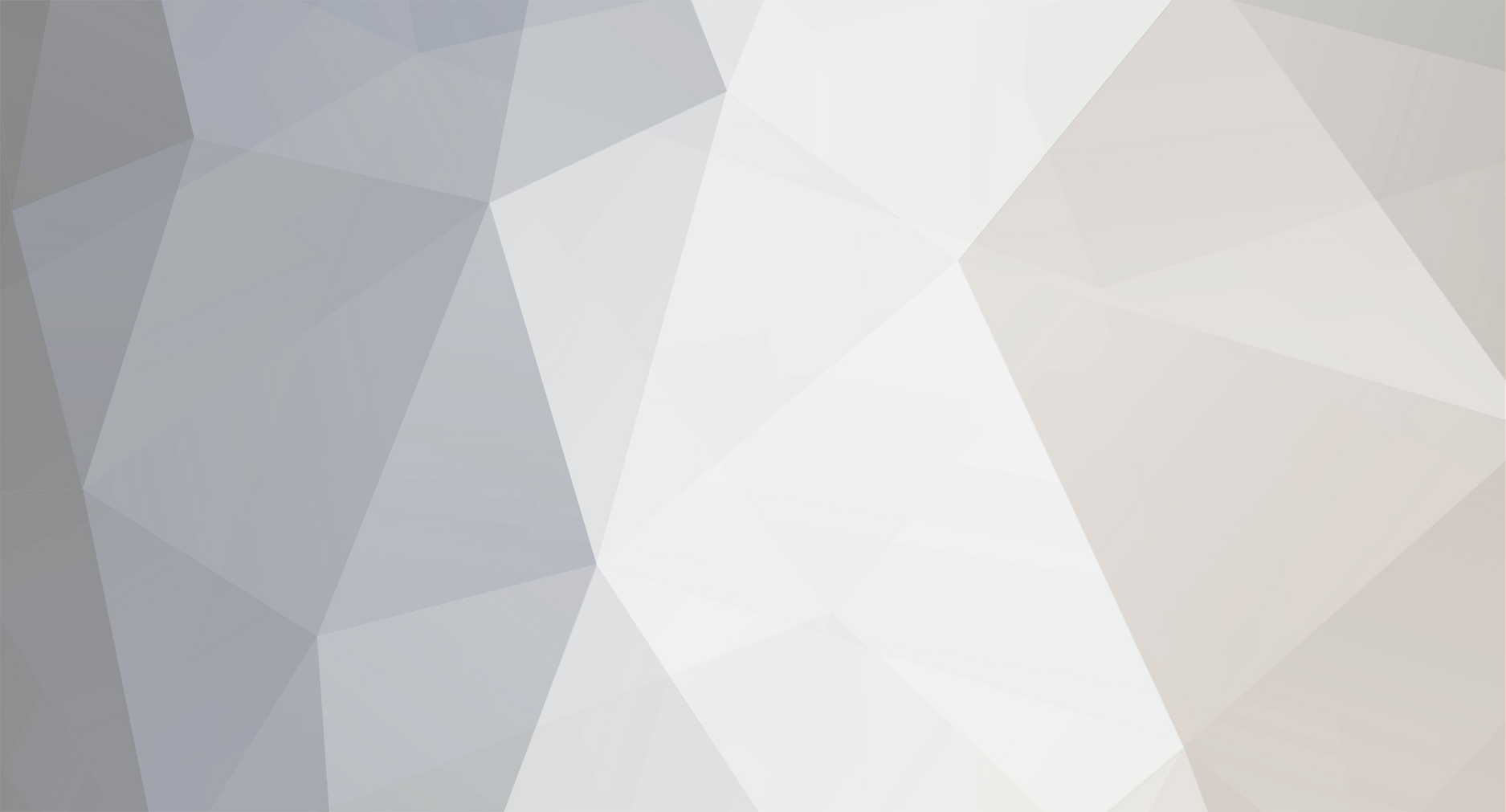
zoomzoom
Members-
Posts
898 -
Joined
-
Last visited
-
Feedback
0%
Content Type
Profiles
Forums
Events
Gallery
Media Demo
Store
Everything posted by zoomzoom
-
Realistically, an English translation hasn't happened in >25 years, but luckily you don't usually need to translate the whole billion page manual. I've used this tool before: https://www.i2ocr.com/pdf-ocr-japanese The manual has enough English headings and words to get to the section you need, then the OCR tool can help you decipher the remaining info on the page.
-
Give some thought to doing a big suspension and brake overhaul. I did that about 11 years ago and it totally changed the feel of the car. The steering was much sharper and the car tracked straight over bumps in the road, whereas before it was a wandering mess. It might take you a couple of months with the car on stands, but it's given me a decade of rewarding results. Given the age of the car, you could probably assume the following are stuffed: All suspension, subframe and steering rack bushes. I used Superpro polyurethane replacements. Inner tie rods and outer tie rod ends on the steering rack. All ball joints, 2x for each front wheel (on the lower control arm). Same as skyline GTR. Rear suspension has 1x ball joint. Certain suspension arms can be replaced with adjustable units, like the caster arm, and upper control arms for the front suspension. This allows the alignment to be set more accurately than those crappy eccentric bolts that are standard. Having everything stripped down is a good time to get to things like the driveshafts. While they are very good quality and long lasting, the boots inevitably crack and lead to the contamination and destruction of the inner joints. Over the past year and a bit I've replaced all 4x driveshaft boots (ie all 8x boots). This gives you a really solid base to then start piling on the mods.
-
R33 Rear Wheel Bearing Replacement
zoomzoom replied to No Crust Racing's topic in Tutorials / DIY / FAQ
Yep I soaked them in WD40 overnight and came back the next day with a mallet. They were indeed stuck due to corrosion, but came loose after a few minutes of hitting. It's definitely easier to do this with the hubs out. Also on the issue of presses, I have a 6 ton press which has been fine for every bush and bearing I've had to do over the years, including this job, but the downside is the platform is quite small, making it difficult to mount a full hub on them for pressing. I was just looking up a 20ton press for the wishlist. -
They seem to be getting scarce on this side of the pond too! Mine is modded to what I would consider "Stock Plus", basically sharpened suspension, shift kit in the auto trans, slightly larger turbo and an ECU resulting in 200awkw. Gives it more pep without being too laggy, and also not on the brink of snapping something. Ive owned it for 15 years now, myself among others here can give you a fair few pointers on what should be done, and what shouldn't be done.
-
In relation to this video: A few things in here really made me facepalm. It uses belts to drive the cams and oil pump, which wouldn't be too remarkable except that they're INSIDE the engine, and while I would hope that they used a special composition belt, the state of the belts in a short service life leads me to think they're pretty much standard rubber timing belts that last about as good as you'd expect bathed in hot oil their whole life. In this teardown, the belts appear to have caused the destruction of the engine. Also, the timing belt isn't keyed to the crank. Yep, that's right, it only keeps timing if the toothed pulley remains torqued enough. I shouldn't be surprised that this exists, but I keep wondering why it exists. Even an amateur engineer can see these obvious failure points, and yet a company with more than a century of experience in motor design has made this engine. Some things might be easily explained by cost cutting. Not keying the crank technically saves on a machining step. But belts inside the engine? The more sinister side to all this is 1) planned obsolescence after about 5 years, and 2) difficulty in maintenance and repair by either the consumer or 3rd party repair. Take for example the timing belt, it's no longer a matter of simply synchronising the belts teeth to the correct teeth on each pulley. It now has an infinitely variable pulley which needs some special tools to get it synchronised. Does anyone have any insight into the industry? I can't believe these are ideas originating with engineers, but rather the accounting department. Or is that even too generous to all engineers, is there also a culture of amorality in which they're in the business of creating the ultimate disposable consooooomer item? Let's not forget VW's dieselgate, there's plenty of engineers willing to go along with some shady stuff.
-
R33 Rear Wheel Bearing Replacement
zoomzoom replied to No Crust Racing's topic in Tutorials / DIY / FAQ
How tightly should the bearing assembly be mounted in the hub? Judging by this thread it should come out with a basic puller, however I bent a 3 jaw puller trying to push the bearing out of the hub. I've had to remove the entire hub from the car, but it wont fit on my 6 ton press. Even then it looks extremely difficult to support the cast hub in order to apply force to the bearing. I'm struggling with ideas. -
Just changed my water pump which was in there for around 14 years. Impeller was spotless, no perceptible play in the bearings but maybe the tiniest bit of moisture got past the seal. That's definitely a fair bit larger than a standard impeller though.
-
Tips for removing crank bolt on auto RB25
zoomzoom replied to zoomzoom's topic in R Series (R30, R31, R32, R33, R34)
Here's the tool I came up with if anyone needs some ideas on making their own. This is using the scrap I had lying around, just happened to have an ideal sized piece of steel pipe. The "teeth" are bits of M12 threaded rod, (obviously unthreaded would be fine too), and spaced out at 120 degrees. Just got the bolt loosened by myself, tightening shouldn't be too much of a hassle now either. -
Tips for removing crank bolt on auto RB25
zoomzoom replied to zoomzoom's topic in R Series (R30, R31, R32, R33, R34)
Yep, just got the radiator out and I think I'll make a tool to hold the pulley. Forget taking the starter out LOL Funny that even the Nissan manual specifies a ring gear locking tool that requires taking the starter out. Feeling a little nervous about those M6 threaded holes. The puller that I have only comes with some imperial bolts and they're all like M10 or M12 equivalent in size. -
Tips for removing crank bolt on auto RB25
zoomzoom replied to zoomzoom's topic in R Series (R30, R31, R32, R33, R34)
I'll probably tackle this over the weekend. The manual says to remove the radiator, do you guys bother with that? -
Tips for removing crank bolt on auto RB25
zoomzoom replied to zoomzoom's topic in R Series (R30, R31, R32, R33, R34)
Thanks. I'll procrastinate on the whole thing for a little longer. -
Tips for removing crank bolt on auto RB25
zoomzoom replied to zoomzoom's topic in R Series (R30, R31, R32, R33, R34)
Just double checking how you're locking (and accessing) the flex plate with the engine+trans in the car? Is that using a screwdriver in a vent/breather port directly under the bell housing? -
Pretty much as per title. I have to do a timing belt / water pump replacement so I'm trying to figure out the hurdles before I get to them. What are some ways of preventing the crank from turning while loosening or tightening the crank bolt with an auto gearbox? Maybe jamming something into the starter ring gear?
-
A few things to consider: Is there a good quality aftermarket replacement arm which already has new bushings but also adjustable camber? Rather than the eccentric bolt? Many years ago I replaced all my bushings front and rear with superpro polyurethane bushings. Sure they've been fine. But the castor isn't adjustable and is slightly out, the camber adjustment bolts aren't the greatest and most secure way of adjusting them. If I were to do them again I'd probably just replace the arms with aftermarket ones. I used a 5 ton press to get everything out. The biggest pain is having a wide selection of metal pipe pieces that are strong enough to press things out with. The rear hub bushings gave me PTSD.
-
The 2 shift solenoids form a 2-bit number which describe the forward gears. But don't assume, 0 is first first gear, and 3 is 4th gear. I think from memory b00 is actually 3rd. The ECU loom also has wires which are digital states for when central shifter is in reverse, neutral or the forward gears. Coupled with some microcontroller logic (or lucky you if your ECU is modern and has some flexible inbuilt programmable logic), you could determine what gear is currently active, and drive an LED digit display. Forget the speed vs rpm method for an auto. P.S. From one of my micro programs the solenoid combos are as follow (LSB being solenoid 1) b00 : 3rd gear b10 : 2nd b01 : 4th b11 : 1st
-
The welsh plugs are used to block off the cylindrical accumulators, which become pretty obvious once you unbolt the valve body. They just hammer in. Just the mindful there's large springs that drop out when you remove the valve body. Whatever you buy should include instructions on which accumulators are plugged and what springs need to stay in. My valve body kit included the welsh plugs.
-
It's a modification to the valve body of the transmission, a unit which is bolted onto the underside of the transmission after you take the pan and oil pickup tube out. It contains a maze of hydraulic pathways and it affects the pressure and flow to the various clutch actuators. In practical terms it will increase the shift speed, remove the clutch engagement overlap between gears and I think it also increases flow to the cooler. Other components may include welsh plugs for blocking some of the accumulator cavities (I think they are called that) which are there to soften engagement of the clutches. I installed an MV Automatics unit around 8 years ago. It was based on a core return process - they send a complete modified valve body then you send back your original, after which they refund a deposit.
-
A shift kit is highly recommended.
-
Check the variable cam timing solenoid. They can fail and they result in low end torque being even more sluggish than usual.
-
I'm running an adaptronic 440 as a piggyback. It controls fuel delivery, ignition, and the idle air solenoid. I'd like to get a more modern one, with enough outputs for full sequential fuel and ignition. I just cut and splice what I needed to on the loom, it's only wire afterall. With a universal independent ECU you can always put it on another vehicle later too.
-
Manual valve body in stagea auto
zoomzoom replied to oxford1327's topic in Four Door Family & Wagoneers
If you're willing to sink the funds into a box rebuild then I'd be looking at an aftermarket trans controller too. Apart from retaining the choice of auto or manual gear selection, variable line pressure, and the ability to tweak all the shift and lockup points is a benefit once you've tuned the engine. Also I highly recommend retaining and optimising ignition retarding logic on gear changes, to maximise the life of the box, reduce shocks to the rest of the drivetrain, not to mention the inhabitants of the vehicle. -
Manual valve body in stagea auto
zoomzoom replied to oxford1327's topic in Four Door Family & Wagoneers
Any other variables like how much throttle you're giving it when the gears flare? Once the ECU actuates the solenoids, gear flaring really becomes a mechanical problem. The auto control should be similar to a series 1, in that the line pressure is determined by throttle position, not how much torque the engine actually produces. Once you start introducing tuning and different turbos, you can imagine the engine producing more torque than stock at a given throttle. The type of transmission fluid can contribute to flaring. Ironically I tried the genuine nissan fluid years ago and it flared on gearchanges (back when I had a stock valve body), this was solved when I used transmax z. In terms of dealing with increased torque from the engine, the standard line pressure ballast resistors should be replaced with a higher value or better yet a 2 step system works well, if you have an output from your ECU available (for example I have 2 resistors to vary the resistance once the manifold pressure reaches a few psi of boost) Standard value is around 15ohms from memory, which I increased to 25ohms at low throttle, then switches to a couple of kilo ohms under boost, essentially maximising line pressure. Gets rid of flaring at part throttle with boost. -
Manual valve body in stagea auto
zoomzoom replied to oxford1327's topic in Four Door Family & Wagoneers
OK https://xyproblem.info/ Maybe specify whether you actually want to have to stir some lever all the time under full line pressure or whether it's intended as a stop gap measure for your real problem. What do you mean by the ECU fluffing around? -
Wash your mouth out, that F40 rear end is ruining the gorgeous AU lines.
-
Lol @ the idiot OP shopping at supercheap. OK, occasionally they have the odd decent item at a decent price, but mostly it's over-priced poor quality stuff. Sometime soon after I must have switched to getting all my oil at costco, getting Nulon full synthetic around $7-8 per litre when on special. Get oil filters in bulk online, too. Barely set foot into supercheap auto anymore. I ran that chief/cherokee stuff in a few econo cars and never had an issue, but just switched to nulon when I could get full synth stuff at the same price. I must have run the stagea on nulon for around a decade now, and the only difference I could remember is that some semi-synth stuff I used caused lifter noise at startup, went away after switching to Nulon.