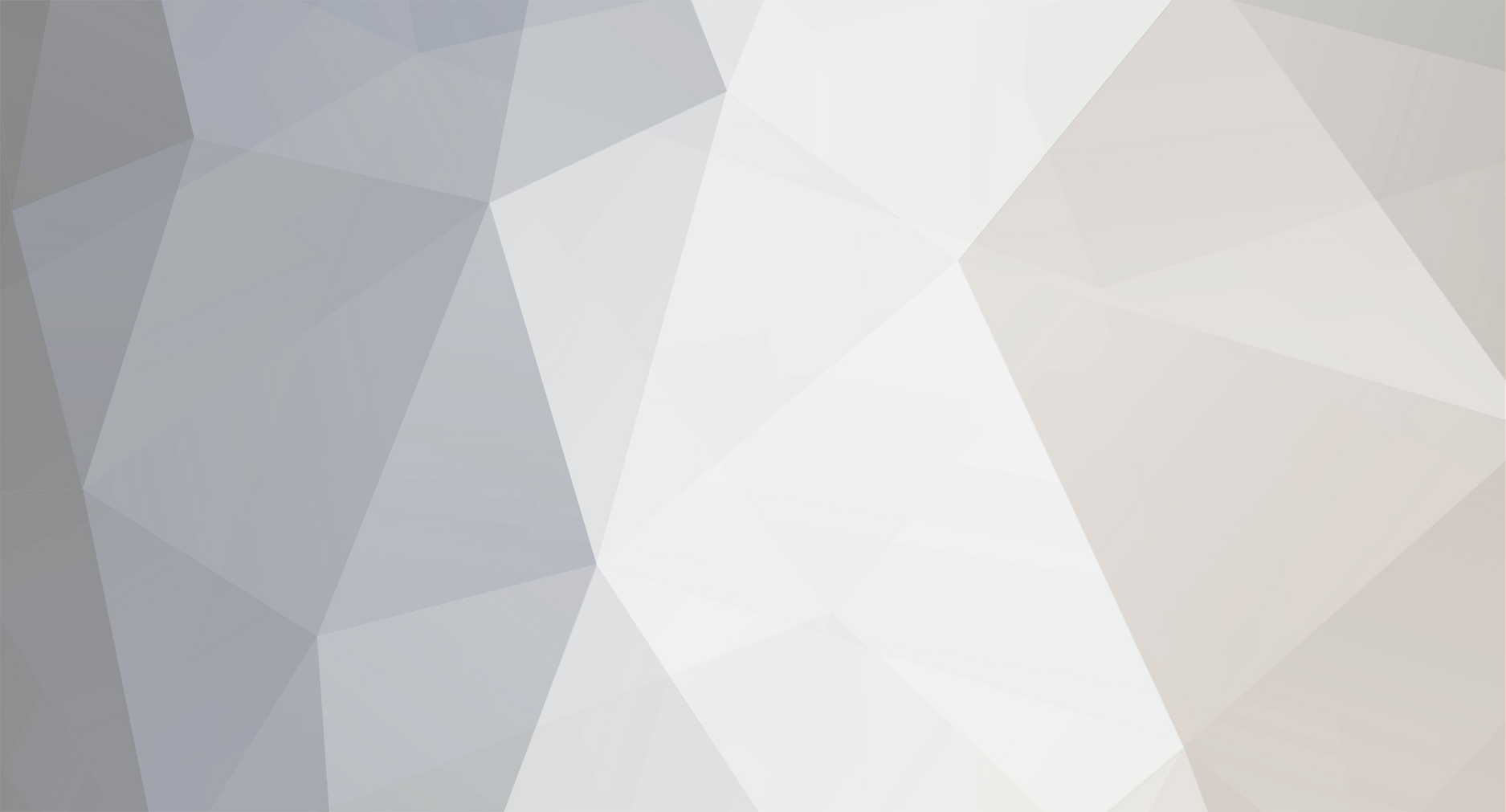
GTSBoy
Admin-
Posts
18,278 -
Joined
-
Days Won
277 -
Feedback
100%
Content Type
Profiles
Forums
Events
Gallery
Media Demo
Store
Everything posted by GTSBoy
-
What you should do is go set up your existing turbo on matchbot and tweak the engine parameters until it pretty much matches what you get at the two datapoints in your OP. Then you can throw other turbos at it and see what happens.
-
That's for convenience of assembly of something which can suck balls to do if you've got to juggle all the parts in a location with poor accessibility.
-
Leaking clutch slave cylinder?
GTSBoy replied to Meap's topic in Suspension, braking, tyres and drivetrain
With the caveat that brake fluid leaking into the booster can damage the diaphragm. So when taking it off and cleaning it on the outside, do your best to work out what the situation is inside, and deal with any fluid in there appropriately. -
That sort of ballpark, yes. Nah. The blue map on there would do 85 pounds and 2.8PR at about 69%. That would give you the same output on your engine, but with that much cooler charge from he better efficiency. The 62% line at 2.8 PR would do about 97 lb/min. But you're not going to be able to operate at that point, because at 2.8 PR, your engine & turbine only want to flow what they're flowing now. So that ~85 lb/min number. What you know is that the engine and turbine would remain the same. So the boost required to make more power must increase. Same resistance. So you can't be looking at the 2.8 PR area. You have to do an in-skull dyno/flow bench to scale up from your existing performance. So, PR say 3.2 might push you up to around 95 lb/min. That would land you on about 67% efficiency. Not bad. It'll be somewhere near there. No promises though....I did that in my head, and it's got all sorts of likely error! Note, a big difference (beyond the simple size difference) between the 91 and 92mm comp wheels is massive increase in inducer area. That pushes the choke line way over to the right, because it slows down the inlet flow.
-
Nah. Air to power is the same pretty much independently of how well the engine flows. The only way that the air to power ratio changes is if you change the stoichiometry. Richer or leaner means that you have a different amount of air for the amount of fuel you're putting in. At any given load & speed the air flow is approx the same (for the same engine), but if it is pig rich then it won't make as much power as if you lean it out a little. So, starting from rich, if you take some fuel out you make more power, but the amount of air remains the same. So the air to power ratio changes. As you approach stoich you sort of go towards a peak of how much power you can make from that qty of air, then as you go over stoich to the lean side, you start making less power again.** ** All of that presumes that you do not melt or detonate the engine to death first, which is what will actually happen in a turbo RB. But in an engine that is a looooong way from the detonation threshold (say, NA, 6:1 compression ratio) then the above paragraph is all true. More boost = more flow = keeping on going up that compressor map towards the top right. You will stay on the RH edge of the map regardless. The only way to push yourself back towards the centre of the map is to introduce a big restriction somewhere. So, I tend to agree with Lith. Turbo is maxxed out. Needs a bigger turbo, or at least one that is better optimised for more flow and less PR.
-
I suggest the biggest Century battery that fits in the space. I can't remember exactly which one I put in there. I think it's the 430CCA one. I find Century more trustworthy than most other options available in Australia. I also suggest that you either leave a solar panel charger on it, or a good float charger, if it is really left idle most of the time.
-
No, what he meant was.....the EGOT lamp is also the check engine light, so it will indicate either that the cat is too hot, or that the ECU is chucking a code. You need to check whether or not the ECU is chucking a code at you. That's what he meant by "verify that there are no active codes". What he really should have said was "check to see if there are any codes". So, check to see what your ECU is telling you. It is far far more likely that you have an ECU/sensor problem than that you actually have overtemperature exhaust**. **Although I am willing to concede that a thoroughly blocked injector, or similar problem, could cause sufficiently lean conditions to make hot gas. Usually though, there are other more horrible symptoms of such a problem than just the cat light coming on.
-
Yeah, it's not so much that you're near the choke line specifically, in that, it's not that likely that you're actually choking the turbo. It is possible that you're choked, given the possible range of errors in your placement of your operating point on the map (ie, estimated crank power from wheel power, estimated relationship between air flow and power). What happens when you choke a turbo is that you reach the local sonic velocity in the compressor inlet and hit the wall in terms of how much air you can get through it. In order to get more air through the inlet, you start to pull a vacuum right in front of the compressor wheel and that "stretches" the air that you're trying to compress. That effectively lowers your starting pressure for calculating the pressure ratio. You're not starting with atmospheric air - you're staring with a lower pressure than that. And that hurts production, driving the mass flow down and the PR up. There may actually be some more horrible effects of choke resulting from shock waves and resonances in between the compressor blades, so it is wise to stay away from choke conditions. But there's not a lot of evidence to show that it's particularly bad for the turbo and to stay away from choke just for that reason. The fact that the turbo is tapped out and not giving what you need from it is the main reason to stay away from choke. What is actually the biggest killer, and would directly point to the IAT problem, is that being right over on the edge of the map places you a long way from the efficiency island. Instead of operating the compressor at the highest efficiency available (over 75%) you're way down at <65%. Could be as low as 60%, depending on the above mentioned errors in the location of the operating point. And that loss of efficiency turns up directly as temperature. A useful question to answer is, where is the operating point for your lower boost result? I had a quick look, and sadly it appears to be on the same (64%) efficiency line. So that probably (possibly?) rules out the boost increase driving the OP off to the right. That would suggest the IC is heat soaking. But it's a big Hypertune unit, so......hard to imagine. Perhaps though, you should consider sticking some fine thermocouple tips onto the core tubes at each end of the core, to see how hot the core itself is getting. You'd best benefit from (temporary) IAT measurements in the hot and cold pipes also. Or at least adding the upstream measurement, seeing as you already have IAT in the plenum. Got to see how hot the air is getting as it exits the turbo, and what it is doing to the IC core. If the air T isn't much worse out of the turbo (on the high boost, cf the low boost) but the core is getting hot, then you could conclude that the turbo efficiency isn't changing, and the IC is no good. If the turbo outlet temperature is going through the roof, then you would conclude that you are actually suffering an efficiency change.
-
20 Neo had VCT. I don't have the full R34 wiring diagram here with me (thousands of km from home) to have a look at the wire colours, and I don't even know if the 25DE diagram is in my collection anyway. So I can't check for sure, as to whether the loom is most likely to be one or the other. I'd suspect that it is a 25DE. But just can't be sure.
-
Well, assuming that the empty spot next to the red one is in fact position 47, then yes, the wire is missing. But, the next position along, 64, I think, should be vacant in the DET loom, and....it has a wire in it. That perhaps indicates that it's a 20 or 25DE loom.
-
My R33 GTST Bare Shell Build Up
GTSBoy replied to PerthR33GTST's topic in Members Cars, Project Overhauls & Restorations
It's a perennial (millennial?) problem. -
AC compressor tech questions
GTSBoy replied to Murray_Calavera's topic in R Series (R30, R31, R32, R33, R34)
And they only draw 1 to 2 digits of Amps. AC compressors would draw 3 digits (at 12V). -
AC compressor tech questions
GTSBoy replied to Murray_Calavera's topic in R Series (R30, R31, R32, R33, R34)
I've had this type of conversation lately with a couple of peeps on here. The electric compressor is a good idea to prevent the on-off clutch problem from the compressor potentially cycling while at high revs. Granted, in the usage model of charge cooling, it would likely be stuck in the ON condition. But in the OP's usage case, it could quite likely cycle on-off when just working as an AC, even though he might be pooping out 7k rpm at the time. So, yes to elec comp on that basis. But perhaps the better aspect of an elec comp is that you really need a 42V battery there for the alternator to run against. Now, ignoring the weight penalty of having to have another 18 cells of lead acid battery on board (in addition to the native 12V battery) (or potentially something like a lithium battery) you could then actually not even load the alternator while trying to extract max power from the engine. You'd use a clever charge controller between the 42V alt and the 42V battery that would allow charging on overrun and partial throttle, but reduce alternator current draw when above X% throttle opening, or some more sophisticated arrangement, if desired. Then you can still get the comp to run to produce the cools when you need it to cool your weary body (or the air charge) by leaning on the battery for part of the lap. And so on, and so forth. There's a dozen things that you could come up with like that if you really wanted it. -
My R33 GTST Bare Shell Build Up
GTSBoy replied to PerthR33GTST's topic in Members Cars, Project Overhauls & Restorations
A hood is a thuggish brute with poor manners, BO and a criminal record. That's a bonnet. -
AC compressor tech questions
GTSBoy replied to Murray_Calavera's topic in R Series (R30, R31, R32, R33, R34)
And....no. You're not going to draw 3ish kW of power from a 12V supply. BEVs and hybrids that use electric AC compressors are running them on the 42V standard that sort became the thing when such high power demand applications started to become a thing, or even higher voltages. This because..... they have higher voltage available. You wanna rig up a special alternator capable of putting out 42V, then yeah, maybe. -
AC compressor tech questions
GTSBoy replied to Murray_Calavera's topic in R Series (R30, R31, R32, R33, R34)
The other thing to keep in mind is that it is not at all good to ask the clutch to pull in at high rpm. If you do not prevent it pulling in up high, then it will, and the clutch will cop a hammering. -
R33 s1.5 missing at 5,000rpm onwards.
GTSBoy replied to Killer33gtst's topic in R Series (R30, R31, R32, R33, R34)
The information comes in dribs and drabs. What about the spark plugs? Had them out? Changed them? Particularly #6. -
They're probably all using aftermarket ECUs.
-
A state of quantum superposition, like Schrodinger's Cat. Both alive and dead - we just haven't found out which, yet.
-
Or just some carpet without the MDF. If nice flat sections are required, corflute is a lighter alternative.
-
viscous diff replacement for R33 gtst
GTSBoy replied to Dasmbo's topic in R Series (R30, R31, R32, R33, R34)
No....the open diffs also have equal length shafts. I would presume that an LSD upgrade (ie, Quaife) would be primarily aimed at the open diff market, not replacing an already helical diff. I have no idea whether the open diff equal length shafts are the same as in the S15 helical diff or not. They might be. I really should go to the effort to find out one day. The Just Jap listing for the Quaife diff lists it being good for all the S & R chassis diffs (and older long nose diffs too). With the only stipulation being the 29 splines. But of course, we all know that there's a bunch of different spline lengths across all that, hence my concern. -
viscous diff replacement for R33 gtst
GTSBoy replied to Dasmbo's topic in R Series (R30, R31, R32, R33, R34)
I was skeptical. I haven't looked for a while. But they're now listing the QDF7L for all the R200 chassis cars. All S and R. Just has to be 29 spline stubs. But.... the thing that bothers me about that (apart from the slightly eye watering price) is that the imply you can use it on any such car....but clearly there are different stub axle lengths for the open diffs, VLSDs, and factory helicals. Surely the Quaife can't accept all those axle lengths and you have to either use the equal length stubs or the VLSD unequal length stubs, or maybe even the Nismo equal length stubs. Would require clarification before jumping on board. -
viscous diff replacement for R33 gtst
GTSBoy replied to Dasmbo's topic in R Series (R30, R31, R32, R33, R34)
It's the same with 3 out of 4 such things Nissan did. HICAS? A bold idea, hampered by insufficient sensors, processing power, and experience with the required algorithm design. Result? Good up to 7-8 tenths, then a f**king nightmare to drive around. A-LSD? Ditto. Ceramic turbos? Yup. Bold idea. Perfectly valid for usage "as intended as a street car without any modification". No bloody good in practice in the real world. Turn up the boost and say bye bye (to the wheel, not the guy you were racing). Only ATESSA came close to being a good first effort and result. Still not perfect, but not really bad in any way.