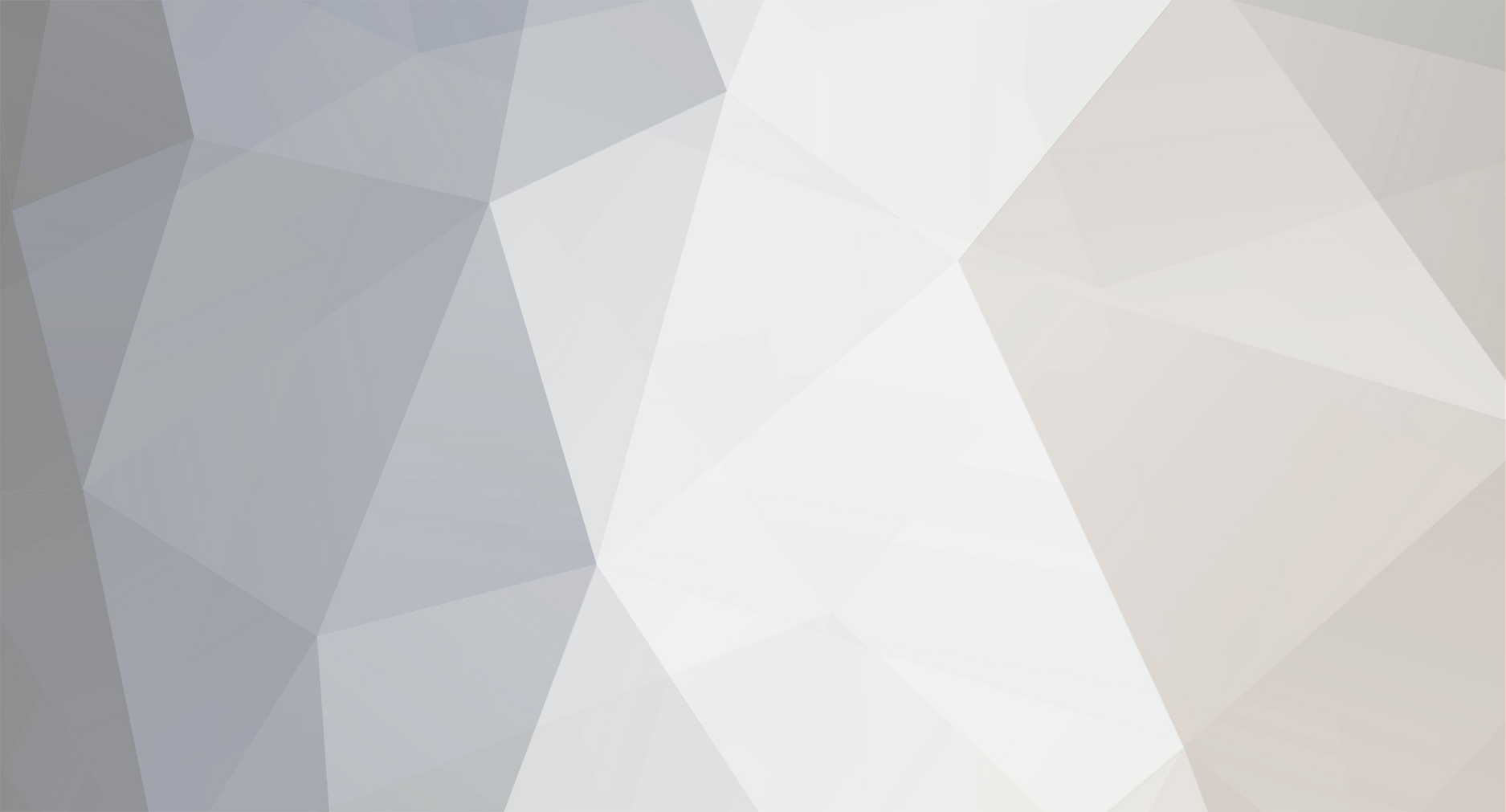
rockvale
Members-
Posts
6 -
Joined
-
Last visited
-
Feedback
0%
Content Type
Profiles
Forums
Events
Gallery
Media Demo
Store
Everything posted by rockvale
-
Gearbox oil leaking into transfer case
rockvale replied to stealthfoz's topic in Suspension, braking, tyres and drivetrain
Ok lets try and help the guy, it does not matter how you fill the transfer case or gearbox as long as the correct type and amount of oil is used, un qualified comments by idiots dont bother putting your comments up. now to your issue of gearbox oil transferring to the transfer case via your centre plate?? (hoping this is what is happening) 1. Can occur if transfer case pump main shaft seal is worn, damaged, or not installed 2. Seal on Shifter Rod worn, damaged, or not installed, 3. But this issue of transfer of gearbox oil to transfer case oil is generally cause by a broken magnet on the transfer case drain plug (Eg the magnet is entirely missing from the transfer case drain plug) What happens over time is the metallic compounds do not collect on the transfer case drain plug magnet (because it is missing), instead the metallic compounds block the very fine filter of the transfer case oil pump filter which creates a high suction vacuum substantial enough to suck gearbox oil past the transfer case pump main shaft seal. The result becomes evident when the transfer case fills up with the mixed oil and overflows out the transfer case plastic breather hose and onto the hot exhaust causing smoke. If your magnet is not present on your transfer case drain plug, you will need to remove and wash clean the transfer case pump filter and replace 1. The transfer case pump main shaft seal 2. Replace the transfer case drain plug (one with magnet in good condition) Yes, I have done this twice for customers R32 GTR'S, sorry, but not a small job for such a small damaged magnet on a drain plug!!! -
So many times I read threads on SAU about additions to the OEM RB26 ignition system, yet no one has completely or conclusively understood the capabilities of the std ignition system, I have made 500kw at all 4 tyres with std ignition at 0.024". Yes I have also fitted a HKS DLI which by the way does not increase you max secondary ignition voltage, it increases the current, and the engine does run a cleaner spark plug So the question that needs to be answered is why can some Rb26 run extreme power levels and others can not with the std ignition? Simply because the ignition is breaking down, but where, so following test will identify your ignition problem. 1, Firstly you will need 6 x brand new plugs gapped to 0.6mm, 6 x sachets of high temp dielectric silicone greese (jaycar sells it) an aluminium sheet about 800 x 400 x thickness does matter, but say 1,0mm, you will need to drill a 9mm hole in the top left hand corner of the shortest side 2. Ensure ignition is OFF, Remove ignition coil loom from coils, remove coils from engine, eg 2 off x 3 coils in Al coil mounting brks, remove std ignitor from engine cover, remove old spark plugs, liberally apply dielectric silicone greese to the top and insulation of each new plug and install into engine 3. Remove 6 x injector connectors, 4. Remove crank angle sensor clip, ensure you witness mark around the washers of the 3 x crank angle bolts before you loosen and remove crank angle sensor from the motor, connect the crank angle sensor back onto the crank angle and rest it in a safe place loosely 5. Plug ecu & coil looms back into ignitor (which has been removed from engine cover), find 1 x small nut for ignitor bolt so that you can attach the std ecu ignitor earth onto the ignitor in std position 6. Place the Al sheet directly on top of the engine with longest edges running front to back, with the 9mm hole at the back on the drivers side 7. Place sideways down the 2 off 3 x coil packs on the Al sheet in simular position as if they were fitted to the engine 8. Find a 8mm nut and use 1 x 8mm Al coil mounting bolt to securely bolt the engine ignition coil loom earth to the Al sheet using the 9mm hole that you drilled (this earth normally attaches at the back on the head under the ignitor) 9. Now connect the ignition coil loom to all 6 x ignition coils 10, Install 6 x old spark plugs to ignition coil boots, and space up coils with steel or Al, so that all spark plug threads are touching Al sheet 11. Connect 1 x start jumper lead from neg battery terminal and connect to Al sheet 12. Turn ignition ON 13, Ensure you are well clear of the spark plugs, spin the crank angle sensor by hand to stimulate the ignition to operate (spinning crank angle sensor in the wrong direction will not operate the ignition, it must be spun in the alternate direction) 14, Testing the ignition system can occur by ensuring the Al coil mounting brkt is in contact with the Al sheet whilst you increase the distance of the spark plug thread from the Al sheet, this should be done in limited illumination to see the arc bridging, if, and where it is occuring A good std ignition system will ionise approx 25mm air gap between spark plug thread and the Al sheet, if the gap is increased further until the coils can not fire down onto the Al sheet, the 2 off x Al coil brkts with there 3 off x coils each will only " jump" on Al sheet with no arc bridging - Ignition System Test Complete and PASS But generally ignition misfires are caused by bridge arcing across between the top of the spark plug silicone boot connection point on coil to the ferritic iron core coil mounting plate (its on the coil with the 4 holes in it) Eg From the top of the silicon boot, across the coils body to the coils mounting frame. Once the coils that are bridge arcing have been identified, you must remove the spark plugs and the silicon boots from these coils and retest to ensure that the coil spark initiates from the coils high tension terminal and not from a crack or pin hole in the coils housing, if this is the case it is in the bin and buy a new coil, but if it is not, what you need to do now is remove all the bridge arcing coils from there mounting positions, get a sharp stanley knife and a very good light source to closely examine the coil body silicon boot connection point for carbon tracking(some form of magnification will help with this task), and use the blade to scrap away on the coil housing until all the carbon tracking marks (ie very small thin black tracks) are removed, when done (be matriculus when you make final inspection) clean all 6 x coils with electrical spray solvent, all 6 x silicon spark plug boots are to be wash with soap and a "clean engine oil gallery brush"(suitable size one of coarse and scrub the silicon boots clean ) and finish with electrical spray solvent Apply liberally the dielectric silicon grease to all the coil silicon boot connection points and to the top of all the silicon boots and connect the silicon boots back onto the 6 x coils and retest as above. The final test of approval is when you can spin the shaft on the crank angle sensor and there is "NO" arc bridging when the spark plug threads are further away from the Al sheet than the spark can jump (eg >25mm approx) and all that happens is that the coils/brkts will jump a little, you also may see a very small spark coming from the coil mounting brkt to the Al sheet, this is the residual emf when you are shunting the in this test, now you can put it all back together with your new spark plugs and enjoy. In closing THE SECRET - CLEANLINESS AND A LIBERAL AMOUNT OF GOOD HIGH TEMP DI-ELECTRIC SILICON GREASE All RB26 coils (even New one's) should use High Temp dielectric silicon grease on the coil/silicon boot connection point New Nissan OEM coils are the best Always wash, clean, liberally apply silicon grease to silicon boots when changing new spark plugs Always apply dielectric grease to the top of the plug and insulator on new plugs Ensure the ignition coil loom earth is in good condition and firmly connected and the 6 x ignition trigger ecu loom earth is connected to the ignitor Ensure all 6 x ignition coil + positives are getting battery voltage (consider dedicated ignition relay direct battery feed) Ensure main earth battery lead that goes to engine block which also connects to the car body half way along is connected and that the body earth is clean, and tight(This is a strategic point for a number of electrical problems). ALL THE ABOVE AT YOUR OWN RISK
-
So many times I read threads on SAU about additions to the OEM RB26 ignition system, yet no one has completely or conclusively understood the capabilities of the std ignition system, I have made 500kw at all 4 tyres with std ignition at 0.024". Yes I have also fitted a HKS DLI which by the way does not increase you max secondary ignition voltage, it increases the current, and the engine does run a cleaner spark plug So the question that needs to be answered is why can some Rb26 run extreme power levels and others can not with the std ignition? Simply because the ignition is breaking down, but where, so following test will identify your ignition problem. 1, Firstly you will need 6 x brand new plugs gapped to 0.6mm, 6 x sachets of high temp dielectric silicone greese (jaycar sells it) an aluminium sheet about 800 x 400 x thickness does matter, but say 1,0mm, you will need to drill a 9mm hole in the top left hand corner of the shortest side 2. Ensure ignition is OFF, Remove ignition coil loom from coils, remove coils from engine, eg 2 off x 3 coils in Al coil mounting brks, remove std ignitor from engine cover, remove old spark plugs, liberally apply dielectric silicone greese to the top and insulation of each new plug and install into engine 3. Remove 6 x injector connectors, 4. Remove crank angle sensor clip, ensure you witness mark around the washers of the 3 x crank angle bolts before you loosen and remove crank angle sensor from the motor, connect the crank angle sensor back onto the crank angle and rest it in a safe place loosely 5. Plug ecu & coil looms back into ignitor (which has been removed from engine cover), find 1 x small nut for ignitor bolt so that you can attach the std ecu ignitor earth onto the ignitor in std position 6. Place the Al sheet directly on top of the engine with longest edges running front to back, with the 9mm hole at the back on the drivers side 7. Place sideways down the 2 off 3 x coil packs on the Al sheet in simular position as if they were fitted to the engine 8. Find a 8mm nut and use 1 x 8mm Al coil mounting bolt to securely bolt the engine ignition coil loom earth to the Al sheet using the 9mm hole that you drilled (this earth normally attaches at the back on the head under the ignitor) 9. Now connect the ignition coil loom to all 6 x ignition coils 10, Install 6 x old spark plugs to ignition coil boots, and space up coils with steel or Al, so that all spark plug threads are touching Al sheet 11. Connect 1 x start jumper lead from neg battery terminal and connect to Al sheet 12. Turn ignition ON 13, Ensure you are well clear of the spark plugs, spin the crank angle sensor by hand to stimulate the ignition to operate (spinning crank angle sensor in the wrong direction will not operate the ignition, it must be spun in the alternate direction) 14, Testing the ignition system can occur by ensuring the Al coil mounting brkt is in contact with the Al sheet whilst you increase the distance of the spark plug thread from the Al sheet, this should be done in limited illumination to see the arc bridging, if, and where it is occuring A good std ignition system will ionise approx 25mm air gap between spark plug thread and the Al sheet, if the gap is increased further until the coils can not fire down onto the Al sheet, the 2 off x Al coil brkts with there 3 off x coils each will only " jump" on Al sheet with no arc bridging - Ignition System Test Complete and PASS But generally ignition misfires are caused by bridge arcing across between the top of the spark plug silicone boot connection point on coil to the ferritic iron core coil mounting plate (its on the coil with the 4 holes in it) Eg From the top of the silicon boot, across the coils body to the coils mounting frame. Once the coils that are bridge arcing have been identified, you must remove the spark plugs and the silicon boots from these coils and retest to ensure that the coil spark initiates from the coils high tension terminal and not from a crack or pin hole in the coils housing, if this is the case it is in the bin and buy a new coil, but if it is not, what you need to do now is remove all the bridge arcing coils from there mounting positions, get a sharp stanley knife and a very good light source to closely examine the coil body silicon boot connection point for carbon tracking(some form of magnification will help with this task), and use the blade to scrap away until the carbon tracking, when done clean all 6 x coils with electrical spray solvent, all 6 x silicon spark plug boots are to be wash with soap and a "clean engine oil gallery brush"(suitable size one of coarse and scrub the silicon boots clean ) and finish with electrical spray solvent Apply liberally the dielectric silicon grease to all the coil silicon boot connection points and to the top of all the silicon boots and connect the silicon boots back onto the 6 x coils and retest as above, In closing All RB26 coils (even New one's) should use High Temp dielectric silicon grease on the coil/silicon boot connection point New Nissan OEM coils are the best Always wash, clean, liberally apply silicon grease to silicon boots when changing new spark plugs Always apply dielectric grease to the top of the plug and insulator on new plugs Ensure the ignition coil loom earth is in good condition and firmly connected Ensure all 6 x ignition coil + positives are getting battery voltage (consider dedicated ignition relay direct battery feed) Ensure main earth battery lead that goes to engine block which also connects to the car body half way along is connected and that the body earth is clean, and tight. ALL THE ABOVE AT YOUR OWN RISK
-
Trust Td06 20g Turbo Kit
rockvale replied to Risking's topic in For Sale (Private Car Parts and Accessories)
Hi IS KIT STILL FOR SALE