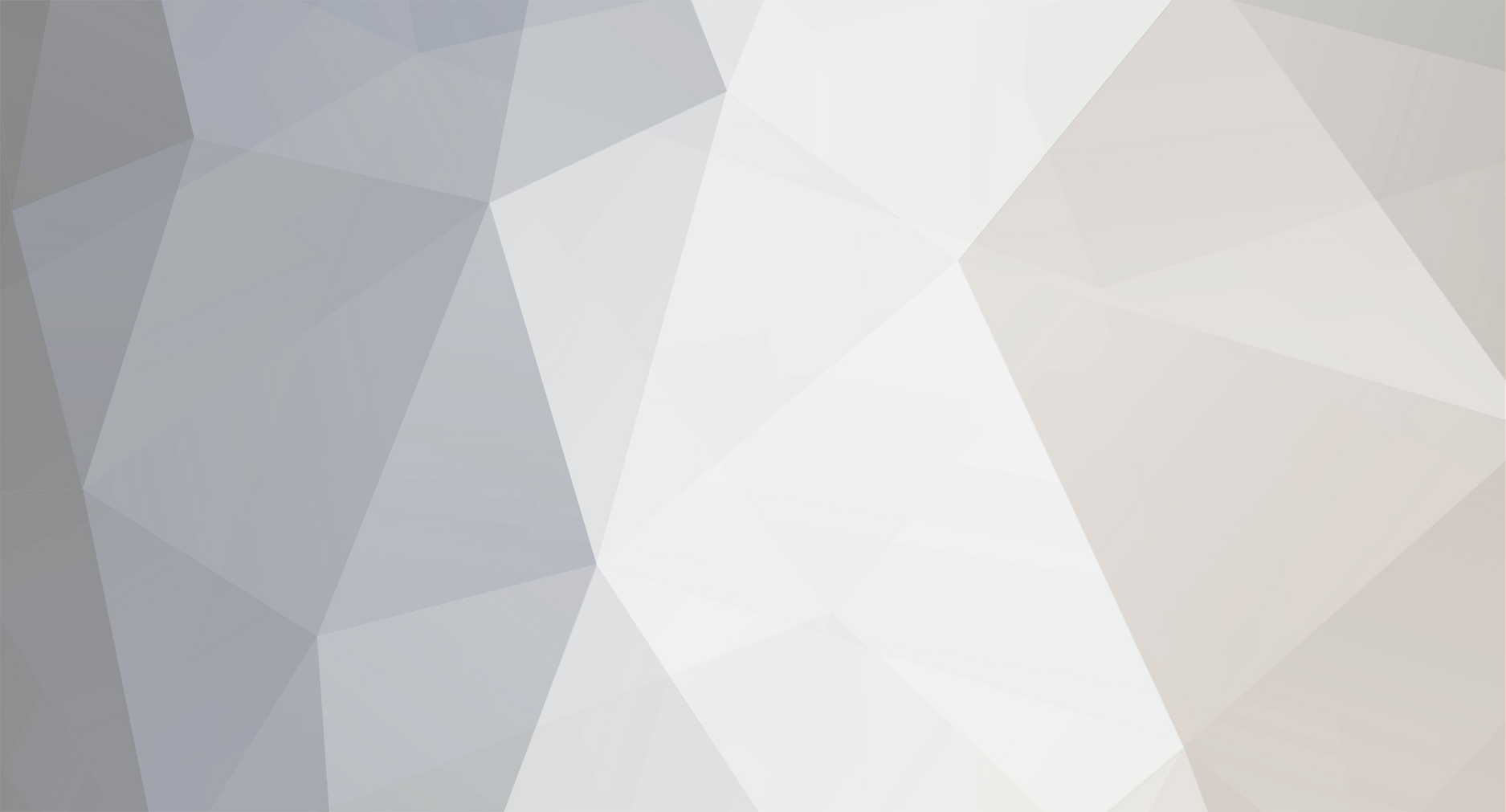
GTSBoy
Admin-
Posts
18,279 -
Joined
-
Days Won
277 -
Feedback
100%
Content Type
Profiles
Forums
Events
Gallery
Media Demo
Store
Everything posted by GTSBoy
-
Twins vs single vs 2 x singles lol
GTSBoy replied to Old man 32 GTR's topic in Engines & Forced Induction
I still say that a supercharger + turbo is the answer to all this bullshit. Put 500HP worth of screw compressor on board and have it hand over responsibility to the 1000HP worth of turbo(s) at some point where the turbo(s) can and will make all the boost you need, without needing to worry about their boost threshold, etc etc, wah wah. Torque multiplier from idle on up from the blower = more gas to the turbine anyway. You get to use an open housing for reduced EMAP at full noise. Win win win win win. And that's just as a sequential setup. Extra brownie points for doing it in series. Low blower pressure ratio multiplied by low turbo pressure ratio = high pressure ratio with none of the stress that typically results from trying to get it all from one place. -
Two boofheads or one derp.
-
Constant power to injectors Rb20det
GTSBoy replied to wdk32's topic in R Series (R30, R31, R32, R33, R34)
Allright, I'll answer my own question. -
Constant power to injectors Rb20det
GTSBoy replied to wdk32's topic in R Series (R30, R31, R32, R33, R34)
What does the wiring diagram say? -
Twins vs single vs 2 x singles lol
GTSBoy replied to Old man 32 GTR's topic in Engines & Forced Induction
Stupid big twins = NOS to get it up, right? -
Vibration when power Send to the Front
GTSBoy replied to JoKeR33GTR's topic in R Series (R30, R31, R32, R33, R34)
Don't know if there's anything to see. Seeing as those photos will be on a memory card.....why not upload them direct to the thread? -
FWIW - I did type "r e t a r d"
-
I think this, because (actually, not because of this) because that's not true. He's adjusting the cam gear, not the crank gear. But also I disagree with Ben, because This is not true. The CAS is driven off the centre of the end of the camshaft. Therefore the CAS is in time with the camshaft. The gear remains in fixed relationship with the crank, but the adjustable bit of the gear moves the cam foreward/backward wrt the gear, and the CAS goes with it. So, advance or boofhead the cam by 2° and you have to boofhead or advance the CAS to compensate. Whatever the case, you don't just twist it back..... you do use a timing light to get it set right, in which I do agree with Ben. There. I hope I haven't ruffled too many feathers.
-
Crank angle sensor question? R33 gtst s2
GTSBoy replied to Almera96gtin15's topic in R Series (R30, R31, R32, R33, R34)
this -
If that's where your speed signal is coming from, then yes, it could be. But, given that I can't see how the speed signal would be coming from the wheel sensors, it would seem unlikely.
-
Crank angle sensor question? R33 gtst s2
GTSBoy replied to Almera96gtin15's topic in R Series (R30, R31, R32, R33, R34)
Yeah, it's not supposed to spin. Spinning would be the bad thing happening, not the occasional stopping of spinning. Care to post a video so we can all do the WTF!? together? -
That's how the aftermarket solid ones are held on.
-
Borg Warner S360SX vs S362SX-E testing on a drunk RB30DET
GTSBoy replied to Lithium's topic in Engines & Forced Induction
The key difference here is that the smaller engine will require a higher pressure ratio (more boost) to flow the same amount of air through the engine - hence Lithium's point about there possibly being a need for a different size turbo if that higher boost would put you up against the surge line or way off the efficiency island cf the larger engine. -
Was probably just Sikaflexed on there.
-
O-ring or gasket for Oil Strainer?
GTSBoy replied to Neostead2000's topic in R Series (R30, R31, R32, R33, R34)
Seems fine. You never have 2 grooves facing each other. -
No voltage to red/blue wire r33 gts25t
GTSBoy replied to G2trop's topic in R Series (R30, R31, R32, R33, R34)
Good work. -
No voltage to red/blue wire r33 gts25t
GTSBoy replied to G2trop's topic in R Series (R30, R31, R32, R33, R34)
Get the wiring diagram. Find the source of the power, go there and probe. Then move forward in the diagram until you don't find power any more. -
O-ring or gasket for Oil Strainer?
GTSBoy replied to Neostead2000's topic in R Series (R30, R31, R32, R33, R34)
If the block mating surface will work with an o-ring, then use the o-ring that suits the pickup. If you were going to fill the groove to use the gasket, then the best bet would be some epoxy putty. Not bloody silicone! Remember to use a suitable o-ring material for hot oily conditions. Not just some random hardware shop o-ring. -
Where are all the 370GT Coupes Hiding?
GTSBoy replied to Vee37's topic in V Series (V35, V36, V37 & Infiniti)
They're starting to succumb to random unfixable electrical gremlins. -
High RPM RB's - Share Your Story
GTSBoy replied to Chopstick Tuner's topic in Engines & Forced Induction
8K is a walk in the park for a stock RB20. I simply raised the rev limit on mine (Nistune) to 8300 and ran it hard for years. Stock turbo though. 9k is not hard. Just need springs, and maybe consider the lifters as a potential weak point. Making strong power up there is, of course, a matter of cams and porting and so on, as I said before. Doing all of this, on a forged motor, and not planning to run 22+psi is a waste of time. You need boost and you need lots of it to make power on an RB20. With E85 you should probably be considering 30+ psi. An RB20 is not a good motor for the street. By the time you have them up into the 250rwkW region, you have lag, lag, lag, lag, nothing, then more nothing, then.......wheelspin. As a track engine, kept right up on the boil, more acceptable. For street use, I would seriously not be looking too exceed 200rwkW on a 20, to try to keep it more useful. But even that still matches the description in the paragraph above. I went RB25 and the thing actually accelerates before boost arrives, simply from that tiny bit of extra capacity. A 3L would be even better. If I was stuck with an RB20, I would twin charge it. Screw compressor blowing through a turbo. Make it act like a 3L, then rev like a 2L. I think I might have said this before. -
I bet they wear gloves too.
-
Sounds like clutch.
-
R32 Sedan Front and Rear Window Seals
GTSBoy replied to 2000c43's topic in R Series (R30, R31, R32, R33, R34)
Front might be the same, but there's no way the rears are. Rear screen is a different thing on the sedan, fo' sho'.