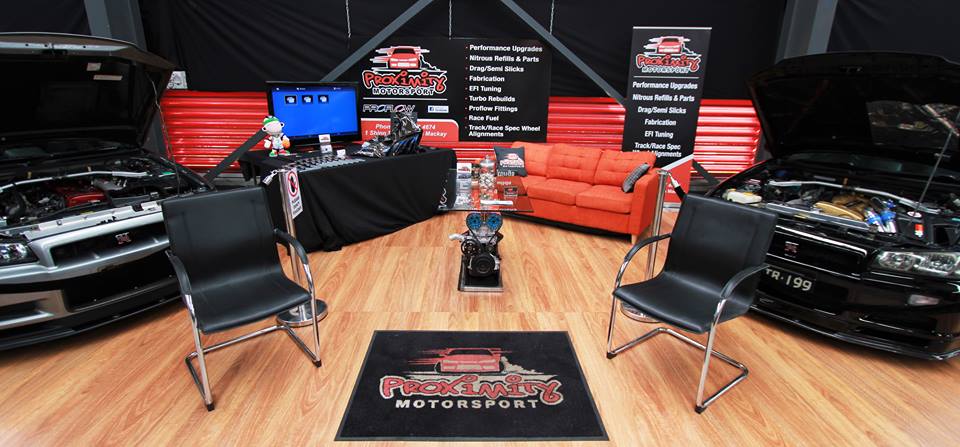
Proximity Motorsport
Members-
Posts
654 -
Joined
-
Last visited
-
Feedback
100%
Content Type
Profiles
Forums
Events
Gallery
Media Demo
Store
Everything posted by Proximity Motorsport
-
hey guys I'm still having drama. Everything looks electrically okay. I have tried THREE Cas's now and they were all working when removed from motors, one working earlier the same day, so definately not a faulty CAS. To check if the coils are getting signal would putting a timing light over the white wire on coil one work? I'll try this when I get home, at work atm. Have you guys got any other ideas before I start pulling the loom out to change it out for another The Haltech had a plug in patch loom. What do you mean with the LED test light? How would I check it? Just put light to ground and to one of the incoming signal wires of the coils? So the signal is 12v?
-
Yes it is, and its out of the motor, although it has been sitting, but was working perfectly okay before. The spare I used is from a R33 that was crashed, and was working perfect before the crash.... hmm maybe I should call around and get a mate to bring a spare around if i can find one. Is there any way of checking what the signal is getting to the coils? Is it as simple as checking with multi meter?
-
Hooking Up Plumb-back Bov On R32 Gtst
Proximity Motorsport replied to cogs's topic in Engines & Forced Induction
I have a Greddy Tyre R BOV and here is an example of another way of routing your bov back to intake. It doesnt have to be from the factory location, and all you need to do is get the air back to the intake pipe. -
Hey, I am putting back together an R33 GTS-T 1995 model and basically the previous owner decided to strip it and I decided to put it back together. Previously it had an RB25DET NEO but I think its just a rb25 S2 loom because the ECU plug only has 2 rows, and there is no ignighter pack plugs 1995 S2 R33 GTS-T Shell S1 RB25 Motor with NA S2 Coils and CAS S2 RB25 Loom S2 AFM Standard S2 Turbo ECU The car used to have a patch loom with a Haltech E11v2 and wired into the standard loom was a Apexi SAF-C and AVC-R and today I removed all the splices for the SAF-C and AVC-R. The car IS NOT sparking or firing the injectors... this is what I have done so far.. The only wire that was completely cut was Pin 27 (AFM Intake air quantity signal) its solid grey in colour. The car did have a map sensor with the Haltech but I have put a S2 AFM back into the car and none of the wires to the plug were cut or tampered with. Anyway I joined the grey wire back to itself, and when it is plugged into the ECU I found continuity through that signal and the speed and rpm signals although there was alot of resistance. Im not sure if this is okay or not. Anyway the fuel pump primes when the ignition is turned on, the car cranks, but does not fire. There is fuel getting through the rail. So these are the things I've tried and nothing has worked.. The ECU is getting power and a good ground and I have tried 2 ECUs The CAS is getting power, and ground, and signal wire 51 (120 degree) and 52 (1 degree) both have continuity to the ECU The injectors have power to the main harness although I did forget to check on the plug (I know) The coils have power and ground to all of them, and the signal wires all have continuity back to the correct pins on the ECU (Pins 1,2,3,11,12,13) Unbolted a coilpack and put a spare plug in and tried to crank motor with it earther on chassis and motor and no spark When unplugging and plugging back in the CAS it primes the fuel pump and I tried 2 different CAS's and no difference I removed the CAS from the cam and turned the shaft the correct direction (with power on and everything plugged in) and there was no spark coming from coils and could not hear the injectors ticking The main earth on motor is connected to chassis, and all other earths on the loom have been sanded clean, and then paint was removed with a dremel from chassis and they are all tight and connected (as far as I can see!) So is there anything I'm missing here? Is there any way of checking what signal the signal wires are getting on the coils? Is it a positive 0-5v signal? I dont really know alot of auto electrics. Thanks
-
Im a fitter and turner so yeah I do have quite a good mechanical knowledge. I have never built a diff which is why I'm asking. And yes I do have a magnetic base dial indicator, and yes I do have bearing blue to check meshing of gears. And I have rebuilt many worm drive gearboxes so I know the mesh patterns. To me the idea of these diffs is stupid, compared to the nut type, where you just tighten the nuts to get the backlash and preload on bearings. I didnt think of looking through the GTR manual, but I do have one somewhere, I'll check it out. So I suppose maybe nissan could help me out with these shims. At the end of the day if I spend $20 on 20 shims that should see me through to get it right, Id be much better off having the satisfaction of doing it myself and not spending $300 odd at a diff place that really dont give a f*ck if they get the diff spot on or not. Thanks for the advice for those of you that have helped out. I'll see how I go with this and I might do up a tutorial
-
Rb26 Gearbox Rebuild
Proximity Motorsport replied to DVS JEZ's topic in Suspension, braking, tyres and drivetrain
nah I have never done it but I know someone who did it to his box while it was apart, and he said it worked well -
Rb20det Runing On 3 Cylinders
Proximity Motorsport replied to falky929's topic in Engines & Forced Induction
Do you mean you pulled out coil from cyl 1 and put a old plug in it, and earthed the plug somewhere on the car and cranked it, and the coil is firing the spark plug okay? If thats the case, then maybe its your injectors? check all your injectors are getting power to each plug. If its got spark and its not firing, then it probably doesnt have fuel. Maybe your injectors are completely buggered, or maybe they are dirty. Did it just "happen" one day, or have you done something to your car and now its not working? -
Vipec And Frying Igniters
Proximity Motorsport replied to Scooby's topic in Engines & Forced Induction
I had a vipec and a Morrison? Ignighter... And I never have had a problem in 12 months - 15,000km -
Toyo Proxes 4
Proximity Motorsport replied to johnnyt's topic in Suspension, braking, tyres and drivetrain
Had them on my old r32 215/35/18 on fronts, and when they got old I put them on the rear and they were ALOT grippyer than brand new 235/35/18 Nankangs I usually had on rear. Not that Nankangs are much of a tyre, but I was very happy with the proxy 4 all the time, exept one delimitated on front due to 2.5 deg neg camber, and shop told me it's my fault for "shitty" camber so no refund. They lasted 10,000km on front -
Hey. I put a nismo centre into my r200 from r33 the other day, and when I put it back together, there was shitloads of backlash. I didn't check before I pulled it apart but im assuming the centre is maybe machined slighlty thinner on one side, causing the shims I re-used not so effective. I haven't had huge exposure to diffs, but I know in a Patrol diff, there is nuts on either side that you can adjust to set preload and backlash.. and what an easy, effective way of doing it. The R200 diffs though use shims to get preload and backlash though. My diff only had 2 shims on one side and 1 on the other.. I haven't measured them, but how close to perfect could it be, the shims are at thinnest, 1mm thick. So Im wondering can anyone tell me, if I need to add 0.25mm on one side or something how am I supposed to get such a thin shim in there, considering I had the use a soft hammer to tap the others in there in the first place. Or do nissan sell a HUGE variety of shims in steps of 0.05mm or something? (1, 1.05, 1.1, 1.15 etc) Can anyone please do a bit of a spiel on how to setup the backlash properly with these diffs, and what specs I should be aiming at. for preload on side bearings, I've been told with the patrols they tighten them until you can feel load on the diff when turning it by hand, then back it off 2 notches on the diff. Is this pretty much the same principal with the R200? Ill try get some photos and do a HOW-TO right up, because I can't find anything on the net about this, and there has been a few diff questions asked on here before. ps. just for knowledge.. do the R200 have a crush tube under the pinion or just shims? Cheers
-
Rb26 Gearbox Rebuild
Proximity Motorsport replied to DVS JEZ's topic in Suspension, braking, tyres and drivetrain
Just word of mouth here but it makes sense... If you have the syncros bead blasted (not sand blasted) then smoothe pitting makes them a bit grippy then standard so they grab eachother. -
check out NENGUN. They are having huge wheel discounts on rays this month only. up to 44% off I think they said. Plus the aussie dollar to yen isnt too bad atm either at 80yen
-
oh dear haha... Im using a GTR box so hope it holds up... Although I did just purchase a full set of 265/35/18 Federal 595 RS-R to go on the 18x11.5" rears and 18x10.5" fronts.... probably going to break a box........... or two. I got them from the guys at Option 1 Garage. I highly recommend them, and awesome prices on tyres.
-
Making Lobster Back Piping
Proximity Motorsport replied to Proximity Motorsport's topic in Fabrication
Scotty, thats a pretty nice dump. I just wish I had my motor in my car so I could practice re-doing my own exhaust haha. Chris you know as silly as it sounds, I didnt even think of that.. but its probably my problem. I do hold the torch on an angle, so I'll try standing it up a bit more. CPC that alloy I was welding was 2mm wall, I'm pretty sure that was the thinnest the supplier had and the next size up was 6mm wall. I have some 1.6mm stainless 2.5" pipe ill try some practice lobster backs. Is there any sort of rule of thumb for size of filler rod to use? Such as amps to mm or electrode size to rod size. One pretty handy tip I've found on the net that might help out some beginners is approx 30 amps per mm for alloy. Do any of you guys purge pipes with argon or any other gas to help reduce that slaggy crap under the weld, especially on stainless? I think I'll invest in a die grinder and do one weld at a time, then clean the inside of pipe with grinder, then next weld and so on. Any other tips please post. -
Hey guys.. I have been using a top of the line Kempi MasterTig 3 phase welder at work over the last 2 years we had it, just doing odd little jobs on it, and I really enjoyed welding things, there is so much satisfaction in making something yourself. So recently I purchased a 200amp 240v ac/dc pulse tig off ebay, brand is ProWeld, and its got a reasonable amount of adjustment in it. There is however, a very large difference in welding with a $800 chinese welder and a $6k+ Kemppi welder. There is a few things I need help on getting right. Now I haven't had any professional welding advice. Im a fitter and turner so its not in basic welding we do at tafe. First off.. The most annoying thing is, with the Kemppi welder I found that fusing aluminium with pulse at around 1.8 frequency was really easy.. but my pro weld tig set on 0.5 frequency and its still going at about 10!!! :@ so that makes pulse reasonably useless for me. So I have been welding with no pulse at around 50amps welding 2mm thick pipe 60mm diameter. And correct me if I'm wrong but you can't buy aluminium bends off the shelf and they have to be pressed from sheet? Well I'm building an r33 daily out of parts laying around the house and just making it a stocko pretty much, but it needed new cooler pipes so the most cost effective way for me was to buy a lengh of 6mx60mm pipe for $80 and make lobster back piping. And the welds arent that crash hot, and I'm not blaming the welder but more so my lack of experience. Although if I had a decent pulse I could turn the amps up a little and run over it and make it look good. The thing that is stuffing up most of my welds is the filler rod melting before I dip it in the pool, or when removing from the pool, and I would assume thats from not having enough heat in the material, but if I go any hotter it melts through! Any ideas? And the other thing is can you guys post up any pics of little jigs or anything you have made to help hold piping on the bench. I don't have anyone to help me so getting things to sit nicely on the bench its so hard, I have been using the earth clamp, grinding discs and files stacking them under everywhere trying to level it out. And as for the pipe, I set my saw at around 7.5 degrees, and welded a flat piece of aluminium onto the end of the pipe, and sit level on it, then clamp and cut, then spin pipe 180 degrees and get level again and take another cut and so on and just weld on as many pieces as I need. Is this the best way? Thanks guys, let the discussion begin
-
Okay so yesterday I finally fitted the s14 nismo 2 way into the r33 GTS housing. Im not too sure about the rear housing cover off the GTS diff though, it hasn't got any fins, and its got less oil capacity than a GTS-T or GTR one, so I might get a greddy extra capacity one, only because it will be too hard to find a diff cover alone. I had one out the back but its a 4 stud one for R32 cradle. Anyways the diff looks pretty, painted in metallic blue, really similar to the cusco colour
-
Aftermarket Fuel Rail For Side Feed Injectors?
Proximity Motorsport replied to 89CAL's topic in Engines & Forced Induction
I think you might be a little mixed up mate. GTR injectors are top feed. We are talking about side feed rails. -
Aftermarket Fuel Rail For Side Feed Injectors?
Proximity Motorsport replied to 89CAL's topic in Engines & Forced Induction
are you going to buy one Cal? I think I will so if you want to bundle shipping ill get one too. Ive been looking for these for a while, I want more bling