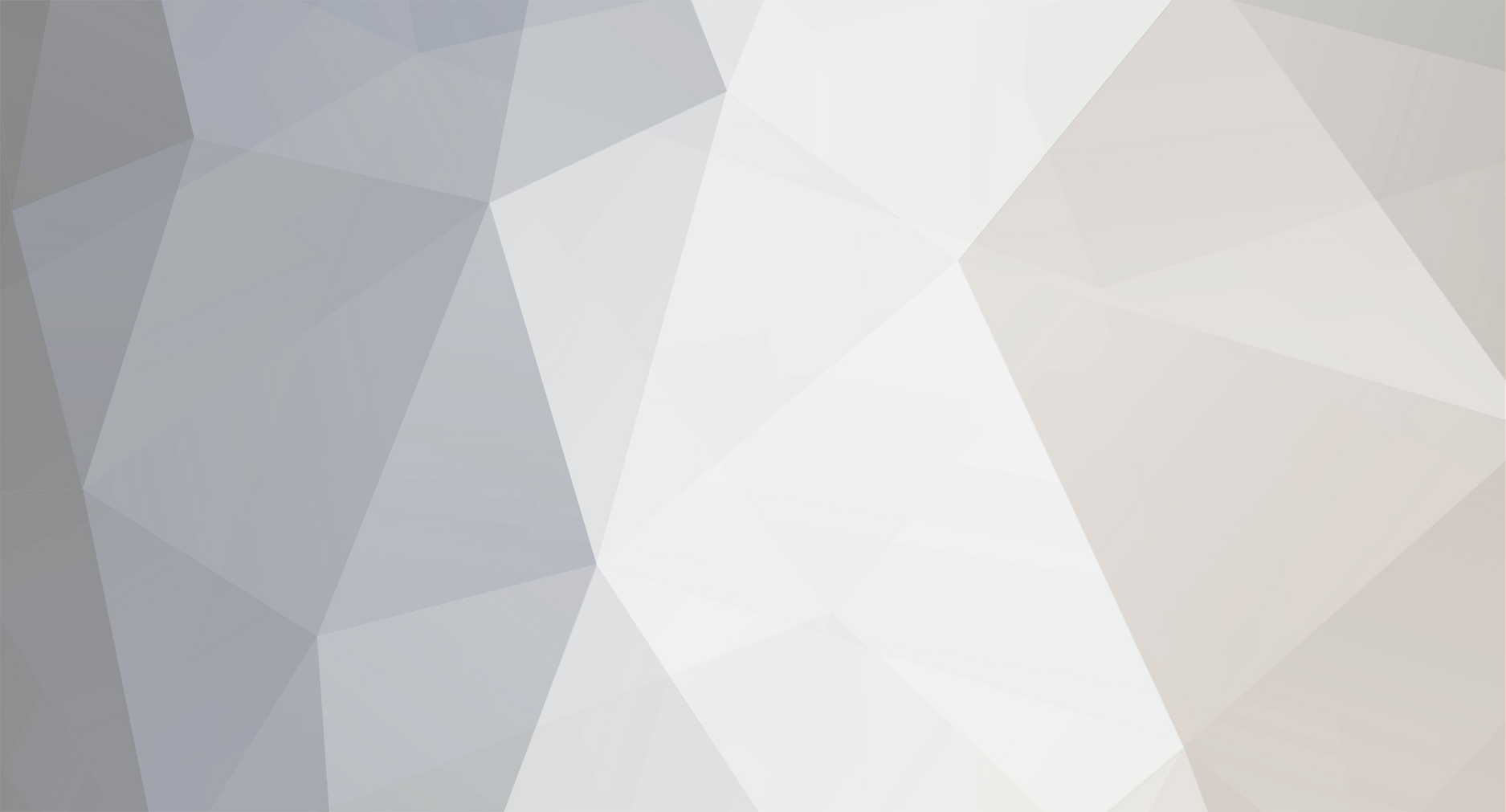
urtwhistle
Members-
Posts
632 -
Joined
-
Last visited
-
Feedback
100%
Content Type
Profiles
Forums
Events
Gallery
Media Demo
Store
Everything posted by urtwhistle
-
hmm my Rb3025 came up with 155 and all the rings were lined up lol
-
ouch that can't be cheap being an auto too
-
Hey so it turns out that 4tho shim is still too tight and I can't get the oil pump gear on. which is a pain when I know that if the gear is in position I can push 2x 6 tho feeler gauges under it. Also Loctite 406 is not a valid option as it is extremely hard to get it to key on and stop the shim from peeling off. Thats If you are quick enough to actualy get the glue on without gluing the shim to your hand first. My boss suggested using Loctite 680 high strength retaining compound. So I'll let you know I go with that experiment. At the rate I'm going this motor is going to take about 2 years to get running. Almost give you a run for your money ay Bubba????
-
I think you might be right but I no longer have the neo Rb25 block to mic it up. I went with the 4thou shim and its still possible a bit tight. I'll have more of a look tonight now that the glue has dried and I can take the sharp edges off the shim.
-
I think you hit the nail on the head, I totally didn't even take into account the runout of the crank. I might do a few experiments with different shimming and see how tight I can actually go before its a PITA to fit the oil pump.
-
Hey Mr Bubs, In hind sight I think your onto something and I probably should have gone the welded route. 12 thou makes the oil pump gear rock back and forth like its on a rocking chair. I don't understand why there isn't alot more post's relating to this subject I mean its so damn obvious to me lol
-
Hey guys, I have done a bit of a search and can't find any thing that helps. I have just had my rb30 crank machined and a crank collar put on. I just test fitted the oil pump gear on the collar and noticed there seems to be a lot more clearance than what I would have expected. I measured a total of 12 thou, Ie 6 though on each flat face. Firstly is that normal? that amount of slop I would have expected to negate the whole purpose of the collar. Do people shim up there gears? I'm think about getting 2 small peices 4 thou shim and loctite 406'ing it to the crank collar just to tighten it up a little. I noticed tonight that the glue added about 1 thou. so In theory it would bring it down to about 2 thou. What does every 1 else do? Lastly when using a standard rb25 pump on a built rb30, do people put say a 2mm washer in the oil relief valve? regards Chris
-
Do Sr20 Arp Rod Bolts Fit Rb30E Rods?
urtwhistle replied to bubba's topic in Engines & Forced Induction
Yes they do fit and I have half a set left over if any 1 wants to make an offer for. There is about 2 - 2 1/2 threads left over after the nut has been done up. regards Chris -
wow any 1 who chooses a laggy pig over a street friendly setup has got rocks in there heads
-
Those new swifts are bloody quick around the ring. I was in a 3 series beemer (diesel turbo) and they were blowing past us. no chance against the DB9 that I went in tho lol. I sooo badly want to go back
-
I find this website very handy for id'ing turbo's http://www.turbomaster.info/eng/
-
and I ment to say NEO being better than rb26 cams
-
After thinking about this thread I called "southside engine centre" who do some very nice engines and discussed machining the base circles to suit more lift. The main problem that I never thought of was that due to the NEO and 26 heads having solid lifters would mean reshimming the head with much bigger shims. Which runs a higher risk of spitting a shim out and smashing the cam. They strongly suggested not going this route and fitting an after market cam that didn't require using big shims. That might not be such an issue in a hydraulic head though. The link below shows that a NEO ex cam would probably be better then a R34 ex cam. It has more lift but only slightly less duration. http://www.tomei-p.co.jp/_2003web-catalogue/e090_camshaft-specs.html
-
soooo am I reading this correct. I could put a 26 exhaust cam in my neo head????
-
You are correct, for your situation you might be better off doint it that way and blocking the BOV return pipe. In mine I knew roughly where the leak was so it wasn't really an issue.
-
The problem with only blocking the inlet of the turbo will cause the air to go back out of the blow off valve. another way would be to block it at the turbo then block it on a rubber joiner before the cast aluminum 90 deg bend that runs to the throttle body. which will stop the waste gate from leaking back to after the AFM.
-
unfortunatelysince my motor is out it was a little hard to get a good photo. But as you can see remove the cross over pipe and block it with a pvc pipe end cap (use pipe clamps). remove the pipe from the pressure side of the turbo. jam a cricket ball or another PVC fitting in t. You can either pressurise the system through the bungs that you run to your waste gate or leave them all hooked up and drill a hole in 1 of the pvc fittings. I set the regulator on my air compressor to about 20-30psi. Ay that pressure it is very easy to hear a leak. The main leak on my car was where the inter cooler had a bracket attached to the bottom. They had accidentally drilled into the core. Which I ended up blocking with araldite. I hope that helps.
-
its easy to test for a pressure leak. all you need is a $2.00 pvc fitting from bunnings and a cricket ball. I will take a photo tonight and show you how to do it. PS I think your missing the point about the actuator. the PSI rating is irrelavant. Its the surface area on the diagphram inside the can that makes a very large difference to how quickly it reacts. And I find it extremly strange that a company like Ovaboost can't log the boost response. it's 1 of the most simple tools that they would use.
-
well if its that recent then it's ovaboosts dyno which reads very close to Hyperdrives, How do I know? cos my car has been on both with in a week of each other. I seriously think your chasing the problems in the wrong area's. Print and overlay yours onto my sheet or mine onto yours and scan it and post it on here. That way we can compare and see possible reasons to why its not making power. I can barely see on those print outs. But it looks like its exactly the same untill about 5krpm then it slowly comes up to where mine was. have you got prints with the boost graph. That would be very interesting to compare. I originally ran the standard wastegate, then I put on small can 14psi wastegate that Stao supplied and my car ran like shit. Then he supplied me a big can 14psi wastegate and it ran a lot better from that day onwards. What area do yo live , PM me and you could borrow it and test how it or compare setups. (since there so damn close)
-
I also would love to see some 1 do a direct comparison. the problem is any decent drop in cam means deleating the VCT. The stock cams are actually extremly good and longer duration cams just make it a dogg in low range. The real downfall of the stock cams in my point of view is actually the amount of lift not the duration. I would love to see the comparison between standard and standard with the cams welded to suit an extre 1 or 2mm of lift as the only change. Chris
-
I have said it once, and I'll say it again. Hyperdrives dyno reads low. My RB25 R34 with my stock turbo and 15psi did 245hp. My Hypergear highflow pulled 300hp at 18 psi on my Rb25. my (very sick) RB30 with a GT3576 did 370. You just can't compare dyno results from the east with hyperdrives. your best bet is to overlay your graph with mine as there both on the same dyno, same cars, same turbo. CHRIS'S R34 DYNO3.pdf
-
Rb25 Neo / Xr6 Injectors Same Same?
urtwhistle replied to Justa32's topic in Engines & Forced Induction
certainly do Harey -
Rb25 Neo / Xr6 Injectors Same Same?
urtwhistle replied to Justa32's topic in Engines & Forced Induction
no there not a direct fit but quite simple. there are two lengths of injectors. I have the long 1s which are alot more work then the shorter. -
No problems with the sump clearance. I lowered the motor on the engine mounts as per R33 specs and no problems still.
-
See Mrsparkles I had a similar issues with AA, and they didn't do things I asked them to do and arrrrrrrrr don't get me started. BUT i believe that these issues could have been a once off. Every company makes mistakes every now and then. what I have learnt is do not pay a cent to any company until you have inspected and MEASURED every thing a company has been asked to perform.