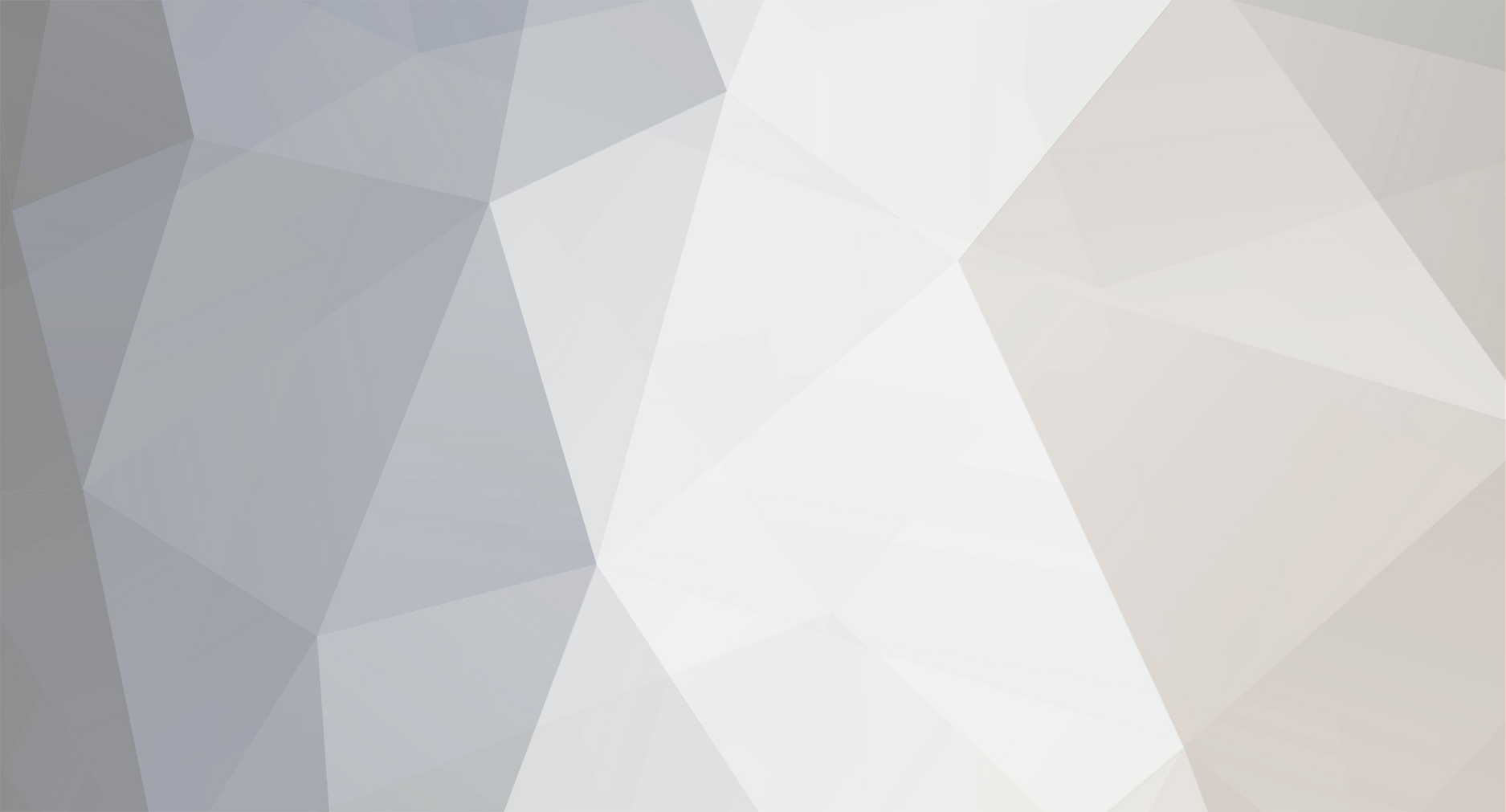
GTScotT
Members-
Posts
4,917 -
Joined
-
Last visited
-
Days Won
2 -
Feedback
100%
Content Type
Profiles
Forums
Events
Gallery
Media Demo
Store
Everything posted by GTScotT
-
Well sarge, you have been underground for some time now... Le test car now sports a high mount and E85, while the SS2 has since gone from 71mm hi/lo blade to 74mm full blade compressor. The SLSS2 is the SS2 compressor mated to a TD06SL2 turbine, like on the kando T67s.
-
65Mm Pistons - Ie Stock Bore For An New Rb26 Block
GTScotT replied to djr81's topic in Engines & Forced Induction
Agree, I think its good that it's discussed. If the thread title was a little more forgiving it would be better lol but I think this thread will be a good resource in future. I know this will sound rough but has anyone building an RB ever thought to take to the oil drains with a power drill? Surely they could be opened up fairly easily. I might need to build an RB soon, just to prove I can lol -
65Mm Pistons - Ie Stock Bore For An New Rb26 Block
GTScotT replied to djr81's topic in Engines & Forced Induction
It's all relevant and going to help OP anyway, I say keep discussing it. Again I think a lot of this comes down to build quality. In my eyes torque plate honing the block should help get an effective seal, and I have always seen the ring gap as what effects blow by the most (I think we all know all motors have blow by and the issue is how much). I understand what you are saying re wider rings letting less blowby pass, yet I think a seal is a seal. Once broken it wont matter how wide it will continue to pass through. Therefore if the bores are done right the rings should seal equally, once combustion pressure overcomes the rings it would be the same effect regardless of the quarter mm difference. I may be wrong, yet do think discussing this will add value for people wondering about the same in future plus helps OP consider his options. -
Yes they come in different thicknesses. No MLS gaskets are not reusable as they normally have a coating which bonds to the mating surfaces. If you have assembled a motor (not run it) and pulled it apart again you can usually reuse the MLS. Yes skimming your head will raise your compression ratio. If the gasket is thinner than stock this will also raise it further. Generally skimming alone wont be enough to warrant a tune or any serious change. If you are building the whole motor you should buy a proper gasket and not use a second hand item. Know what is going into the motor and don't waste your efforts on second hand consumables.
-
65Mm Pistons - Ie Stock Bore For An New Rb26 Block
GTScotT replied to djr81's topic in Engines & Forced Induction
It's a fair argument, and I'm all for improvement. I hope it does work for him, you can see I've been trying to give with what help I can. For me I am struggling to see that the thickness of the rings will effect blowby. The gaps are one thing, but thickness of the material another. Am not totally convinced but am happy to be educated. -
65Mm Pistons - Ie Stock Bore For An New Rb26 Block
GTScotT replied to djr81's topic in Engines & Forced Induction
I find it more than odd that you believe this to be the issue when most people can build an RB and do the appropriate oil control mods to fix the issues stated, most to all using off the shelf piston kits with their thinner rings. You have literally said thin rings don't cut it in a turbocharged application. Do you believe they do not seal? Do you believe everyone who has a built RB with the supplied 1.Xmm rings has a dud which will have excessive blow by? I think this is a very strongly worded opinion in light of the unending number of people who have had flawless success with off the shelf piston kits and their thin rings. You have mentioned that experienced builders gain success by having breathers in the right spot, which I must agree is probably the real trick to it all. Yet you have also noted that standard motors (which have 1.5mm rings) don't have this issue, like a built motor with 1.5mm rings wouldnt, when in fact they do. It is known fact that a 'tracked' internally stock RB26 should have all the drain/breather mods done and should over fill the sump by 1L to stop it puking its guts out and nuking itself. I agree that the thicker rings would work for a stronger motor (better heat transfer plus outright ability to take heat and not fail, which would make for a stronger motor when building for extreme application), but can't for a moment believe that running thinner rings 'just won't cut it' in terms of providing a seal and stopping blow by. I still believe we are simply discussing poorly built motors. -
65Mm Pistons - Ie Stock Bore For An New Rb26 Block
GTScotT replied to djr81's topic in Engines & Forced Induction
And that is a fair theory, yet you may be trying to reinvent the wheel where over engineering your rings is not necessarily going to fix the fact the RB's have poor drainage or overzealous pumps. I really recommend you invest some time into disassembling the broken RB and working out what it wrong for yourself. Like I said I am betting the second compression ring is upside down in at least 4 of the 6 cylinders. -
65Mm Pistons - Ie Stock Bore For An New Rb26 Block
GTScotT replied to djr81's topic in Engines & Forced Induction
I don't think the oil control issues experienced with RB's has anything to do with blowby mate... They are just a piston with rings on it, and piston manufacturers dont make vastly different pistons for different motors.. For example, your CP's would be more or less identical to the ones in my SR. Pin height and all that would be different but the pistons and ring design very much the same. I do not have oil control issues nor do I have blow by. The rings in my SR are exactly what came with the CP kit. There is no cursed flaw in the RB26 block.. Its just a piston in a bore, like any other motor. Oil control issues are caused by the pump volume vs drain efficiency and blowby/leakdown is caused by worn motors or shit builds. I am sure everyone will be happy to back me up here. Chances are you will go to all this effort only to find a quality build would have fixed it, and I bet I know what the problem is anyway.. I nearly did the same thing to mine, but you will need to pull the motor down to find out. The CP's come with an oil wiper 2nd ring. The 2nd ring is designed to wipe oil back down to the oil rings and let a little seep up to the top rings for lubrication. Get this upside down and it will wipe all the oil up into the chamber, making the motor pump smoke, plus will likely get bad leakdown results as it will work the opposite way to what its meant to. I reckon this could be your problem, and you could save yourself a motza if you just pull that motor down and check. You might find that $500 on a new set of rings and a quick hone could save it entirely. -
65Mm Pistons - Ie Stock Bore For An New Rb26 Block
GTScotT replied to djr81's topic in Engines & Forced Induction
Sounds extremely complicated for a very simple build. Just so I know, your going to this much effort just to have a 1.5mm ring, right? -
Yeah, there are people talking about that in this thread. Somewhere between here and page 1, its one of the most discussed topics in the whole thing.
-
How do you mean? Is there some kind of evidence that they have been rebuilt prior? What did GCG tell you
-
I quoted what you said and asked WHY
-
Its not possible that you cooked the seals without the water connected. Even Garrett says the water cooling is optional, and you put sweet f**k all worth of heat through them just idling. Unless theres an issue with your oil drains backing up I am 100% certain you were sold duds.
-
So the oil was in the cooler pipe or spraying out into the engine bay? Where's the oil coming from?
-
That's odd, its on fairly late. Yet if it feels like its on much earlier I'm guessing it actually has good pull before being on boost?
-
Fair enough mate, you only need to discuss what your comfortable. Am just curious.
-
Ah ok, thats interesting. The dyno is indicating a powerband from 120-180kmh, so 1/3 of the rev range (roughly). If you were to do it basically 8200/3 = 2733, x 2 = 5466. So the sheet is saying its on power at 5500 if its revving to 8200. Is it possible that graph is for a lighter ramp rate or something like that?
-
And the power? Tell em the price son.
-
That's good power for 98. I'm guessing its on full pelt about 5k? When does it start to get urgent?
-
Etsi bravo. What are you revving it to, Nick?
-
[Closed] Borg Warner Efr Series Turbos
GTScotT replied to Lithium's topic in Engines & Forced Induction
Theres an opel badge on the front of your vectra; you in the states or europe? What do you plan to do with these driers? -
Martin your not working with stock cams so that must be the difference. People only ever skim a few thou but the tool exists for a reason, clearly being that it does put them out.
-
The idea is that because your motor has never been apart the decks are at factory height. Being factory height means that when the belt is installed properly (all markings used, correct position etc) the cams will sit exactly where Nissan intended them to (assuming they are stock). Once you dismantle the motor things start to change. For myself both the head and block were warped, and I had to have both decked flat. This meant that the cams ended up being closer to the crank, so the non tensioned side of the motor had extra slack which pulled the cams back. Combine the new shorter distance between cams and crank with the new MLS headgasket and the distance was way off what it normally would be. So my thinking for yourself is that the motor is still within factory parameters and wont experience these problems. HOWEVER, this is only assuming that the cams are spot on. The cam supplier normally advertises the specs so the end user can check and confirm that the cams are at true centre (where the manufacturer intended them to be). The poncams are intended to be a complete drop in, and according to unigroup they did exactly that in my car... Yet I am still curious as to HOW spot on the grind is compared to what the specs say. I know the front of my cams meet the correct position/markers when the motor is at TDC, so I am just trusting Tomei from there. Which is pretty much the same position you are in.
-
300Kw Unopened 25 Club...
GTScotT replied to joeyjoejoejuniorshabadoo's topic in Engines & Forced Induction
Agree with you both guys. I built my SR as the cost to me doing all the work myself was about the cost of two stockers anyway, so it was well justified. Plus I'm hoping to see more than what a stock SR will reliably do in the long run anyway.