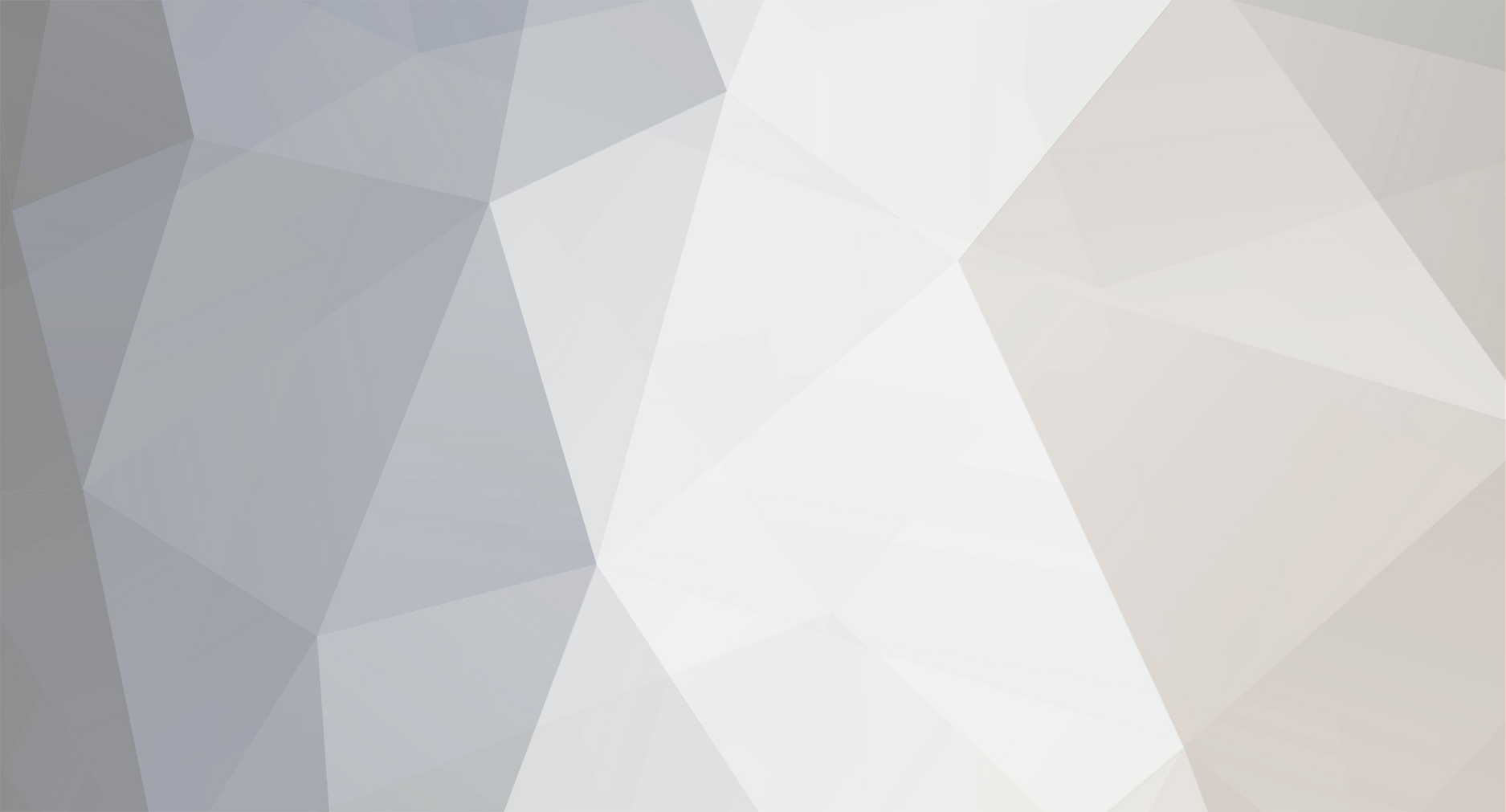
GT-RZ
Members-
Posts
331 -
Joined
-
Last visited
-
Feedback
0%
Content Type
Profiles
Forums
Events
Gallery
Media Demo
Store
Everything posted by GT-RZ
-
No not too bad if it's got coolant in there your just diluting it. allthough it's better to top up with demineralised water rather than tap water. obvious reasons.
-
Oil Control In Rb's For Circuit Drag Or Drift
GT-RZ replied to Sydneykid's topic in Engines & Forced Induction
I'm looking through your diary atm. looked like fun. Positive crankcase ventilation valves are only meant for one thing, what other use would it be. If you follow where it connects to the firewall, follow that hardpipe and it goes to the right hand side somewhere, on it's way to the intake. There is certainly no filter in view sat on top of the catch can or the side. it would make perfect sense for a top class car to be using re-circ, it's the most efficient way to do it. I think you are right with the images of the engine though. on the front of the engine image: We have them two lines, the one on the right most likely is to connect to the head attachment as the one on the left is shown attached on the engine bay shot: And i just found a front shot of the bare block (had it before and never paid attention ): There is the attachment that the hose will connect to from the rear of the head. With it's location it's most definently being primarily used as an additional windage vent, which is how i planned to use mine like posted earlier today! Finally i know So that's cleared up on m speeds use, which i'm happy to follow. i'll continue through your diary for images lol. -
Oil Control In Rb's For Circuit Drag Or Drift
GT-RZ replied to Sydneykid's topic in Engines & Forced Induction
That would be great. I'll check your diary post too. The pipe in view could be an oil drain but it seems too high as i would rather mount a drain at the lowest point. If it was a drain there would still be another connection elsewhere. The pcv valve is needed in recirc simply so that when the engine is on boost it will close and not let any positive pressure in the crankcase, when idling it will open and allow natural vacuum to suck from the crankcase. The connction before the turbo intake (i think it sits in the cold air box, unsure - have to check) does it's job primarily when the engine is boosting as the other valve is closed and this one lets the turbo suck a vacuum from the crankcase via this line. upon idle it teams up with the other connection with the PCV valve attached to it which would be open. If you have one line run directly to your cold air box or my preference (between turbo and pod) you do not technically need a PCV valve inline but it will not hurt anything and could help if natural vacuum was created within the crankcase. m-speed due to the PCV valve being connected on the balance tube(above throttle bodies) clearly use both vacuum points. vacuum lines can be very small and m speed has chosen to adopt the rear in to a hardline across the firewall, nice idea. this will in-turn join with the line from the cold air box or alike. Somtimes people can do more harm than good when messing with factory set-ups. venting to atmo is not too bad and the primary reason people do it is because they install a catch can and think re-circ is only for emissions, which is wrong. Infact if that were true the factory connection to the intake vac line would not be there as not all gasses would be sucked back through the turbo. The primary reason is for good venting of the crankcase, just that under high loads the connections from the block to the head obiously are not sufficient and the head potentially becomes overun with oil and we get a mess or in re-circ excess vapour in the intake. m-speed's extensive filtration system clearly aims to eliminate as much oil vapour as possible before allowing it to enter combustion. Sorry quick edit: i never saw your last bit at the bottom. You cannot see any small connection from the PCV to the cam covers because unlke the factory setup where the two are linked without catch cans and additonal filters, M speed do have the additonal catch tank and filters. so the lines from the cam breathers must pass through the catch filters before re-entering via the vacuum lines. -
Oil Control In Rb's For Circuit Drag Or Drift
GT-RZ replied to Sydneykid's topic in Engines & Forced Induction
In the 2009 image i can see a line that goes back from the catch tank yes. It would be travelling to the other vac line which plumbs in to near the turbo intake, like factory. there is always two lines on the factory setup. one near the manifold and the other near the intake. vacuum lines need only be small, easy to hide away and make things look tidy. Infact m speed joins the manifold PCV valve pipe in to a hard pipe that runs along the firewall. easy to spot? If you have seen it with your own eyes i would have taken note of where the head connection joins the block! did you? i'm interested! When the PCV is connected why would they use vent to atmo? have a hose to the PCV for looks or something -
Oil Control In Rb's For Circuit Drag Or Drift
GT-RZ replied to Sydneykid's topic in Engines & Forced Induction
? Why do you think that. They must just connect a pipe to the PCV valve or 'blowby control valve' as Nissan call it for the joy of it then? I can assure you in the images above, both 2006 and 2009 they are using a re-circ system. -
Oil Control In Rb's For Circuit Drag Or Drift
GT-RZ replied to Sydneykid's topic in Engines & Forced Induction
I agree. which is why the discussion did not end when the website was discovered. -
Oil Control In Rb's For Circuit Drag Or Drift
GT-RZ replied to Sydneykid's topic in Engines & Forced Induction
There is some similarities mainly in the use of multiple filters/tanks but they are using intake vacuum and you vent to atmo. so there system will be venting much more efficiently and more than likely creating internal atmospheric vacuum which we all know the benefits of by now. They still use the factory pcv setup (one in the balancer tube and the other near the turbos) just with there additional tanks/filters. The other way to achieve the same effect would be to block of the factory pcv valve then run a line directly from the final catch tank to between the turbos/pod with an inline PCV valve although there must be some advantage in doing it the way the factory has otherwise i fail to see the reason behind all the effort. Not forgetting they have the connection at the rear of the head to aid flow to the covers and as a potential oil escape. wheras you opted for the block vent method, both good options. With your current setup dirt going with the idea of keeping your current oil drain from your catch tank (since it would at some point be submerged in oil imo due to placement in the sump wing and not acting as a vent all the time) Plumb another attachment from the block to mid point in your catch tank (or relocate your drain higher up in both tank and block). Then replace the filter on your final tank with a pipe that connects to between the turbo/pod with an inline PCV valve (or thread one in to your catch tank at the start of this pipe). Due to the large amount of tubing you have making sure it's all air tight would be paramount. Then you will be using a vacuum system VERY similar to m speed r34 with the extensive amount of filtration. what would be good is to attach a pressure gauge to your system (wherever you like) before you do this and then compare results. When i get around to setting all this up on my new 26/30! i'll be doing it like above most likely unless i go the hard yards and set up lke m speeds 'factory variation' The only difference to yours is i'll probably fit the head attachment and miss the block vent and try and net both potential gains. -
Is that directed at his question or is that your question You wouldn't want to leave tap water in there for any other reason than flushing it imo... unless you want rusty water chambers.
-
I was simply making a light hearted joke, you were supposed to laugh! Really the answer is obvious, you are not asking for information how to fix it because you did not post up any image of the crack. what can you expect? I told you how you should weld it up to prevent cracking in the same direction. You will notice the factory runners are cast and quite thick so i would advise you remove a small amount of material around the crack with a sharp tipped die grinder. then get a competent welder to fill er up, then drill two holes either end of the weld and weld them up. There is the full story. I told you basically that before the rest was obvious. If you did not want advice on fixing it then i suggest you should have called the topic 'New manifold options for RB20'. My posts were for your benefit only.
-
Oil Control In Rb's For Circuit Drag Or Drift
GT-RZ replied to Sydneykid's topic in Engines & Forced Induction
Yes they have a very nice setup and with the later version seem to have added extra filters rather than have the one which is up to the individual, probably a good idea especially if you plumb it in to re-circ. interestingly with there setup is the additional brass attachment tapped in to there head connection: as seen here which is an addition to the Auto Staff product. it's more than likely just a vac line attached to a gauge to read the pressure (which would be handy?) As for the re-circ i tend to think that the m speed r34 would re using re-circ especially when it still has the standard throttle body assembly with the balance tube etc which is where the factory pcv valve is located... if you look on both images there is certainly a hose heading from the PCV valve but tracking where it leads to is another case (looks like the factory location, though), there is also hoses under the catch can... If you do not change your manifold or 'throttle body assembly' with rb26 then the factory recirc setup is as good as any other choice you can make just add in your own catch tank etc that is sealed, that's why above i listed it as 'If you had your own manifolds / piping' you could always try to duplicate the factory system with it's t junction etc but probably not needed. I might try sending them an email you never know. -
Oil Control In Rb's For Circuit Drag Or Drift
GT-RZ replied to Sydneykid's topic in Engines & Forced Induction
yep i agree with that perfectly. The factory re-circ infact is almost a perfect system if a catch can/seperator was introduced in to it (uses one way pcv valve and venturi effect to create vacuum). with the additional connection to the back of the head and larger returns to allow the bottom end to talk with the head easier. Would be flawless IMO. If you had your own manifolds / piping to achieve the ideal setup you simply need to go out and buy a pcv valve (one that allows hoses to fit either end) Then run a hose from the cam cover breathers (just link one to the other then run one hose to the catch can/seperator (with an oil drain to the block if you wish, not recommended) then run a hose with an inline pcv valve (could be mounted to catch can if you wish) to the intake just before the turbo (behind pod filter/ AFM) (reason being is that if you have after the turbo when on boost you will not get ANY vacuum at all as your boosting... if it was an N/A you could mount it anywhere as the engine is always sucking and never being 'boosted'. The Rb25 has a pcv valve in the cam cover but it does not matter if you intend to have an oil drain to the block, reason being that if you just used the cam cover valve and then put a drain from the catch can which links to near the front pod the 'oil drain' from the catch can will be acting as a vent too without any vacuum control. If you don't intend to have a drain back then you can use the one in the cam cover. although the closer the valve to the source of vacuum the better so having it inline with the hose to the intake is better IMO. Then with this setup you would ideally want the vent/return to the rear of the head to help everything flow around easier. Enlarged oil returns etc would still be a go go. Where the drain/vent from the head plumbs in to the block is your decision, i think either side will have some benefit but read what's being said and make an educated guess! personally i'm leaning to the intake side wherever is convenient and use it to help vent some pressure up top as the primary goal. (still want to see m speed r34 intake side of engine to see what they did ) someone gotta have a pic!!!!!! With the above setup a vent from the block directly would not be needed, i think the above is the best solution IMO as the connection to the head allows venting and potential oil return also. Of any use? -
Oil Control In Rb's For Circuit Drag Or Drift
GT-RZ replied to Sydneykid's topic in Engines & Forced Induction
On another note there seems to be no small adjustable pneumatic 'mechanical' valves i can find. I have a few places to ring around but for the most part i think the standard PCV valves may be the best option. cheap and easy to find, plus i noticed there is a few fittings for the later model nissans that don't have a thread machined on one side just a hose attachment each side which would be perfect!! -
Id check my bank balance and try again. if all the other pistons are perfect? are they perfect? then just replace them ones. how is the cylinder wall damage? does it need a rebore? if so, new pistons. apart from that it serves as a big lesson to rush things! no way i personally would strap the timebombs on a new engine.
-
Oil Control In Rb's For Circuit Drag Or Drift
GT-RZ replied to Sydneykid's topic in Engines & Forced Induction
This picture does not explain it all. if we had a picture of the intake side of the engine it attaches to we can make more educated guesses. You clearly underestimate some laws of physics. In an engine as we accelerate the g force does increase but what also increases is the windage within the block and with that would also come an increase in vacuum from the potential 'venturi effect' which is exactly how the turbo oil returns work. This is also exactly how the stock re-circ system works. you increase RPM hence windage and simultaneously the intake air speeds are increased which pulls more vacuum, a perfect cycle. This is the entire reason why we have no clear answer to this debate, it can be used as a drain or vent on EITHER side of the block depending on it's location relative to the cranks centre. Fact remains if you added a drain it would help oil problems and if you added a vent it would help oil problems, which way is best is what we will not know without testing (or copying the fastest R34 around a track M speed pics ppl????) To add to your image 'conclusion' i have attached a link (posted earlier. the link is to the following product: http://www.rhdjapan.com/jdm-low/Auto-Staff-RB-Engine-Oil-Return-Block-RB25DET-RB26DETT-59928 That is the exact drain used on the image you think clears everything up. They state: They do not list where it should be attached to the block so it does not help with any part of this discussion but it seems clear on there 'intended' use. weather or not m speed followed this path we don't know. m speed pics We do know they have it attached to the right side, which proves not much. PS i am not taking any side. there is arguments from both setups. I do know that if a vent was the primary goal with no additional oil drain needed, a vent directly from the block would be far more efficient. Maybe the m speed r34 team aim for both as even if it was located as a vent due to the size of the hose any reasonable amount of oil would have no trouble flowing down half the tube whilst the other half was still being used as a vent... Despite what some think crank 'windage' is not all that strong. the main concern is pressure build up. -
when you start your car on a cold day you will always get condensation, it will not lower your coolant level... smoke is smoke and condensation is condensation... can you smell smoke?? is it white or disappears? plus when you first start your car there is no way it would overheat straight away. From what you have explained it sounds like condensation on a cold day. unless you can explain in more detail i don't think you need worry.
-
Oh wait i think i see the problem!!!! you need an excuse to buy a new fancy perfect manifold... Yep it's F*cked if you leave it the crack will enlarge and cause your left tire to explode. Very dangerous, i would suggest a custom jobby. that RIPS one sounds nice?
-
Oil Control In Rb's For Circuit Drag Or Drift
GT-RZ replied to Sydneykid's topic in Engines & Forced Induction
Well it depends on the setup really. if you had setup a venturi effect inside the intercooler piping (factory does not do this but...) then without a one way valve when the throttle is closed (which a bov is designed to vent) it could potentially push air down the wrong way of our vent and pressurise the crankcase, which we don't want. Basically if you mounted your re-circ to utilise venuri effect you would be mounting it before or after the throttle body. If it is after the throttle body (ie inside the manifold given that it's a single entry throttle body) then you would not have as large a problem as it would not experience big issues due to 'refused' pressure. But if you have six individual throttle bodies it may prove difficullt to achieve this and the re-circ may have to be mounted before the throttle bodies, leaving it vulnerable to positive pressure once the throttle is closed. So to your question a BOV would be beneficial if you mounted it before the throttle bodies because it is designed to release excess positive pressure. Bearing in mind if you just ran a one way valve you would not worry wherever you mounted it. Think i explained what i mean? -
pfft i prefer the sound of stainless and titanium than mild anyway. each to there own. You could get a custom one made of thicker stainless pipe and get the same noise as ur mild one. the 'tinny' noise you talk about (which i wouldn't say they are) is just because SS generally comes with thinner walled piping due to it's properties. titanium is normally thinner again.
-
weld the crack up. if your worried about the crack reopening in the same direction drill a small hole either end of the crack and then weld it all up. see if it holds up, id be doing that before buying a new manifold?
-
Wouldn't worry too much. If your coolant is overheating too much you will know when your bay sounds like it's got a kettle in there... Look on the floor where you park your car. is there any coolant on the floor?
-
Oil Control In Rb's For Circuit Drag Or Drift
GT-RZ replied to Sydneykid's topic in Engines & Forced Induction
Anyone got a pic of the m speed r34 intake side of the engine???? That will prove if they are using the head connection primariliy as a drain or a vent... If its higher than the centre of the crank it would certainly point towards more of a drain utilising the venturi effect... if not then more of an extra windage escape... I would like to add that the connection to the head would not be as neccissary if you have a vent from the block directly... Anyone know where you can source some pneumatic one way valves? one that is adjustable and able to open at very low pressures would be ideal... You could connect that from your vent on the intake side of the block (must be above oil level, dipstick would be ok) or from the breathers on the covers ideally coupled with the head attachment if you don't want a vent from the block. Then attach that directly to the TOP of your catch can that vents to atmo or even better to some sort of vacuum setup, or either plumbed in to intake (factory re-circ would work... and with the one way valve you would not need a BOV if you did not want one...) or exhaust to utilise natural vacuum (venturi effect). That way you could guarantee no positive pressure is going to enter the crankcase from your escape (engine will make it's own negative pressures depending load of the engine) and it would allow rising positive pressure an escape! -
well i saw a TB48... bloody big engines. never ever fit one in a silvia hah(like huge bonet bulge much?). Guess thats good to get it out of my head lol. Be good for a drag car setup though when stupid bonets don't matter much.
-
Oil Control In Rb's For Circuit Drag Or Drift
GT-RZ replied to Sydneykid's topic in Engines & Forced Induction
It was an example. Any level of vacuum is possible although generally gauges will only show up to -14.7psi. You need to read up on vacuum. would you have prefferred to say 15inHG instead? I will not go in to vacuum but it is as endless as pressure. You are reinforcing your comment that Zero pressure is that same as -15psi or whatever stupid comment you made. Infact thinking about it i think you have confused yourself. atmospheric pressure is standarised at 14.7psi which is close enough to 15psi... if you were to take away 15psi then you would be at around zero pressure, correct. is this what you are saying? What is being said is the atmospheric pressure WITHIN the CRANKCASE is lowered to a negative pressure (vacuum) If you have a system that is capable of removing 15psi of pressure then indeed the atmospheric pressure WITHIN the crankcase could be zero. That would depend on where the pressure was when it started (+15psi). If you have a system that is variable and can KEEP the atmoshperic pressure at -15psi or 7.5inHG is you prefer then that is completely different, and is what i was reffering too. And would be over the top. The perfect system would keep the pressure between 0 and -1psi or 0.5inHG. IMO. I think you have come unstuck when the word atmosphere came up. when i say atmoshpere within the crankcase that refers to a local atmosphere within the crankcase, not the earths atmosphere... -
Oil Control In Rb's For Circuit Drag Or Drift
GT-RZ replied to Sydneykid's topic in Engines & Forced Induction
I understand how rings seal. I also understand there primary function is to compress mass and to take combustion pressure. Rings have an order for a reason and only the top one is made to take the brunt of force. All lower pressure in the crankcase does is remove any additional resistance pushing against the rings in the wrong direction, therfore the more crankcase pressure the greater the Force being applied to primarily the weaker rings at the bottom. having zero pressure would be optimal or a vacuum that would create marginal force. this would allow the rings to deal with primarily forces from the top, operating in the order they are designed. To think that the higher the vacuum pressure the better a ring will seal does not make sense to me. A ring is just a seal, the pressure it can properly function in is not unlimited and ringland failure is not uncommon. Like any material if you place too much force on it they will fail. Just like i said before, when you add a vacuum under the rings you are simply increasing the downward forces acting on the rings. if you were to increase combustion pressures to a point where the rings failed you would get the same effect increasing the vacuum. 200psi of combustion pressure plus 30psi of vacuum effectively has 230psi of downwards pressure. 30psi of that is acting primarily on the lower rings which is an extra stress they were not designed to deal with. Unless you were talking about something else? -
Oil Control In Rb's For Circuit Drag Or Drift
GT-RZ replied to Sydneykid's topic in Engines & Forced Induction
Having pressure in the crankcase means the pistons/rings have to fight against it, that's what i was saying before. Having too much vacuum will still cause a problem rather than a benefit, though. If anyone has images of the M speed r34 intake side of the engine id love to see them!!! i can't find any, only of every other angle hah. Simply because if the venturi affect was to have any huge advantage on the intake side then it must be placed offset to the centre of the crank in the positive rotation direction of the engine! If it is not higher than the centre of the crank on the intake then it merly would be working as a windage escape just like the channel at the rear of the head on the intake side! Hence why the exhaust side turbo oil drains are lower than the centre of the crank (all RB excluding front drain on rb26? clearance maybe) , ensures no horizontal windage could be pushed up the return. This allows the drain to use the vortex of the crank windage to 'suck' oil down that turbo return (venturi effect). the position of the connection to the block could be deceiving but is very important!!