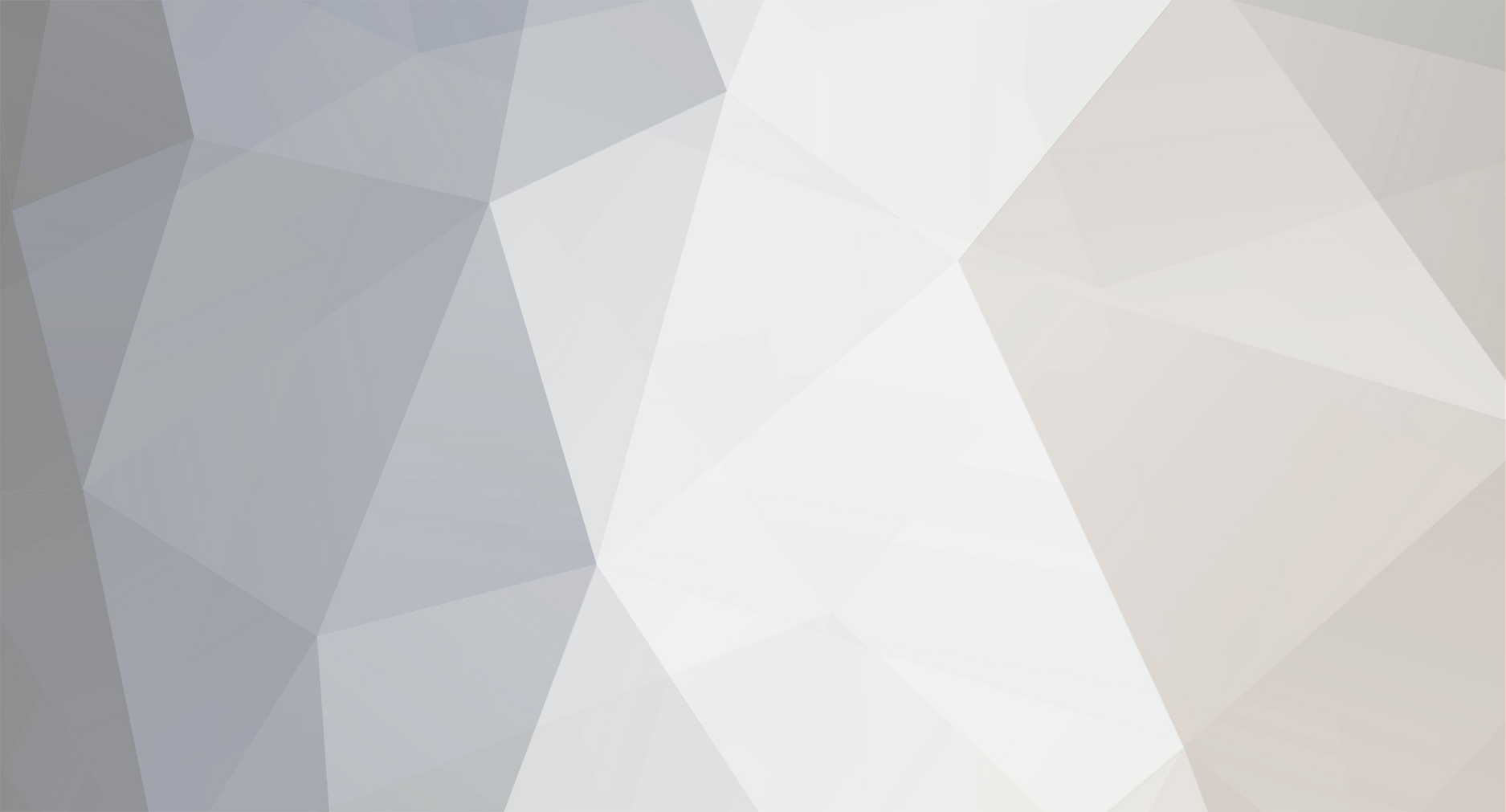
Jmaac
Members-
Posts
564 -
Joined
-
Last visited
-
Feedback
0%
Content Type
Profiles
Forums
Events
Gallery
Media Demo
Store
Everything posted by Jmaac
-
Now that you've changed the oil viscosity change the plugs. Plugs might now be too 'hot' (pre ignition), run a colder plug (lower heat range)
-
Thought I might get a few of these together. Links to basic modification info for each state NCOP: http://www.infrastructure.gov.au/roads/veh...n/vsb_ncop.aspx (all standards based on this) ADR: http://www.infrastructure.gov.au/roads/mot...adr_online.aspx NSW: http://www.rta.nsw.gov.au/registration/dow...si/vsi_dl1.html See VSI06 "Guidelines for light vehicle modifications" VIC: http://www.vicroads.vic.gov.au/Home/RulesS...rdsInformation/ See "Modification Guide" QLD: http://www.transport.qld.gov.au/Home/Safet..._modifications/ See "Motor vehicle modifications booklet" NT: http://www.nt.gov.au/transport/mvr/vehicle...rds/index.shtml (Refers to NCOP) See "Modified Vehicles" SA: http://www.transport.sa.gov.au/personal_tr...ht_vehicles.asp (Refers to RT Act) See "Modifications of Motor Vehicles" WA: http://www.transport.wa.gov.au/licensing/1882.asp & http://www.transport.wa.gov.au/licensing/1421.asp (Refers to NCOP) ACT: http://www.rego.act.gov.au/registrations/regomain.htm (Refers to NCOP) See "Light vehicle modification info"
-
Car Still Missfiring After Change Of Coilpacks
Jmaac replied to Jay_stylz's topic in General Maintenance
check harness? -
We have a large machine shop here (a small section of it actually used to be an engine reconditioning shop) Im an engineer at an (ductile) iron foundry. I do the majority of product design, tooling, process improvement etc. so CAD/CAM is no problem Its not cost effective to have one of our cnc's tied up doing tooling so we usually outsource that component (still trying to get my own) Limited to 12-13tonne max. per pour
-
If you want to pay for the tooling I can do it here
-
Poor design, look at the transitions compared to the blitz!
-
Archers Smash Repairs in Ashmore are not to bad (opposite Nizzpro)
-
Recommended Engineer To Certify A 25det In A Laurel
Jmaac replied to RB25DETC33's topic in Queensland
Goto the QLD transport website. There is a list of all the certified engineers -
check the rail pressure
-
check that the belt hasnt jumped any teeth. will do that if not tensioned correctly
-
4 Jul - 11 Oct - one bolt! haha so painful when you see how easy it comes out in the end hey? You could of done it 10 times Should be heaps easier next time!
-
ignition module/power transistor. most common sympton people experience is a missfire however when they get real bad they will intermittetly cut all power to the ignition until it has cooled (generally). is it difficult to re-start?
-
Jaycar have kits to do this also (+ kits for wideband readout)
-
Can you borrow a ratchet style one?
-
If you can get hold of a broken one theyre relatively easy to fix if you can solder. Only problem is getting the plastic pieces apart You can get cheap replacement ones from autobarn but the holes dont line up so you'll have to use double sided s/tape. Enough if you want a roadworthy/safety cert.
-
Unless you really need it or have money to blow go for the same CCA as whats recommended for the car. If the car struggles at that then theres an electrical issue that needs to be fixed. As above make sure its sealed, or has a vent which allows hose attachment. Make sure the terminals are on the correct side and are also the right size.
-
+1 for the regulator. Easy to change depending on type, usually little black box on back. As steve said just double check with a Multimeter Thats a service. Recond. alternators are usually rewound also.
-
+1 Get a higher grade. The extra safety factor in property class 12.9 or 10.9 bolts will help or you can try removing the surface irregularities by polishing Property class 12.9 is 1200MPa UTS and 0.9x(1200)=1080MPa yield Property class 10.9 is 1000MPa UTS and 0.9x(1000)=900MPa yield as compared to Property class 8.8 is 800MPa UTS and 0.8x(800)=640MPa yield
-
Take it to an autoelec to have it rebuilt. They can do it quite easily (I believe they use components from an AU XR). I have also heard of Castle (Cove?) Auto Electrics doing good work Did a quick search, these all have bosch 120a alternators 2004 Volkswagen Touareg 1997 Volkswagen Passat 1999-2001 VOLVO 2.8L Saab 9-3 93 TiD 92-95 VR6 Corrado 94-99 Jetta GLX VR6 02-04 Jetta Wagon 95-99 Golf GTI VR6 (These are Mk3 bodies). 92-97 Passat GLX VR6 93-2004 Eurovan VR6 or Winnebago / Rialta RV camper (150A) 1996 - 2001 BMW 528i 4DR (E39) 1999 - 2001 BMW 328Ci 2DR (E46) 1999 - 2001 BMW 328i 4DR (E46) 1999 - 2001 BMW 323Ci 2DR (E46) 1999 - 2001 BMW 323Ci CONV (E46) 1999 - 2001 BMW 323i Wagon (E46) 1999 - 2001 BMW 323i 4DR (E46) 1997 - 2001 BMW Z3 2.3/2.5 Roadster (E36) 1997 - 2001 BMW Z3 2.8 Coupe (E36) 1997 - 2001 BMW Z3 2.8 Roadster (E36) 2000-2003 E39 M5 (Sedan) and Z8 (Roadster) Holden VT V8 Audi A6 Quattro
-
No need to get your knickers in a knot, just trying to help. Yeah I’m laughing too, some brief answers for your brief ‘points’. Firstly it depends on the manufacturer and to what extent. Nuts are commonly manufactured to different tolerances than the stud/bolt/shaft ‘it will be attached to’ it’s called class of fit. In general a nut with strip before destroying the stud, this is not coincidence but a design feature. In fact, a nut is usually softer than a bolt to allow slight yielding of the top threads and thus distribute the load more uniformly among the threads in contact. I believe what you are trying to say here is that the length of nut engagement is balanced between bolt tensile and thread stripping strengths, and yes I agree they are made like that in special instances. That would allow you to say the stud/shaft defines the UTS (which is actually a property of the material). When designing around fasteners the 0.2 offset yield is used over the UTS anyway. Without working for ARP I wouldn’t know what their design requirements specify, but you seem to know. Yes I understand torsional strength is lower than axial strength (in most isotropic materials by a factor of 1/SQRT(3)) and yes in most instances a nut will convert torque into thrust (or clamping force) more efficiently because of the reduction in thread contact area (less energy absorbed by friction i.e. heat, sound etc.) …not simply “by the way it must be tightened”. You have completely forgotten about the nut failing in traverse shear. This is what stud/nut or bolt/nut interactions are based on (as above). I suggest you read some proper literature yourself. Your increased clamping force at the same torque has just brought your nut closer to failing in traverse shear than the much higher axial stress you anticipated it failing at earlier. Don’t worry about torsional shear or axial stress, your going to strip the thread from the nut! (or destroy both equally in your opinion, two birds one stone? economical). Yes I have used many… both really small and really fkn BIG. Most people don’t know wrench accuracies change with graduations in scale (eg. two parallel scales with a shift each graduation) and unless you can fully distribute your hand across the whole handle or use one finger directly in the middle at perfect right angles your result will be off. The variance is quite surprising. Remember 1400MPa is strength per unit area. What are the original ones rated at? I’m just trying to help people by providing an understanding in plain engrish of the benefits of using studs in an engine block. That is, after a stud is installed the block is effectively in a state of stress i.e. there are invisible forces pulling or holding these studs into the engine block. When the head is torqued back into place, these studs are effectively pulled back up out of the block, basically back to its ‘original position’. Even though the head is torqued nice and evenly on, the sum of all force at the block/thread face is next to ZERO.
-
Damn me too.......... Actually, bolts are stronger than studs+nuts in terms of clamping force as the nut is sacraficial to the stud thread. There is no such failsafe in a bolt. The reason for studs being superior in this type of application is because when a stud is torqued there is a state of compression left in the blocks thread region. Next when you clamp the head on with nuts, it exerts an opposite state of tension to the area. This tension cancels out this compression and eleminates the majority of residual stresses in your block. Yes bolt torques will differ from nut torques because of the increased contact area but that is how it was originally calculated/measured from factory. Needless to say, applying that same torque to a nut could be dangerous (even with a different type of factory lubricant). Also there are two types of friction working, static and dynamic. Static friction is much higher than dynamic hence you should never torque a bolt from stop i.e. should be torqued from a 'running' continous movement. Using torque wrenches correctly is quite complicated because of the different types but I wont get started here. With regards to the different head stud sizes (M10x1.5p and M12x1.75p) then theres deffinately a difference in tensile stress areas (58.0 and 84.3mm^2 respectively) and hence overall strength (M12x1.75p 45% stronger than M10x1.5p). Although a/market bolts are genuinely treated to higher grades, I would say a/market 25 nuts (or bolts) would definately be superior to the original 26 bolts. As above the dowels do the locating. That said, you have to machine at the top of M12 tolerances to get the correct clearances from an M10 thread (M10 on top and M12 on bottom tolerance = problems). hmm so a/m 25 studs for 26 head application most likely ok in my opinion and studs are good in general when doing block modifications
-
On R33 S2 its in the boot. Top 15A fuse
-
all ryco... z145a oil filter - 7.5/30w is stock visc. (so any fully synth 10-40w / 5-30w will do) do a search for particulars z200 fuel a360 air
-
+1 slave cylinder rubbers
-
Yes thats the sump plug What are you going to do? this sounds scary