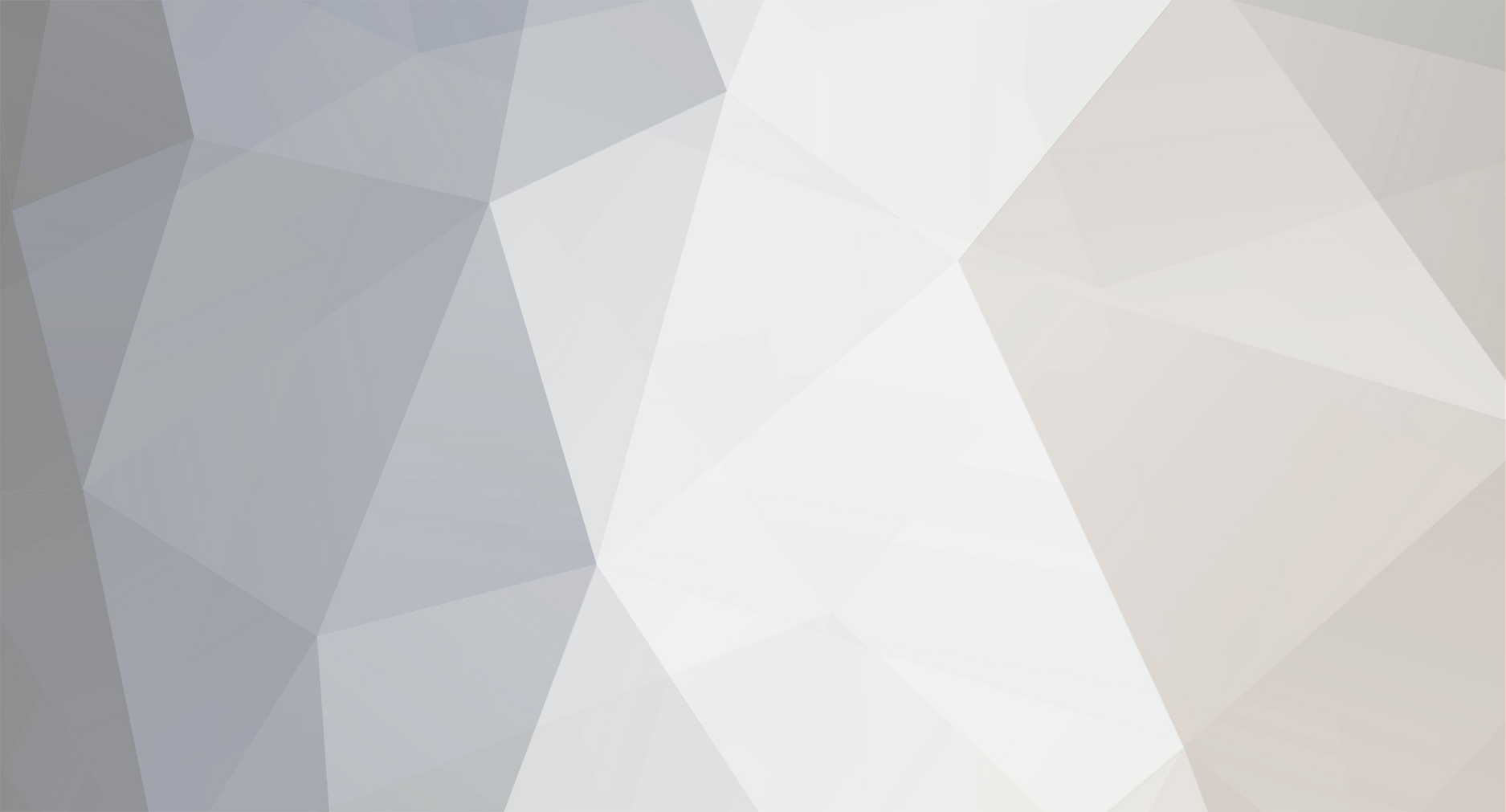
nissan200sx.dk
Members-
Posts
225 -
Joined
-
Last visited
-
Feedback
0%
Content Type
Profiles
Forums
Events
Gallery
Media Demo
Store
Everything posted by nissan200sx.dk
-
Hi. Am wondering If there are any nissans in europe that used the RB30 block. I live in Denmark, and am thinking of building a RB25/30, but need to source a block.
-
Yes, but i have the VG30 bolts. Arp make connecting rod bolt washers.. Can i use those to compensate? I can make my own hardened washers, but need to know what HRC they are.. Also do rods need to be resized after a bolt change? What if i dont do this? Because engine is assempled.. and would hate to tear it apart now, and need to buy a different size bearing now. :-(
-
Hi. Just got my vg30 rod bolts from ARP for my RB25DET s1... But looks alot like the Nut will run out of thread when put together in the rod? Do I need to ad a shim or? Thanks for any help.
-
So it should all be good? And ready for use then? Thanks alot for the help
-
Endfloat is: 0.08mm Run out, measured on number 4 main bearing, is 0.015mm. This is total what the dial show. Souldnt this be cut in half to get correct run out number?
-
Thanks for all the replys. If it is clearance issues why does it change then? Its ONLY when it has been sitting still for a little minutte, it "binds". Have measured accuratly today with a torque dial gauge. (built in dial gauge), range 0-8N. Its calibrated 2 times a year. To break the "bind" it need ~6 N. To rotate it need ~2N, after the "bind" has been broken. If I start rotate just after stop, I still need ~2N. If I wait 15 sec, it need ~6N to begin rotation again. (If I wait 5 min. it still is 6N to begin rotation) There is NO spots were it need more or less N to keep rotation. Have talked to a engine builder here in Denmark. He says when the crank rotates it draws oil on to the surfaces, 2N friction, when it sits still the oil runs back in the grooves, and crank makes contact with bearing, that is what I need to overcome? The block is upside down, and havnt tryed doing this when block isnt upside down. Could this have any influance? Tomorrow I should check for endfloat, and run out on number 4 bearing? What more should I check?
-
Have measured both crank and cradle, ordered correct bearings, got the ordered bearings. Mounted with clean surfaces (back side of bearing) and used plenty of motor oil to lubricate. When it is turning it feels free and top nice. My only concern is what it is that is "holding" it when it hasnt rotated for a minutte or so. What i need to overcome for it to turn.. Could it just be oil friction? Because when using the tourque dial gauge the applied force to get it turning (when i have to overcome what is holding it) is only just the needle moving, only just moving, not even up on the dial... But when it has just been turned, and then turned again there is nothing holding it. The needle doesnt move to turn it. Tomorrow i will try with a different tourqe dial gauge. goes from 0 - 8N. Should be apple to see more accuratly.
-
The applied force just need to be a little higher to get it to turn over when it has been standing still for a little minutte or so. After it has begun to turn the applied force to turn it is close to nothing. It turn freely the hole way round. There are no spots were it feels more or less freely to turn.
-
ohh, and yes, every bearing cap was well oiled.
-
All grooves in bearing caps are faceing up, (top of block). The notch in each bearing cap is correctly mounted.
-
Hi. Have a question about me RB25DET s1 engine that im building. My tourque wrench is one from work, our test department uses it. Its calibrated 2 times a year, and uses a dial gauge built in it. Goes from 0 - 80Nm. Just tourqed down the main cradle, but now my crank sort of "binds". When the crank just has been turned around, it will spin free, and only require ~2 N to be turned. (You cant really measure it as it really doesnt move on the dial.) Easy to turn by hand. When the crank hasnt been turned for a minutte or so it "binds". Will need around ~5 N to get it to spin free again. (On the dial gauge you can only see it move, and then drops back to nothing as the crank begins to turn / frees it self from the "bind") Is this just oil friction I have to overcome just when turned? or?? Could this be a problem? Best Regards Ronni
-
Modded Rb25det Rods..
nissan200sx.dk replied to nissan200sx.dk's topic in Engines & Forced Induction
Can up the revs to 7500 rpms? Or maybe 8000 rpms? Turbo wise im currently on a GT3076r, exhaust A/R 0,82, That cant get me ~550 flywheel HK? But have the possibility to get a GT3582r dirt chep. (sponser deal with a turbo company) Should I move up in turbo? Cams are still std, but will be changed soon. -
Modded Rb25det Rods..
nissan200sx.dk replied to nissan200sx.dk's topic in Engines & Forced Induction
Hi. Have done them, RB26 rods are hard to get for me in denmark.. Aftermarket rods are too expensive, am under education, so dont make alot of money right now.. But was just looking for ~550 hk at the flywheel anyways.. So if the RB25 rods i have polished, balanced, and get ARP bolts for will be fine for 550hk, that is great! -
From the album: RB25DET rebuild
-
From the album: RB25DET rebuild
The new fresh engine block.. My current head has been fully renewed, and will be used together with this block when I change. Will prob do it between christmas and new year. -
Hi. Std RB25DET s1 rods, they are polished, balanced, and I will be using ARP bolts with them. How much power can they handle you recon? Can I push them to the 550hk mark? Car will be used for 1/4, and trafic light race...
-
Problem is, its hardned to Rockwell C 36, so hard to make a hole in now.. I know, should have asked this first. My mistake..
-
My question is more on the way its fitted.. If it needs a pin throgh it, to be sure it wont spin on the crank. Now its mounted this way: crank was cold shrunk, collar heated to 100 degress, both parts degreesed, special glue, VERY strong and will hold up to 150 degrees, still needed 2 tons to be pressed on. (No I did not press 2 tons down on entire crank, a metal bar was fitted just down under the first counter weight.) Question is, do you think it will stay on and not spin round the crank. I dont know how much force there is trying to twist it around the crank.... How hard the oil pump is to drive..?
-
Thanks for replies. KN here can get the oil filter for the RB, they just dont have any home here in denmark.. And I need the oil filter now. hehe. So im just using filter for 300zx. Best Regards Ronni
-
Just a qiuck one. Oil filter from a 300zx (z32) is that okay, and can it be used on RB25DET engine? I live in Denmark, no skylines, so hard to come by. KN makes oilfilter for 300zx and i can get that here i Denmark.
-
Main Cradle, And Head Bolts..
nissan200sx.dk replied to nissan200sx.dk's topic in Engines & Forced Induction
Hi. Wont be using any "china" parts! The bolts are from work, were thay are used in "hydromats". Machine with alot of hydraulic pressure.. Low grade, or poor bolts simply wont hold up. So they are good quality. -
Main Cradle, And Head Bolts..
nissan200sx.dk replied to nissan200sx.dk's topic in Engines & Forced Induction
If you compare 12.9 specs with ARP2000 bolts they are both quiench and temper steel. Both have almost same Rockwell C hardness. The ARP2000 bolts have a little higher tensile strength 200000 - 220000 psi, the 12.9 bolts have 160000 psi. The 12.9 bolts have their thread rolled, not cut (Stronger) So cant see why a 12.9 bolt wouldnt be better than std as main and head bolts. Have seen cars run with 12.9 bolts as head bolts.. The main std bolts of a RB engine, dont they come from a Datsun 1200?? So wouldnt a 12.9 bolt there be stronger also?? 12.9 bolt info -
Main Cradle, And Head Bolts..
nissan200sx.dk replied to nissan200sx.dk's topic in Engines & Forced Induction
Hi. I'm a little confused.. Only for main cradle now: I know the tourque settings for theese 12.9 bolts. Can I use them instead of std bolts? Would it be stronger than std? Head bolts: Also know tourque settings for theese 12.9 bolts. Can I use them instead of the std head bolts? Would they be stronger? Thanks for reply, and sorry for me being a bit slow. hehe -
Main Cradle, And Head Bolts..
nissan200sx.dk replied to nissan200sx.dk's topic in Engines & Forced Induction
Okay. But when using aftermarket bolts that are stonger wouldnt you get the same issues? So bottom line is I shouldnt use 12.9 bolts for main cradle nor head? -
Main Cradle, And Head Bolts..
nissan200sx.dk replied to nissan200sx.dk's topic in Engines & Forced Induction
I'm building a all std RB25.. But the bolts we have at work, so was just thinking it they are better then i would use them. Thanks for reply