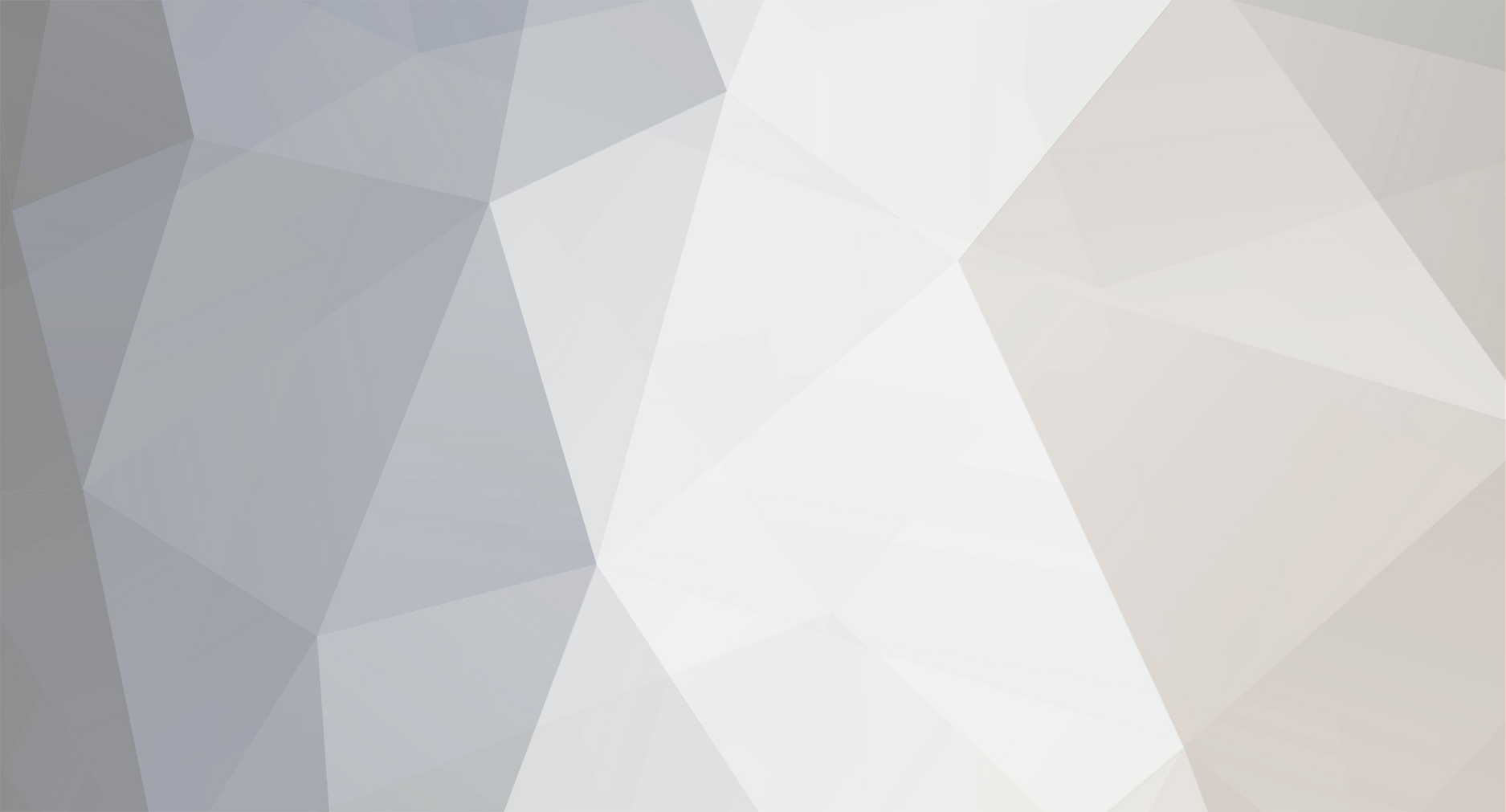
HtwCHACtkh
Contributor-
Posts
216 -
Joined
-
Last visited
-
Feedback
100%
Content Type
Profiles
Forums
Events
Gallery
Media Demo
Store
Everything posted by HtwCHACtkh
-
What Not To Do To Your Ecr33
HtwCHACtkh replied to HtwCHACtkh's topic in Members Cars, Project Overhauls & Restorations
Thanks for all the replies all replies, warnings, concerns, flame and advice. I normally jack from the official jack points when I do oil changes and when I did the torsion tests. The only reason I was trying to jack the rear of the car in a different way was because I needed an alternative method as my jack won't lift the car high enough for the stands and wanted a method other than using wood ramps to see if it were possible. I didn't go under the car with a phone book holding up the jack, I quite like living. The only reason I haven't done anything recently is because Christmas is unexpectedly busy this year for me for a change. The jack and stands are Orcon and set me back ~$150 all up a few years back they passed "standards"; I assumed (god damn hoped) that was good enough not to break on me. I'm starting to think ramps are a very good idea. As for research, I'm only really doing modifications which I have heard do have some benefit and nothing drastic (The stuff I'm not confident with I'll take to the shop). I know there is a lot of information on this forum and it may seem like I'm proving what's already proven however the most proof readily available is a word or another qualitative result of a modification which is all heresay - I wanted to turn that into numbers and make it available for people to see so it can be settled. For example, on this forum from the words of some very reputable people regarding strut braces is that the benefit is questionable and may simply be a placebo effect. My area which I am trained is definitely not Engineering or even Theoretical Physics - it is merely a hobby. I am a trained experimentalist. I really don't know why someone was questioning why I was doing weight reduction though... I thought it was quite reasonable considering the amount of time I didn't need the spare tyre and jack in my boot and the fact that I don't have road side assist or go on long road trips often lugging it along all the time is purely out of anxiety. I've reduced the mass of the car by over 1% without even thinking and given Acceleration = Force ÷ Mass - for the same force but mass now 0.99 of the total (Multiply by 1 ÷ 0.99 both sides) acceleration improves by approximately 1%, not to mention deceleration too and cornering all of which follow the same concept. That surely has to be a reason to remove weight. -
What Not To Do To Your Ecr33
HtwCHACtkh replied to HtwCHACtkh's topic in Members Cars, Project Overhauls & Restorations
Yes, I'm not saying no cooldown period at all is necessary but rather driving close to idle rpm for the last few moments of your drive will cool it quicker than leaving your car in your garage bonnet up. Keep in mind this is a street car and everything I find is only applicable to this situation. This hypothesis is also supported by the fact my auto turbo timer seems to go on forever after turning my car on for about a minute letting it idle in the garage then turning it off. Marlin: Thanks for the heads up. I'm not sure if you understand but the structural damage to the rear strut brace is not on the car. I used two bolts and tightened them a bit too much before adjusting the brace itself which made it bend a bit around the bolt before actually tightening am aware there is not meant to be any tension along the strut brace in normal position - there wasn't any, no creaks no nothing it was tight enough to stop the thing from rattling - the bending around the bolts made me have to tighten it excessively to make up for that slack. Either way, if you believe it's too tight - I'll hand tighten it next time. -
Twin scroll turbo, single outlet manifold for this setup. You want to make all the gas go through the turbo faster by making the area smaller until it starts to create backpressure in which case you begin opening the valve on the turbo slowly until it eventually is open entirely flowing entirely AFAIK.
-
Great work Shaun and Stao, I'm interested in seeing how this progresses. For those who doubt the theory consider bernoulii's theorem. First assume the exhaust gas is not getting compressed (density is constant) and flow within the system is ideal, then the flow out of the head must equal the flow out the turbo. If the area to the turbo is halved then its velocity must increase by a factor of approximately 1.4 (Bernouli's theorem, Conservation of Energy). Momentum is then consequently increased by about 40% => 40% faster spool time. So in an ideal theoretical world - it works great but a lot of R&D is required to reduce ineffeciences. Stao: Is this sort of setup possible in one of your super street turbos?
-
What Not To Do To Your Ecr33
HtwCHACtkh replied to HtwCHACtkh's topic in Members Cars, Project Overhauls & Restorations
Yes and Yes to both things. I measured the temperature the pod filter because I didn't want to bring in other variables like effectiveness of the intercooler. I was only wanting to test the temperature of the air being sucked in - if you find there's a fault in my method please let me know where it is - I'm interested in finding the truth. EDIT: I'll keep my multimeter with me and do a long distance (30 minute 25 km drive or so) temperature test tomorrow involving some inner street traffic, main road traffic and freeway driving. I will measure at a 30 second interval and log it to my laptop - unfortunately I don't have time for anything else tomorrow. -
What Not To Do To Your Ecr33
HtwCHACtkh replied to HtwCHACtkh's topic in Members Cars, Project Overhauls & Restorations
Captains Log: Entry 3 - 18/12/2011 Today I had about half a day to spend on the car, tomorrow I will be spending none on the car. I intended to test front strut brace effectiveness which turned into a fail.. So I fixed my "hot air intake". Once again, I'll do this in chronological order. Before taking a start on the front strut brace I took some photographs of the current front end of the car. The rocker covers I began sanding down while on the engine when I was still in semester to test the concept and will be completed hopefully these holidays. The front bar had someone back into me also during semester also hopefully to be fixed these holidays. I began the work on the strut brace by taking some measurements of the fronts regidity without the front strut brace anagolous to the method of testing the rear. Pictures of the front strut brace can be found in the very first post. Results: Unloaded: RHS: 357.0 ± 0.5 mm LHS: 355.0 ± 0.5 mm No strut brace - Loaded: RHS: 383.3, 411.0, 445.0 ± 0.5 mm LHS: 362.5, 371.0, 382.5 ± 0.5 mm So with that done, I began on the task of installing the front strut brace. I didn't believe it could be hard, 4 bolts... Except that the bolts I swear have never been taken off in the cars life and were extremely tight!! So I soaked them in RP7 and managed to get the inner bolt undone on the RHS strut tower. The outter bolt was being quite stubbon then this happened: I had just been driving the car so I thought it might be very hot and the metal had expanded, so I put some ice on it to attempt to cool it down to make it easier to take off. But that didn't help and I could feel my cheap tools wanting to break soon too, in the end this happened: Yet another fail to add to the list, I told you I would report a lot of failures. Now I swearing to myself quite loudly inside my head, luckily no mind readers were around to hear me because they would get quite a shock! Now I need to source a new set of these bolts, does anyone know where I can get these? To get my mind off the epic fail of rounding the bolt I decided to instead work on my "hot air intake" today seen here: During the mid semester break I made this heat shield from 5mm thick acrlyic from Bunnings. The curve took a lot of fiddly work to do but it fits snug, I heated it up using Mum's BBQ and her oven mitts to hold the thing and bend it - it's really quite hard to do. However I'm not really that happy with the way it turned out in the end and it doesn't fit too well. So instead I decided to cut the top off the damn thing, keep the curve and side bit and measure up and cut up a new top and glue the two things together to make a shield. After sanding to make them fit nicely.. I used a high heat hot glue gun to glue the two things together. There was another fail between these two points where I had the garage door open when I was trying to glue the two pieces together and the glue cooled too quickly.. I used turpentine and sanded down the glue I couldn't really pull off too easily. This stuff holds quite hard, I'm very impressed. This new setup fits a lot better, I like a lot better - it's really much much easier to do to; I highly suggest anyone making a heat shield to follow this method. If this was any other build thread, I would skip to the finished product all put together and all and say something like "feels more responsive, feels cooler to the touch" but this thread is different. Back on with the old setup and take some measurements! Results - No heat shield: Measurements were taken before going on a drive with the car off and then right after a drive around the same circuit at similar velocities and accelerations if possible unless mentioned otherwise. ATMOSPHERIC TEMPERATURE: 22 degrees No heatshield before: No heatshield - idling for a very short while before going on a drive and temperature was rising: No heatshield - after a 4 minute drive around the block max speed 60km/h minimum stops The results were shocking - and when I opened the bonnet after the drive it was no where near as hot as what it normally is after a thirty minute drive down the freeway. Regardless, I carried on. Assembly of the my new heatshield and pictures of yet another fail, that brings it three today only two of the screws line up to hold it all together - which isn't so bad because I only had three screws to begin with. A picture of the reasonbly snug fit around the curve. Note: I actually did want this to be a fully enclosed air box but I quickly realised the amount of extra design time that would take and instead decided to test this as a proof on concept. Results - Heatshield: The test drive was the same as the first one except I got stuck in very heavy stop start traffic as I decided to drive through a street with beautiful Christmas lights the first time through which got really busy around this time. Heatshield - Just before the drive: Heatshield - Just after a 6 minute drive max speed 60km/h quite heavy start/stop traffic for one quarter of the drive. The results truly do speak for themselves but I still had some energy in me so I didn't want to stop there - I remember I had an old air guiding pipe that I used to use in my computer overclocking days way back and since I have a turbocharged car and now have a FMIC without return hosing I have a 2.5" hold right under where the air filter is - I've always been told that this was too small to be of any benefit as a cold air intake - I decided to put that to the test and one of the reasons I took out my indicators on the front bar and relocated them to the parkers is because this is the highest pressure part of the car and is absolutely ideal for a cold air intake. This isn't not necessarily a permanent modification but rather a proof of concept. A picture of the lil pipe: Installed inside the car: Held in place with a zip tie at the front of the car: Results - Heatshield + CAI: Once again, I went on the same circuit path this time there was moderate start stop. I was able to position the heatshield to provide more isolation from the rest of the engine bay too. CAI + Heatshield - Just before drive: CAI + Heatshield - Just after 5 minute drive max speed 60km/h with moderate start/stop traffic for one quarter of the drive. The results speak of themselves. I also took some more measurements, while my car was meant to be "cooling down" with the turbo timer running the temperature actually increased: Also, the ambient temperature under the bonnet at this time: Conclusion: I think the results really speak for themselves, I don't really have much to say here. One interesting thing to notice is the increase of intake temperature when idling with the turbo timer which suggests that it is true that driving your car softly for the last 30 seconds - 1 minute before pulling up is more effective than using a turbo timer! -
What Not To Do To Your Ecr33
HtwCHACtkh replied to HtwCHACtkh's topic in Members Cars, Project Overhauls & Restorations
Not sure what you're questioning but everything I've said so far is quite real. I got more stuff to upload from todays work and fails... I did my "hot air intake" today and got some good results. Writing it up now. -
Bump, getting a lot of questions about postage costs for the subs. Australia Post won't post them as they're too big. I find http://transdirect.com.au/ to be very very reasonably priced and provide a great service. My post code is 4116. The dimensions of the subs are approximately 60x90x30 cm and weigh approximately 25kg. With that information you can work out the postage for yourself. Offer away guys. Need this gone.
-
What Not To Do To Your Ecr33
HtwCHACtkh replied to HtwCHACtkh's topic in Members Cars, Project Overhauls & Restorations
Thank you all for the kind words. It's reassuring to hear that what I'm doing is not stupid. Captains Log: Entry 2 - 17/12/2011 I didn't get much time to spend on the car today due to life and stuff... I however did get to spend 30 minutes or so doing some more testing on the rear strut brace because I was very unhappy with the results. I measured the mass of the rear strut brace and the lift on either side under more load. Results: Mass of strut brace: 1.1kg Results Unloaded: RHS: 417.0 ± 0.5 mm LHS: 400.5 ± 0.5 mm Results Loaded with no strut brace: LHS: 432.0, 482.5, 522.5 ± 0.5 mm RHS: 405.0, 419.0, 428.0 ± 0.5 mm Results Loaded with strut brace on hard: LHS: 432.0, 483.0, 523.0 ± 0.5 mm RHS: 405.0 421.0, 430.0 ± 0.5 mm Positive results! I was ecstatic to see these results - it answers almost all of my previous theories of the conclusion I made yesterday. I made a small plot of the two series of data to get a good idea of what's going on and regressed them linearly. Note: Linear regression against data of this sort is not the most accurate and I really did it for a quick comparison sake with a reasonable approximation. Conclusion Comparing the gradients of the two regressions having the strut brace in place makes the rear approximately 8% stiffer. This is at a consequence of adding 1.1kg of mass evenly across the rear of the car. I believe the approximately 8% increase in stiffness is a good upgrade for 1.1kg of mass and $55. Also, I have observed some structural damage to the strut brace from being tightened too tightly with only two bolts instead of four (seeable in the pictures in Entry 1) I would like to repair this before installing once again. Cheers EDIT: Added in the two "Unloaded" data points in the series for a bit more accuracy. -
What Not To Do To Your Ecr33
HtwCHACtkh replied to HtwCHACtkh's topic in Members Cars, Project Overhauls & Restorations
I couldn't wait till tomorrow and I started today, so today you all get what I promised. Analysis and A LOT of failure! Without further ado. Captains Log: Entry 1 - 16/12/2011 Today I set on task of installing a rear strut brace and testing its effectiveness in stiffing up the car against torsion. Since I was at the boot, I did a few things there too. In chronological order.. I began with some weight reduction: Out with the jack and tools... I also weighed myself clothed at 74.3kg and then weighed myself clothed holding the spare and read 89.3kg. I removed the spare. Total saving so far 18.4kg I started looking around, exploring the car to see what's around everywhere. I found a thick clear tube behind the LHS rear panel that I have no idea what it is for there's also a few boxes on the LHS near where the jack mount was that I'm not sure what they are. On the RHS, there's a little plastic thing that has a flap that opens up to the outside world!! I took a picture of it from outside the car. I assume that this little vent here is to allow for the air to be displaced while closing the boot. I'm not sure if the plastic thing there is really necessary or if it can be removed safely for weight reduction. Anyone able to shed light on this? By the way, I have Billstein Shocks and King Springs - I don't remember if I mentioned this. A picture of Mum's Garage and my Skyline at this current day. Notice the differences to the earlier pictures when I just got the car seen in the first post. Because I don't have many tools, I decided to look inside the toolkit that came with my car which I hadn't looked at yet. (Hence why I thought it were reasonable to remove it. There's the usual jack and the thingo you use to open up the nuts on the wheels and also this cool little thing used to stop your tyre from rolling back when jacked. Cute.. So I decided to jack up the car, I don't know why... But my hydraulic jack didn't lift the car high enough for me to put the stands I have underneath it - so I had to improvise like so... Which was a FAIL... I caused this damage here: I will need to determine a new way to jack up the car... Now, I thought to myself after I did that damage.. why am I jacking up the car? Because I didn't need to.. So I got to the idea of installing the adjustable rear strut brace I picked up second hand for $55 with no bolts. To test the effectiveness: In order to test the effectiveness I measured the height from the ground to the top of the side skirt with my measuring tape flush along the edge closest to wheel. I did this unloaded, loaded with no strut brace, loaded with strut brace on soft, loaded with strut brace tight. Uncertainty was chosen due to parallax and the slight gradient on the side skirt. Results Unloaded: RHS: 417.0 ± 0.5 mm LHS: 400.5 ± 0.5 mm Results Loaded with no strut brace: RHS: 432.5 ± 0.5 mm LHS 405.0 ± 0.5 mm Here's a picture of it installed set to as soft as my hands used to be before I started this project. I only had two bolts that fit though: Results Loaded with strut brace on soft: RHS: 431.5 ± 0.5 mm LHS: 405.5 ± 0.5 mm I then tightened it up as tight as she could go.. A consequence of having two bolts though is that the metal around the bolts bent... I put the bolts on the inside now instead of the outside to hopefully try bend it back but no avail. This should not effect the results as they were installed extremely tight. Picture of FAIL NUMBER 2: Results Loaded with strut brace on hard: RHS: 432.0 ± 0.5 mm LHS 405.0 ± 0.5 mm Conclusion: No measurable difference in torsion was observed at all under these loads. This goes against what I expected since it seems to be such a popular little modification for people to do and the GTR's seem to come with one. Some possible explainations I have is: That this load is too little for the strut brace to be of any measurable benefit. The strut brace is not installed correctly Rear strut braces are a waste of weight in the ECR33. -------- Also, I removed my old little active subwoofer that was at the back of the car and front indicators (installed indicators in the parkers, they're LED's and the relay is going fast I will fix that later) a little while ago... Weight reduction saving 4.8kg brings the total to 23.2kg. Not too shabby. By the way, I know I forgot to weigh the strut brace before I put it in... Cheers -
What Not To Do To Your Ecr33
HtwCHACtkh replied to HtwCHACtkh's topic in Members Cars, Project Overhauls & Restorations
I don't even remember, the exhaust has been in the car for a while. I'll worry (i.e. gut) the cat when I get there. However, good news! I've finished all my exams now and holidays have started. So the fun begins. -
I have the stainless one running a low powered setup, no problems. Stainless steel is lighter than mild, and shinier. I suggest ceramic coating the thing before you put it in though I wish I did, the front pipes sure do get hot!
-
That's really not too bad. It would definitely make it competitive pricewise if you're going to keep the standard exhaust manifold. +1 to what R31Nismoid said. If you're willing to spend some cash then a lot of doors open.
-
GT2835 Pro S or Hypergear come to mind quickly. I don't think there are any bolt on Kando's which seem to be all the rave at the moment.
-
What Not To Do To Your Ecr33
HtwCHACtkh replied to HtwCHACtkh's topic in Members Cars, Project Overhauls & Restorations
Cheers for the replies guys, one exam down.. 3 more to go.. Two scary ones tomorrow and finally an even scarier one after that. 93WIZ: Mum's garage really isn't pimping with tools at all other than my set of small tools ($10 socket set, $20 screwdrivers, $20 jack, $15 soldering iron, $170 multimeter, $100 dremel, other random stuff + my dad's power tools) so there will be a lot of buying/making of tools and experimenting with them as well. I will buy a tool and fabricate something myself if it is economically more viable in the long term. This is my first build and I am a young fellow and I really want to give this a "fair shake of the sauce bottle" and maybe gain some useful skills for the future too. -
Hijack.. What is that thing for anyway? I have an EBC that needs to bleed pressure build up between the actuator and the solenoid - can I plumb the bleed back into that?
-
The words say she's trolling but the pictures say she's not... Internal battle ftl.
-
Need Help Choosing What To Get, My Old Stuff Blew Up.
HtwCHACtkh replied to MrRx7s3's topic in Car Audio & Electrical
What type of music do you listen to? It looks like the Kicker subs are quite rigid which means it will be good for quicker "kicking" bass with less distortion as the sub can more quickly return to its neutral position for the next note. While the clarion allows for more excursion which means a heavier kick but it will take longer for it to return to its neutral position - so under quick sucession of bassy notes it may start to distort. I can think of many amusing analogies ranging from nerdy to inappropriate to describe how the two subs are different. The most public forum friendly one I can think of is a spring. The kicker is a stiffer spring (tension not compression spring) so requires more energy to reach a certain amount of kick (excursion) however returns back with a snap; while the Clarion is a softer spring which will kick harder for the same amount of energy but return slower. So my conclusion (probably wrong): Kicker if you listen to music which has a quick beat, Clarion if you listen to music that has a slow beat. -
How can you be sure of the plenum providing even air intake to each cylinder? i.e. How did you flow test it?