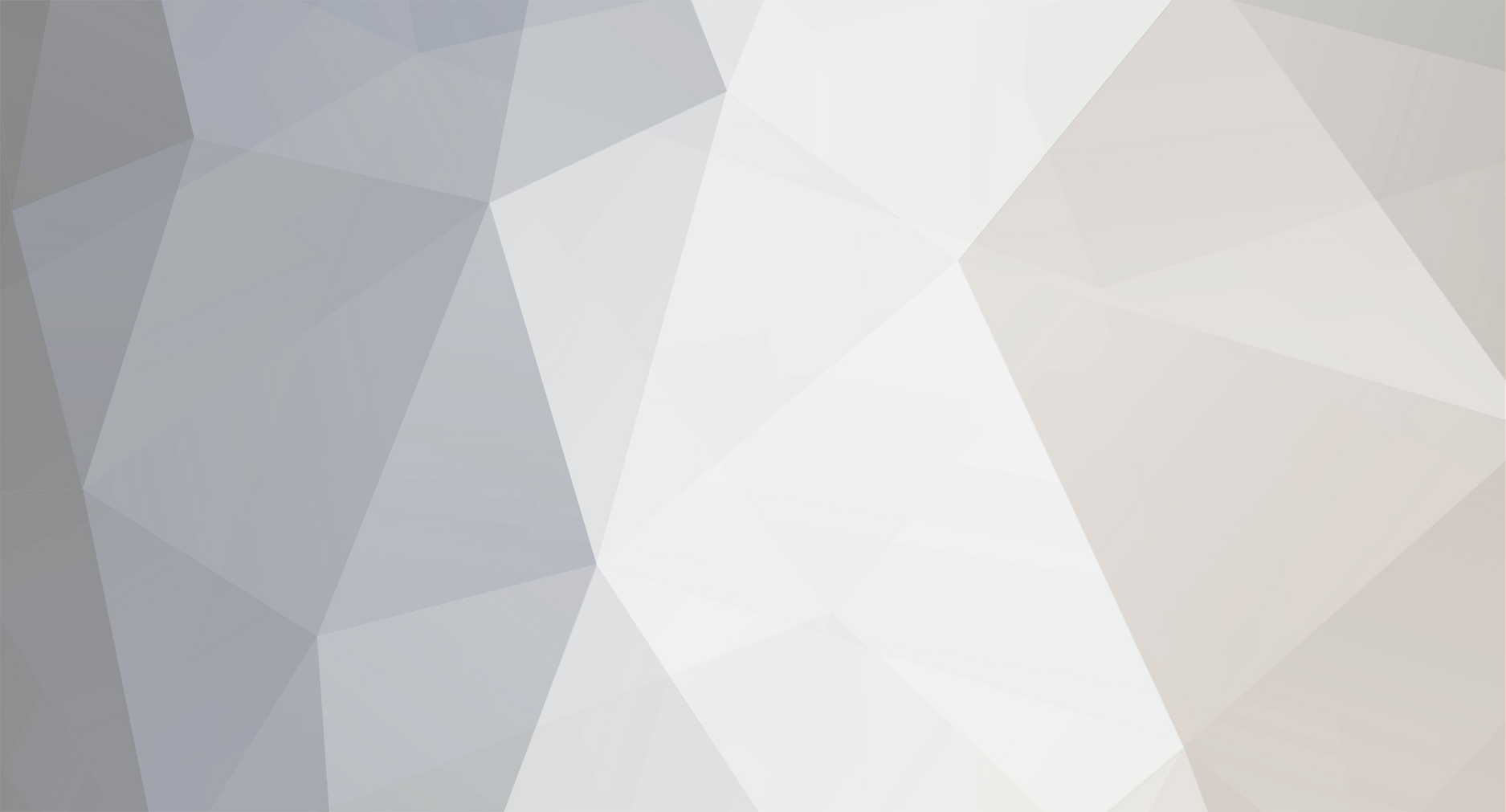
XR Pilot
Members-
Posts
49 -
Joined
-
Last visited
-
Feedback
0%
Content Type
Profiles
Forums
Events
Gallery
Media Demo
Store
Everything posted by XR Pilot
-
boost docs replacement upper radiator hose outlet
XR Pilot replied to joebresson's topic in Engines & Forced Induction
I haven't used the Boost Doc piece but I have replaced the same pipe on one of my RB25s with a similar piece I bought from Unique Auto Sports. I can't remember if I did it on car or not but you should be fine either way. Depending on how corroded yours is you may be able to get some multigrips on it, twist it around and work it loose. Failing that I'd use a cold chisel to collapse it in on itself then it should pull right out. The replacement should be a slight interference fit and tap in however in my case the fit as it was a little loose so I used some JB weld as extra assurance. That was 6 or 7 years ago, no leaks or problems since. -
If you have the boost sensor connected to the plenum and reading vacuum it will cause the issues you've described. It needs to be plumbed to the charge pipe pre-throttle so that is something to double check.
-
Disclaimer: Not a professional engine builder. You'll need to CC your parts to verify these calcs, this is assuming the stock Neo head has a 51cc chamber and you will also want to verify piston to valve clearance. Playing around with a compression ratio calculator (I've been using https://goodcalculators.com/compression-ratio-calculator/) I'd say an 8.5:1ish R33 RB25DET piston would be a good starting point. I can see two fairly easy/reasonably cheap options so far: Option 1 - ACL aka Ross aka Mahle 6MKRY9603 with 11.5cc piston dome. Set to zero deck height with a 1.3mm head gasket on a Neo head this should give a flat 10:1. If you bring the pistons 0.5mm above deck you can achieve around 10.5:1 with the same 1.3mm HG while keeping quench around 0.8mm - I've heard 0.7mm-1.2mm being a rough rule of thumb to aim for. Each 0.1mm gasket change on this combination is roughly 0.15 change in CR so you should be able to fine tune the CR easy enough. Option 2 - Wiseco K578M865AP with 14cc piston dome. At zero deck this will give 10.4:1 with 1.3mm HG. With +0.5mm deck height this will give 11:1. As before a 0.1mm change in HG thickness will change the CR approx 0.14-0.15. Hopefully this gives you a starting point.
-
Depending on the age of the firmware in the ECU you'll need to either find a tuner with either a hand controller (not many people would have one these days) or a SerialLink interface. Pop the lid off the computer and have a look at the label on the microcontroller - if it says GTS with a Q/R/S or T on the end it is laptop tuneable with PCLink using the adapter. I might still have a SerialLink in a box somewhere and could put you in touch with someone who may be willing to tune it but you'd need to be willing to travel out of Sydney.
-
Based on that would it be fair to expect that the SS-1 would give 20-30kw more than a normal ATR45 at the expense of 2-300rpm response? I'm just trying to figure out how it would compare to my other 30DET.
-
Hi Tao, I should add I have an ATR45 CBB 0.82 on an RB30DET (different car and engine) and have been happy with it so I know what to expect from an ATR45, just curious what the difference would be with the billet compressor. Power goals are 450 give or take 20-30 so I know both turbos are in that ballpark. Will be flex tuned on E85 in a Stagea and keeping VCT.
-
Are there any results for the ATR45SS on an RB? I'm tossing up between the ATR45 CBB and ATR45SS CBB. Tao what would be the expected difference in lag and power be between the two? Both external gate on a proper manifold on a 30DET.
-
FS [SYD]: RB26DETT top end 95% complete. Turbos/Manifolds/NEW Nissan gaskets/Wiring harness/Cam covers etc Hi Guys, I've got a near complete 26 top end I can't ever see myself using so I'd like to move it along. Needs a good clean and check over but it's 95% there. Comes with: - Complete head including stock cams, cam gears. NOTE: Cams have some surface rust on the ends behind the cam gears from storage, doesn't affect the cam seal surface, cosmetic only. - Complete cold side including injectors, fuel rail, balance pipe, AAC valve, ITBs, plenum, air temp sensor, TPS, factory twin turbo connecting pipe etc. All the hard to find and expensive RB26 bits are there. - Complete stock 26DETT hot side including turbos, oil lines, exhaust manifolds, dump pipes, turbo actuators and I'm fairly sure all the oil and water feeds for the turbos are there - Cam covers + front cover. NOTE: No coil pack cover included - Stock 26 coils. One coil has the plastic broken off around the plug and will need replacing - Wiring harness. Harness has had CAS plug and AFM plugs cut off before I got it however these are available new. Comes with coil pack harness, I'll need to check if ignitor is there. - Brand new Nissan RB26 genuine gasket kit. Head gasket, cam cover seals, valve stem seals, intake + exhaust gaskets etc. Worth about $400 on it's own. Whats I know is missing: - Timing cover backing plate - CAS + CAS bracket - AFMS and piping to AFMs - ECU - Coil pack cover NOTE: Turbos not pictured but are included Everything is more or less there. Use it to fix your blown up 26 or find a cheap RB30 bottom end to put under it and make ~260rwkw with the stock turbos. I can deliver within Sydney and surrounds for a fee otherwise pickup from near Sutherland Shire. Ph: 0431151016. Prefer not to separate at this stage unless someone wants to make me a decent offer for the head & cold side. If anyone wants photos of something specific let me know as I was too lazy to unwrap and re-wrap it all. $2000.
-
Normally I don't respond to stuff like this but since it's a direct attack on me I'll reply. As an FYI - this was a full 10 hour day from 8AM to 6PM without lunch breaks. As soon as one car was off the dyno the next one was loaded straight up, I didn't take a break. In addition to this I had spent about a day to a day and a half on each car prior to the dyno checking for problems (boost leaks, setting up boost control ignition timing set correctly etc) as well as doing a road tune on each car with a wideband - I had a pretty good idea of what to expect for each car when they went on the dyno and also meant that dyno time was maximized - this was a straight out tuning session, not setup or troubleshooting. Car #1 was an SR20 S15 Silvia on Nistune. The ignition map from the road tune was very close from the get go, however the car wasn't making the expected power. Dropping the exhaust with no other changes brought power straight up from 220rwkw to mid-240kw so I sent the owner home early, advised him to fix the exhaust along with a few small other problems and cut the price down accordingly. Yes, cruise mixtures were checked and adjusted.There were a couple of small problems with the tune after the fact, these were fixed with a further road tune after the dyno the following day at no charge. Car #2 was an RB25-swapped S13 running a Megasquirt 3 ecu. This had a fair bit of time spent prior to the dyno setting up the base maps. In addition they have a very good autotune so I made use of this to help correct the cruise maps inbetween power runs and while adjusting ignition timing and setting up boost control. Should I mention this car was setup for flex at the same time and we tuned both P98 and E85 maps or does that not seem possible? Both fuel, spark and boost control was setup with full ethanol blending. I also did a follow up the next morning to check cold start on E85. This tune will need more work in the future as tuning was cut short as the car has a >4psi pressure drop across the cooler and IAT's were heading past 80 degrees. Current feedback from the owner is he is very happy, cold start and driveability is much better than the ecu it replaced. Car #3 is Dan's HR and I am very familiar with the setup - their is over 80 power runs for this car logged on the dyno with various setups. I ended up spending a good 4-5 hours on the dyno the following day trying to troubleshoot problems. Yes, cruise fueling was checked. For the record, both car #1 and #3 were tuned by a 'reputable' tuner and both owners complained of very poor driveability and economy and I was asked to retune - they are much happier with the current tune. It doesn't take 3 days to setup cruise mixtures - it takes about 20-30 minutes to get it 95% of the way there and then a bit of fine tuning to get it spot on. A tuner might need a car for 3 days to setup an aftermarket ecu from scratch for a comprehensive setup (for example, individual cylinder trims, flex, cold start, modern infinitely variable VCT and electronic throttle) but this is absolutely not the norm. So yet another SAU thread that has been derailed. At the risk of putting it back on topic I'll post up some updates. - Cam timing has been checked and the exhaust cam timing was about 7 degrees off (Dan may correct me as I am working from memory). Inlet was 1 deg off. Has been fixed. - The rear housing was found to be far too small as it is a 12cm twin scroll. Back pressure was very high, a 16cm TS housing has been swapped on. Car now makes 20PSI on the road by 4K in lower gears vs past 5K on the dyno loaded up in 4th. - Internal VCT feed wasn't supplying enough oil. The 30DET has been converted to external oil feed and VCT now makes a noticeable difference - I have pulled my own 30DET down to convert to external VCT for this reason. We're aiming to get the car back on the dyno in early-mid March for a retune.
-
Hi guys, I'm on the way to Tassie so don't have time for a proper post. For the record, I was the tuner for this. This particular mainline doesn't have an rpm pickup and I didn't bother to set the rpm conversion as I had tuned 3 other cars on the same day in the dyno shed where it was ~47 degrees (yes we measured it). 100kmh on this car is 3100rpm or near enough. Between timing and fuel sweeps and dropping the exhaust this just would not make any more power. At this point I'm suspect on cam timing and would like to see it degreed back to OEM RB25 specs as a starting point and I can dial it in on the dyno from there.
-
Ah, that's what I get for skim reading on my phone. The other thing that comes to mind is the symptoms described will happen with a rich misfire - depending on spark strength it can happen at mid-high 10 AFRs. If the OP is comfortable with FC Edit I'd suggest pulling mixtures back to mid 11s and see if the misfire goes away.
-
Why does the FPR not have a vac connected? Not only do you not have a vacuum reference at idle but you've got no fuel pressure compensation under boost either. If it was tuned like that then expect to start over with the tune.
-
Max Hp/rwks For R34 Gtt Auto & Manual
XR Pilot replied to Mr Phatt34's topic in Engines & Forced Induction
Just to be clear - that was a shift kitted STOCK auto that lasted 2000km - which is why I said plan on getting a proper built auto or just get a manual car. Also it's "only" making 180rwkw on 9psi on a STOCK R33 turbo. The car was built for daily duties and I have no doubt it'd be far quicker than a 300rwkw RB25 in point-and-squirt style traffic driving. It makes over 100rwkw at a bit over 2000rpm. I haven't read back to see if it has been asked already but what are you trying to build the car for exactly? Drags, drift, circuit racing, daily driver? Not trying to be harsh but you need to figure that out before you a) spend any money and b) decide you need a 600hp auto Skyline. -
Max Hp/rwks For R34 Gtt Auto & Manual
XR Pilot replied to Mr Phatt34's topic in Engines & Forced Induction
Just so you're aware a built auto box is around the $3-4K mark just for the box and that's generally on exchange basis. For what it's worth I wouldn't bother with a stock box, either plan to build one from the outset or buy a manual car. I've got an early model RE4R01A auto box behind a 25/30 making 180rwkw but a lot of torque (lucky to be 300hp at the flywheel) with a shift kit and the box lasted 2000km before destroying the brake band. A later model RE4R01A like what comes in the R33/R34 is a little beefier with wider bands but it'd do the same thing eventually. I picked up a stronger RE4R03A and will try that with a shift kit but if it dies I'm putting the 25DET manual box in that's sitting under the bench as I can't justify sinking 4 grand into an auto box. -
Nope, it's a daily so not necessary. The water radiator is quite large though, almost the size of the radiator and is sandwiched between the air con condenser core and the radiator for stealth. I haven't got around to logging temps properly yet (there are temperature senders in the top and bottom of the radiator and I will be placing them in the intercooler outlet too) but using an infrared temperature gun shows the IC outlet temps stay close to ambient on the dyno. Throttle response is instant in every sense of the word as expected from a stock 21U turbo on a 30DET with an automatic gearbox. It'll be getting one of your highflows hopefully later in the year once a few other mods get done, most likely OP6 based.
-
Sounds like your ecu is in limp mode. It can be caused by a corrupt image in the Nistune board, poor installation or most likely in your case (if it was working ok previously) the Nistune board has come loose from the socket. Make sure it's pushed in properly. Symptoms of limp mode are you can make changes in the software but it doesn't really do anything and a massively over rich idle.
-
If memory serves the dash cluster uses pull ups connected to a 10V supply (as if they used battery voltage the gauge readings would fluctuate with charging voltage). To make this work you need to build a voltage divider to your MCU with the oil pressure sender wire tapped in and forming the voltage supply to your divider. Check the workshop manual for resistance at low and high pressure (or better yet, use an air compressor and regulator on the factory sender and check with a multimeter; they are 20 years old after all). Connect your voltage divider up to the sender, key on and bridge the sender with resistors based on the workshop specs. Measure output of the divider, swap resistor, remeasure. That's your calibration voltages for low and high pressure then map those voltages against the pressure tested and you've now got your sender calibrated. If that doesn't make sense let me know if you want a diagram.
-
Interesting To Say The Least Dyno Result Rb30det Hx35
XR Pilot replied to menthol369's topic in Engines & Forced Induction
Unfortunately I left my thermocouples at home on the day but I can lend them to Dan to check discharge temperature later. Lack of compressor flow is a possibility but personally I'm leaning to a small turbine housing causing a restriction. From what I know of the HX35s the compressor supposedly flows around the 55lb/min mark; you'd think that'd be enough flow for at least somewhere around the 300rwkw ball park. -
Interesting To Say The Least Dyno Result Rb30det Hx35
XR Pilot replied to menthol369's topic in Engines & Forced Induction
Figure I'll fill in some more information here as I'm the one that tuned it. Timing/fuel/dwell has all been checked, no problems there (Though to be honest I haven't checked timing scatter with a light but I doubt it is a problem here - engine responds to timing how it should) and ignition timing is about what you'd expect - it's not overly sensitive to timing as a lowish comp motor on low boost as you'd expect. Timing sweep under load shows minimal change. AFRs are on another sheet but are sane around the mid-11s, low 12s mark. Pressure drop across the cooler was minimal. We tried dropping the exhaust from the dump back and made around 4-5rwkw more. Basically aside from not being able to get the thing to hold boost (even with full boost pressure applied to top port of gate it made 12-13psi peak up top) it behaves as you'd expect. I have asked Dan to put a pressure tap into the collector on the manifold to check back pressure when he gets time. Cam timing may not be spot on - it's aligned to the backing plate marks - yes, it's not going to be spot on being a 3L block - but I can't see how that'd cause a problem with it not holding boost, just shave a bit off the top end power figure if it is a bit out. VCT is connected and works as expected, changeover sweet spot is around 5K. Finally, before anyone asks the RPM scale is incorrect and I kept forgetting to tell Dan. The end of the run is just off the rev limiter at 6800. I kept forgetting to reset the derived RPM scaling as I had other things to worry about. -
Your R33 ECU has been 'chipped' - you'll notice the chip labelled H8/534 is in a socket while the other is not, a dead giveaway that it's non standard. The factory ecu also has a foil sticker with the MEC code of the program eg MEC-R503A on the CPU - I've got half a dozen R33 ecu's in a pile here including one that has been socketed to compare to. There is only a few companies that can do it as you need to firstly fit the 54 pin socket and secondly the 'chip' on an R33 is actually the processor - the memory and CPU on an R33 ecu is one and the same. The CPUs aren't cheap to buy (last I checked are no longer available) and you can only burn the program once so you want to make sure you get it right. As far as figuring out what your ecu has been set up for the only way to do it would be to connect it up and download the ROM image through the consult port with NissanDataScan or Nistune (provided the tuner hasn't locked the rom download function) and compare the maps to stock R33.
-
Valve Body Upgrade - Auto R33
XR Pilot replied to hardsteppa's topic in Suspension, braking, tyres and drivetrain
There is a set of interlock valves to stop the overrun clutch engaging in 4th gear. In my experience if you have too much line pressure then the overrun clutch will either float on and off or not engage at all due to this. This may or may not be your problem but it's where I'd start - I have the same shift kit fitted to my box (sans components that require box removal & disassembly) and overrun works fine but I have an aftermarket TCU. When locked in 3rd on the dyno it takes have a half second or so for the overrun clutch to re-engage after a pull as the line pressure bleeds away. -
My Uno clone arrived yesterday so I figured I'd bench test this on the Uno for completeness. Due to a misunderstanding on my part as to how Uno interrupt pins are mapped you'll need to change the pinRPM definition in the posted code to either 0 or 1 to use pin 2 or 3 for input respectively. You may also want to change the signed rpm integer variable to unsigned (unsigned int RPM) as that will allow up to a theoretical 65,535 rpm vs 32,767 rpm. Aside from that the code works as intended; bench tested to 60,000rpm on a square wave input (with minPulse adjusted appropriately) with the Uno at 16Mhz. At 9,000rpm using a 1% duty cycle signal I get a jitter of 20rpm which I'd say is down to my basic test rig. Should suffice methinks EDIT: I forgot to mention that the previous tests were on a running RB30 - which is why I didn't rev it too hard
-
Finally got around to testing this. Note that I tested on an MCU that's much faster than an Arduino (still waiting on my Uno - I'll test on it once it turns up) but the attached code should compile ok. When run it'll send the current RPM via the serial port at 4Hz but you can update as fast or slow as you want. The code should be fairly self explanatory but obviously you wouldn't use delay in a real program but it'll show the concept. It also has some basic noise rejection in place where pulses shorter than the specified minPulse value are ignored, it's surprisingly effective. Here's a pic showing the output from the code. Worth mentioning there is a bit more to my test hardware than just a straight connection to the MCU so your mileage may vary. #define pinRPM 3 // Define the tacho input pin #define minPulse 2000 // Reject any pulses shorter than this value in uS. 2000uS = 10,000rpm on a 6 cylinder #define noPulses 3 // Number of tacho pulses per engine revolution. 3PPR for a six-cylinder 4 stroke. volatile unsigned long rpmTime = 0; // Length of time in microseconds between interrupts volatile unsigned long rpmLastTime = 0; // Value of micros at previous interrupt int RPM = 0; void setup() { pinMode(pinRPM, INPUT); // Set pinRPM as an input attachInterrupt(pinRPM, rpm_count, RISING); // Enable ISR rpm_count on pinRPM on a rising edge Serial.begin(115000); } void loop() { noInterrupts(); // Disable interrupts whilst doing calcs if (micros() - rpmLastTime > 500000L){RPM = 0;} // If it has been more than half a second between interrupts then assume engine has stopped else { RPM = 60000000L / rpmTime / noPulses; } Serial.print("Current RPM: "); Serial.println(RPM); interrupts(); delay(250); } void rpm_count(){ if ((micros() - rpmLastTime) < minPulse) {return;} // If the time between interrupts is less than the minimum pulse time then reject it as noise and return rpmTime = micros() - rpmLastTime; rpmLastTime = micros(); }