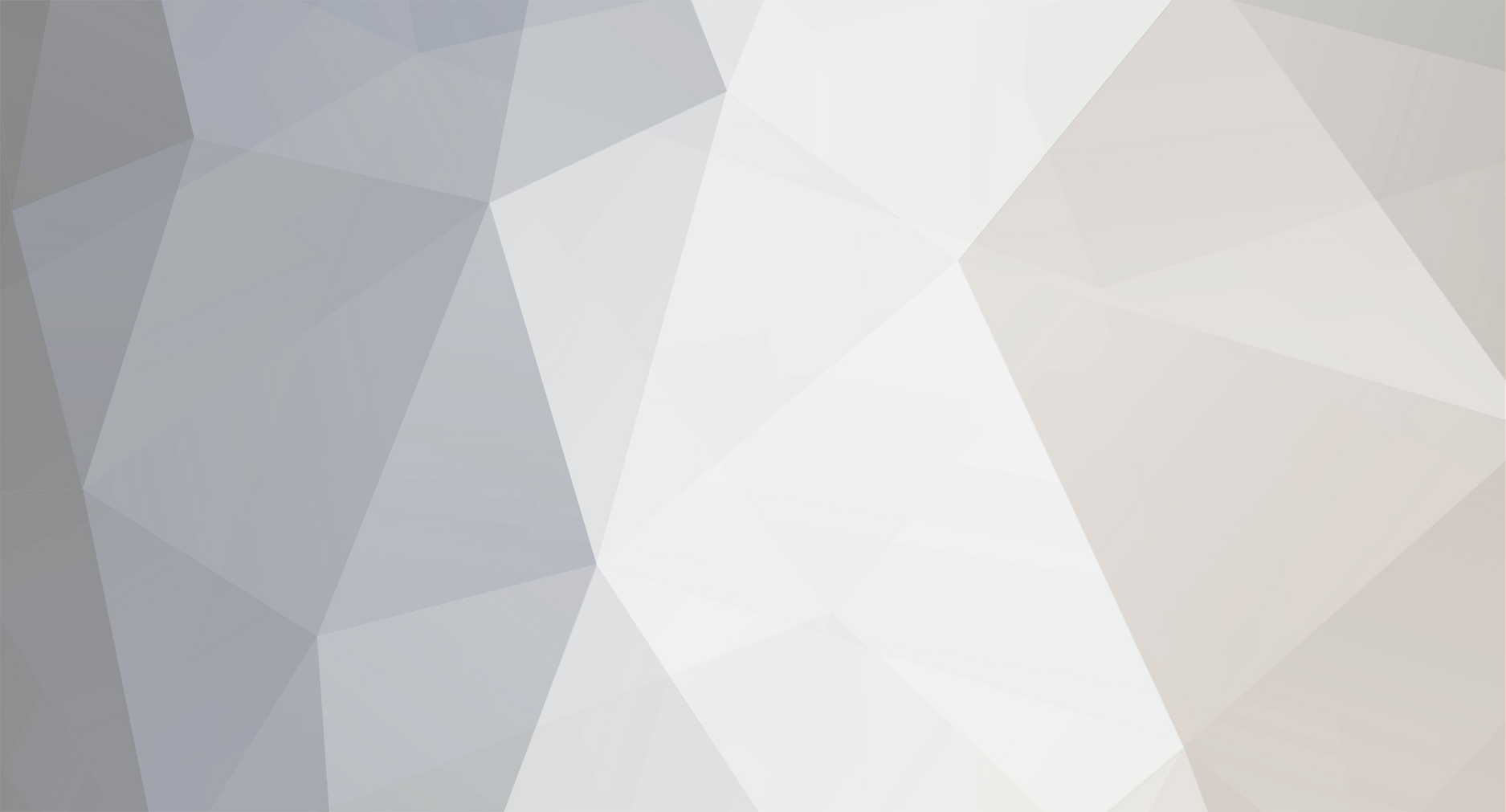
Gerg_R31
Members-
Posts
1,189 -
Joined
-
Last visited
-
Feedback
100%
Content Type
Profiles
Forums
Events
Gallery
Media Demo
Store
Everything posted by Gerg_R31
-
scando; grub screwing the crank isnt really a performance thing, its drilling out the press in bungs on the big ends of the crank, it helps with cleaning any sludge out of the crank from when people dont change oils often enough, or when the crank is ground it helps to clean any excess metal shavings out of the oil gallery, if the block is sludgey id say do it, and also get the front and rear main gallerie bungs in the block drilled to fit a 3/8 unc speedflow grub screw cp pistons are a good quality piston, but what dome or dish volumes, piston to deck height, head gasket volume, head chamber volume did they use to give the rough rating of 9:1 also make sure who ever hones the block make sure they hone to suit the chrome moly rings, if they dont use the right grit stones the rings will fail pre maturely you can still use the rb20/25 11mm head studs without needing to modify the block with a rb26 head i'd also suggest getting the annular grove in the block side of the main tunnel, rb26 main bearings, rb30 main stud kit optional (and i speak from personal experience working in a machine shop)
-
Gerg_R31's N/a Rb26/30De
Gerg_R31 replied to Gerg_R31's topic in Members Cars, Project Overhauls & Restorations
Assembly time. Kero washed everything, assembled, measured and calculated clearances, ring gaps etc, with flexi, feeler and dial gauges etc. Pulled apart re washed, then assembled using natural thiners and non-synthetic oils and assembly/ run in lubes, roughly dialing the cams in. All the usual stuff that should be done. I took my time and finally finished it over 2 weeks of making sure everything is 100% spot on and perfect crank clearances all on mid size, piston to valve clearance 0.130" on intake 0.0180 on exhaust Fitted the one off carbon fibre lower timing cover made. Had 3 dash 8 fittings welded onto the sump and fitted that, one for the drain kit, 2 for a catch can a bit further down the track. Also fitted the 90 amp alternator, engine mount brackets. Pulled out the old rb30e, dropped the RB26/30DE in Bought spitfire coil packs, silicon hose kit, fitted the ITB intake manifold, power steering Sent it to Liverpool exhaust, they fitted equal length 3 into 2 into 1 extractors, hi flow cat, 2.5" mandrel bent exhaust with a resonator and a straight through muffler. Fitted the carbon fibre upper timing cover and coil pack cover when I got it back Mick at Mick Motorsports wired up the Haltech Pro Sport 2000 I've since the tune, I had a little E10 in 98 pump problem, gave the head a quick reco but with very exact details everything like last build, while the head was off I started to make up my own ram tube manifold with gizmo thermal intake manifold gaskets Mick at Mick Motorsports is sorting out the throttle body linkages and doing the final tune with cam timing and stuff above is the most recent picture, not everything was put on as that was more of a dummy assemble picked up an oil cooler and oil catch can to put on when it gets back -
Gerg_R31's N/a Rb26/30De
Gerg_R31 replied to Gerg_R31's topic in Members Cars, Project Overhauls & Restorations
Assembled and measured all the clearances between the cam base circle and valve/ shim bucket, and machined the valves to suit making the valve clearances on the intake exactly 0.018" and exactly 0.015" on the exhaust. Once all the clearances were set, I back cut the intake valves adding a 1.5mm 30 angle CC'd up the head, got 66.5cc's Obviously too much, so I ground the head measuring after every 0.010" that was taken off, the first 0.020" took exactly 2 cc's off then it increased from there. End result, 0.080" was ground off reducing the chamber by 12cc's Test fitted all the spark plugs and added washers until they all protruded the same distance and all faced towards the center of the two intake valves. CC'd each chamber and die ground the squish areas until each chamber matched the largest chamber of 53cc's Weighed every peice of valve train, (valve, spring, retainer, shim, bucket) as a complete unit and weight matched every set to the lightest by removing material off the bottom of the buckets Measured installed spring height, put the spring in a spring tester and got 60lbs seat pressure, put the standard and a 0.050" spring base washer underneath and got it up to 85lbs The spring coil binds at 0.580" / 15mm after installed height, so after 0.080" / 2.03mm was taken out for clearance, I was left with the max spring lift of 0.500" / 12.7mm, since my cams are 0.425" / 10.8mm lift I got plenty of room Final head wash -
Gerg_R31's N/a Rb26/30De
Gerg_R31 replied to Gerg_R31's topic in Members Cars, Project Overhauls & Restorations
See how perfect the manifold and intake ports are blended together Since the RB26 cams are all designed to work with a turbo, I had to figure out a way to compensate. Camtech gave me a list of all their available cam grinds and with a few formulas, I worked out the best cams to suit my intended rev range and intentions for the motor. I then gave them the cams specs that I was interested in and they were ground to suit from billet castings. 10.77mm/ 0.424" Intake Lift 242° Intake Duration @ 0.050" valve lift 10.74mm/ 0.4228" Exhaust lift 252° Exhaust Duration @ 0.050" valve lift I measured every lobe, and the lobes were all exactly identical in lift and duration, the usual quality that Camtech provides (pictures are of both standard and Camtech intake cams) The cam lobes fouled with the head so with a die grinder I cut away at the top of the bucket area until it cleared with enough extra clearance I bought a set of adjustable cam gears, and a set of stainless steel 1mm over sized valves and valve springs to suit the cam. The valve seats were cut on our new Newen CNC seat cutter. Since the machine has a single point cutter, it is unlimited in how many angles or how wide they can get. The angles I chose ; Intake: 30° and 37° on the crown, 45° 1mm thick seat, 58° and 70° on the throat Exhaust: radius crown and throat with a 45° 1mm thick seat -
Gerg_R31's N/a Rb26/30De
Gerg_R31 replied to Gerg_R31's topic in Members Cars, Project Overhauls & Restorations
Cylinder Head I purchased a RB26DETT cylinder head that came off a R33 GTR, it came complete with full intake manifold and cam covers. I got it pretty cheap due to detonation in cylinders 1 and 6 plus 2 burnt out exhaust valves in them cylinders. As usual I took it to work and removed the over head gear to make it easier to diagnose any issues after its been acid bathed briefly Stripped it down completely removing the springs valves etc. Found bronze valve guides.... score I hate having to fit these f**kers As per usual, bead blasted the head Pressure testing the water galleries Bead blasted the injector part of the intake manifold Sent the head and intake manifold off for porting. Had dry flow bench porting done to the exhaust and "wet flow bench" porting on the intake and manifold (its the same as a dry flow bench but there is a dye that is sprayed in to replicate the fuel, and they port to correct anything that may create an issue when the air and fuel are atomizing) Also you may notice that I didn't get the ports smoothed out or "polished." If its too smooth the fuel will stick to it and it encourages the carbon to build up in both the intake and exhaust -
Gerg_R31's N/a Rb26/30De
Gerg_R31 replied to Gerg_R31's topic in Members Cars, Project Overhauls & Restorations
I went into Precision and measured up a couple boxes of rb30 H-beam conrods and made sure that each rod length was exactly the same length, 0 tolerance. I then bought a set of forged JE + 0.040" "RB30DE" pistons with a 10cc piston dome. Honed out the conrod little end to fit the piston pin. Torqued up and measured the conrod big end made sure that they were all exactly on mid size (honed a couple) Bought an Excedy heavy duty ceramic/carbon clutch kit and Extreme Chrome Moly Flywheel Weighed all the pistons and pins, all were exactly the same weight Weighed the Conrod big ends, few were out, got them all to match the lightest. Then weighed the total rod weight, and took the difference out of the small end Sent the pistons off to get the top "tuff" coated for better heat absorbtion, and the pistons skirts teflon coated for less friction Set up the crank on the digital balancer, made it dead on 0 at either end, was out a fair bit due to the knife edging. Then added the fly wheel, machined that until that was dead on 0, then added the pressure plate and once again machined that until that was 0. Reason for this is, if at any point I need to changed any part, i.e the pressure plate, I only have to rebalanced the pressure plate Measured the pistons and calculated my piston to bore clearance to suit the motors usage. Roughed out the block to 0.003" before finished size with the rough stones. Then Put torque plate on and torqued up the head studs. Then using finer stones brought it down to 0.0005" before finished size. Since I'm using chrome moly rings it needs a slightly more finer finish, so I used and even finer set of stones. Finishing with the plateau stones to microscopically de-burr the cross hatches Using the machine is so much more accurate then hand honing as your can set up the spindle and stroke speeds so you can achieve a consistent 30° and 60° cross hatch angles. Dummy assembled measured the piston to deck height, the pistons sat 0.003" lower towards the rear of the block, so when I set it up on the grinder I made sure that the rear sat 0.003" higher Ground it so it was 0.001" deck height all around Washed and painted -
Gerg_R31's N/a Rb26/30De
Gerg_R31 replied to Gerg_R31's topic in Members Cars, Project Overhauls & Restorations
RB30DE (machine work) In Short RB26/30DE, Torque plate honed, knife edged crank, blueprinted, balanced crank assembly, balanced pistons and rods, balanced valve train, wet flow bench porting, mis-match cam profiles 10.75:1 stainless steel +1mm vlaves, supertech springs and titanium retainers, je forged pistons, H beam steel rods, trumpet intake manifold haltech PS2000 Introduction Naturally Aspirated RB30DE using the 3.0 Litre block and the RB26DE R33 GTR cylinder head. I was originally going to use a RB25DE VCT head, convert it to RB26 valve train and cams, but was going to try to work in the vct somehow, scrapped that idea and just bought the RB26 head Block The block I'm using, I pulled out of my old R31. Stripped it down, removed any crap that wasn't needed, then took it into work Removed the rods and pistons, crank, discarded the old welsh plugs and bearings and put it in the acid bath to clean off all the sludge, oil, gunk, paint etc Measured up the crank, it needed to be ground as it was just on bottom size. I know we shouldn't bead blast the blocks, But I did it anyway, then with a hand linisher I machined down the tops of the welsh plug housing to prevent it fouling on the exhaust manifold Knife edged crank counter weights to reduce the drag though the sump oil. It also took the weight of the crank from 24kgs to 23.7kg Drilled and grub screwed the big ends, fitted crank collar and ground both big end and main journals -
(this in my 2nd attempt at this build thread as the first thread I made I was not aware of a picture limit and became very messy and unorganised series of links and spelling mistakes etc) (big thanks to N1GTR for helping me re organise this thread) My R31 build thread and the RB30DE machining to long motor assembly details, Also there was a few things that I didn't get a photo of as somethings need both hands/ full concentration or I just plain forgot Introduction I bought this R31 Skyline Executive off the R31 forum for $1990 It came with, RB30E, auto, pod, extractors, 2.5" press bent exhaust, lowered, ti seats and 10 months rego The Start Build For a while I was restricted to P plate restrictions so I focused a bit on the cosmetic side of things I bought; Just Jap front bar and lip Fibremaster side skirts Fog lights Lenso 17" rims from Tempe Tyres I also rattle canned the the bumpers, and lower half of the doors in matt black, the two dark colours clashed so I used silver to split it up, then gave it numerous coats of clear. Later on I will get the entire car resprayed with the current colours and also have the car park dints and scratches removed Converted it to manual, C**t of a job, but thanks goes to guska for wiring it up for me I kinda got over the whole under breaking side of things so I decided to upgrade I bought R32 front calipers R31 front hubs R32 Slotted front rotors re-drilled to suit the 4 stud pattern I took the r31 hubs into work, machined the break rotors off, and gave it a 30° chamfer. Break disc fits perfectly Removed the old break calipers and hub, realized that the caliper bolt up pattern did not suit the r31 break caliper mounting point. Did a search and found out garage7 already had the r31 floating hub conversion, bought the "dog bone" adapters, received them amazingly quick. Put it all back together and then realized that one of the calipers had a stripped thread where the break line goes in. Took it to work, drilled it out put a 10mm x1.5 heli-coil in 3rd attempt, all on, bled, then the wheel fouled the caliper. Bought some 15mm bolt on spacers. Took it back to work, used the lathe to trim down the original studs and the 14mm high nuts 4th attempt all on, lines all bled out, spacers on, all torqued down to 80ft pounds, breaks significantly better. Will up grade the break booster soon Installed white line sway bars adjustable thicker front and thicker back Had a stack, other driver at fault, his insurance gave me a decent pay out The guys at Prestige Auto Repairs done one hell of a good job and at a good price;
-
have the main tunel groved like the gtr blocks, then use gtr main bearings pretty much everything for the internals sound pretty good, for a good strong bottom end, though ARP RB20/25 11mm head studs for a little extra strength wouldnt hurt
-
is it dedicated track? if so remove 0.350" off the counter weights in a lathe, and knife edge the front of the counter weights with an angle grinder. Then have it re balanced. The positive effects of this will reduce unsprung weight, the negative effects is it will effect the "throw" of the crank and will give you a really laggy take off from stationary which is not benifitial for a road car do you know the current piston dome/ dish/ valve releif volumes? or alternatively you could speak with nitto and they could organise a set of JE customer designed pistons (or custom for short) comp ratio, look in n/a mods explained, ive posted up the formular on how to work out your static compression ratio http://www.skylinesaustralia.com/forums/topic/362638-na-modifications-explained/ how much lift does the current cams have? too much lift with high compression will increase the risk of pistons hitting the valves due to bigger domes, or large amounts ground of block and head also the pistons can get fly cut or have valve relieves machined into them to help increase piston to valve clearance but they add more volume which will lower your comp ratio then you'd have to shave more off, fly cut again, etc becomes a limit to a point when you'd end up chasing your tail
-
from my understanding the rb30e was based on the rb20e holden were going to release the 202 in the VL but the emision laws changed at the last second, holden then spoke to nissan australia and together they designed the motor based on the rb20e, and for marketing reasons, holden went with the mx7 gear box, and turbo, where nissan went with the n/a'd options and rb20 gearbox toyota engine codes confuse the shit out of me though nissan; RB26DET R - ? ~ B - ? ~ 2.6 litre Dual ~ OHC T - turbo 2JZ-GTE - WTF? isnt this a 3 litre? its almost like someone was like "what do we call this?" smash the keyboard "that"
-
just mailed off my SAU membership, i will be there, not sure if ill do the track day yet, might just be a spectator this time around
-
rb26 head, mis matched cam profiles, wet flow bench porting, CNC cut valve seats, weight balanced valve train, stainless steel 1mm over sized valves with back cut on intake valve, supertech springs and retainers, GIZMO thermal intake gaskets, ram tube manifold i made from 6 tubes and a plate of alloy, spitfire coil pack, 6-2-1 equal length extractors rb30 block, steel H beam rods (with a 0.8mm hole drilled into the big end for an oil squirter like on the standard rods), "custom" JE pistons tuff coated tops and (teflon coated skirts) torque plate honed to suit chrome moly rb26 rings, knife edged crank, chrome moly flywheel, excedey heavy duty clutch, balanced entire bottom end, king bearings 10.75:1 comp, haltech pro sport 2000, 20 something row oil cooler, arp studs, nitto MLS head gasket also it helps to work in a machine shop with trade discounts, cost no idea how much but its past 10k easily maybe close to 15k, power not sure yet getting final tune though im more interested in response then HP figures
-
shitty phone pic, but there's my n/a rb26/30de engine bay pic
-
might want to re-word that in detail so i can answer that if your wondering what my rb30de made, i have bothered checking, havent finished the ramtube manifold yet, tough im more interested in response then dyno numbers
-
What? minimum piston to valve clearance should be 0.080" on the intake exhaust usually too far away to be a big issue in the rb heads Why? High revs and thermal expansion internal parts will expand, too little clearance = damaged pistons and/or valves How to check piston to valve clearance cover piston in clay/ play-do about 1/2 inch thick, put head gasket on, bolt down head, set timing, turn crank twice pull head off and with vernie calipers, measure from where the valve stopped to the piston top, side of the dome, top of the dome with mine, I had 0 deck height, 10cc pistons, 1.2mm head gasket, and 0.080" ground off the head, intake was 0.130" and exhaust was 0.250" with a 10.8mm lift cam and 10.5:1 compression
-
i got a standard r33 rb25 tb and upper plenum if your interested, cut flange off the upper plenum, cut and weld onto another upper half done
-
Addition to cams; with the RB30DE when selecting cams if the cams are rated i.e 3000-7000rpms on the rb25/26 head, with the RB30DE the same cams would be more 2000-6000rpms
-
Addition to porting think of it like a macca's thick shake, the standard straws you get with the cokes are useless with the thickshakes, but if you ask for their purple ones they serve with the smoothies, much better, but if you decide to go bigger and use for example a vacuum hose you'd just make a mess of things and will eventually be less sucessful then the first option, aka bigger ports is not always better. Also, the "polishing" of the ports is quite pointless, if the ports are too smooth fuel will stick to them, and in that few minutes while its running rich while its being tunned the unburnt fuel will cling to the exhaust ports. Valve Seats the RB motors all come out with the 3 angle seats from factory (30° crown 45° seat and 70° throat) the best angles for flow is a 4-5 angle on the intake with a 1mm 45° valve seat, and a radius on exhaust with a 1.5mm 45° exhaust seat. With addition the intake valve should have a 30° back cut on the port side of the valve for a better flow Addition to cams I have found with my n/a RB26 head on my RB30 block, doing the maths and calculations, as a rough guide the exhaust cam should have 10 degrees more duration at 0.050" lift Valve Springs I've read alot of posts where people try to get, or suggest the stiffest/ heaviest springs possible, this is not going to help. If they are too stiff they will chew out the cam lobes and pull the valves into the seats, end result need to buy new cams and valves and have new seat inserts fitted. If bigger lift cams are used and the springs dont suit, you will end up with "valve bounce" The correct method is to find the springs to suit the cams To find out if the springs suit, Seat pressure measure the installed height of the valve (spring base to under retainer, or spring base to top of retainer) use the spring base washer, spring (and retainer if measured with one) put it in a spring tester and pull it down to installed height, the seat pressure should be 70-90 pound on a N/A RB motor (add 10-15 per 14psi/1 bar of boost for forced induction as a rough guide) Springs to suit cam with the spring in the spring tester, find the measurement of the spring at coil bind (fully closed) then simple maths, coil bind - installed height - 0.100" = same or more then the cam lift. Less then the cam lift, you'd get valve bounce Blue Printing is the process of making every cylinder working exactly the same as the others, This is acheived by all the combustion chambers the exact same volume, ports all flowing exactly the same, all the con rod little end big ends and total weights all the same, all the pistons weighing the same, crank flywheel and pressure plate balancing, weight matching rockers in some applications, Pistons are of a better quality these days where the manufacturers promise each to be the same size, where as the old days all the pistons would vary and the bores would be "blue printed" to suit each individual piston Grinding RB25/26 Heads People have stated that for every 0.010" ground off any head will remove 1 cc. Some cases this is true but not in every case as the combustion chambers eventually tapper. From my experience and measuring, the first 0.020" ground off the RB25/26s will remove 2 CC's Grinding 0.080" off will remove 12.5 CC's Compression Ratios this is quite often assumed and guessed and where someone may think that they might have 12:1 they might only have 9.5:1 The formula to work out the static compression ratio Swept Volume Bore x Bore = Answer1 Answer1 ÷ 4 = Answer2 Answer2 x π (3.142) x stroke = Answer3 Answer3 ÷ 1000 = Swept Volume ( SV ) Compression Volume Head CC Piston dome/ dish volume Deck height (if 0 deck height leave out) Bore x Bore = Answer1 Answer1 ÷ 4 = Answer2 Answer2 x π (3.142) x block deck to piston crown measurement = Answer3 Answer3 ÷ 1000 = deck height volume Gasket Gasket Bore x Gasket Bore = Answer1 Answer1 ÷ 4 = Answer2 Answer2 x π (3.142) x Gasket thickness = Answer3 Answer3 ÷ 1000 = Gasket volume The Maths Head CC + gasket Volume + Piston dish Volume or - Piston dome volume + deck height or - if piston is above the deck = CV SV + CV + Answer Answer ÷ CV = Compression ratio thats all i can think of off the top of my head
-
what time, could have been me
-
arp main studs and 1/2 inch head studs might help
-
Power Mods That Will Carry Over To Your Turbo Conversion.
Gerg_R31 replied to KezR33's topic in Engines & Forced Induction
differences that i know of pistons run an extra 0.001" piston to bore clearance in turbo models cams the only difference is lobe seperation/ overlap which can be adjusted on twin cam motors with vernie gears valve springs as long as they can have 80 pounds of seat pressure and 0.100" more then the cam lift at installed height then they should be ok all other internal stuff wont be effected between turbo/ n/a