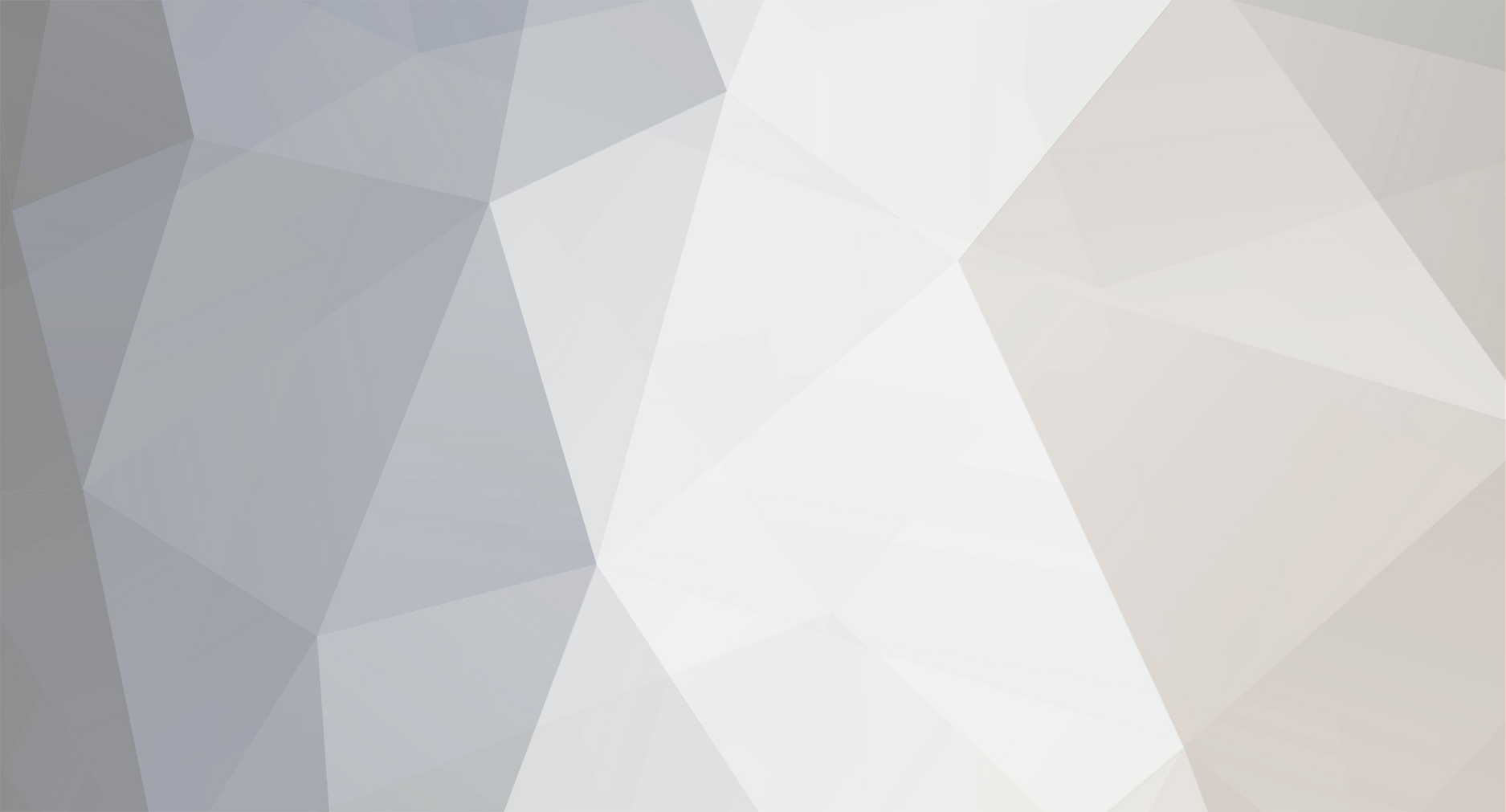
GTSBoy
Admin-
Posts
18,299 -
Joined
-
Days Won
279 -
Feedback
100%
Content Type
Profiles
Forums
Events
Gallery
Media Demo
Store
Everything posted by GTSBoy
-
I f**ked up - cut power cable running to battery too short
GTSBoy replied to IM-32-FK's topic in General Maintenance
You've just been in there working on it. How come you have no idea what it looks like? -
How about....the TCU not being interested in running the wrong trans?
-
I f**ked up - cut power cable running to battery too short
GTSBoy replied to IM-32-FK's topic in General Maintenance
FFS! It's just wire. -
No-one with a VQ would f**k about with anything other than OEM VQ37 type coils (same as R35 GTR basically). Surely?
-
It's not "like" it at all. It is exactly it. There is a minimum velocity** below which the sensor's accuracy goes to shit. That's the catch 22 in these things. A 500HP engine (that makes 500 HP because of boost) only uses almost exactly the same amount of air at idle as its 200HP unboosted original version does. But you need the AFM to be big enough to measure the 500HP worth of air. It sucks really, because these AFMs are really only measuring velocity**. The "flow" simply comes from multiplying the measured velocity by the cross-sectional area of the tube that it is in. Bigger tube means the same velocity = more flow. **Have to be real careful here. They kind of actually measure the "mass velocity" of the air going past the sensing element. The mass of air flowing past steals heat from the wire and the current used to keep the wire at the right temperature is the indicator of that mass flow rate. The mass flow rate is not really at a single point, it is actually obviously in the very small cross-sectional area around the sensing element. But that little cross sectional area is always the same, regardless of how big the rest of the tube the AFM is installed into is. So you can sort of allow the "mass velocity" to condense to "velocity" in your mind when thinking about it. But....that's also only really true when the air is at a reasonably constant density, like it is out the front of the turbo. If you put it after the turbo (cooler), then the density of the air can be way more than double (because of boost), so for the same "mass velocity" you can actually have a much much lower real velocity. Still stealing the same amount of heat from the sensing element. You could go crazy trying to juggle these parameters in your head when working out whether a given sensor will work better in one spot or another. Superficially, at least, I think we really need turbo inlets to be too large for the AFMs to work so that the pressure losses are absolutely minimised. That's because vacuum in front of a turbo is totally parasitic to turbo capacity. Need them to be big for the turbo, but that's too big for the AFM. Post turbo, we only need the pipes to be large enough to minimise pressure drop from friction, which is a whole different relationship and you're willing to give away a tiny bot more there than you are pre-turbo. So it ends up doing exactly what Dose said - you can get both good full scale capacity and good resolution when you put the AFM car post cooler. Less compromise in one or the other than pre-turbo.
-
Sadly, while these AFMs might (they do) measure the air temp of the air going through them (they have to in order to even work), but they do not report it anywhere. It's only used internally to work out what the current used to heat the wire to target temperature actually means in terms of mass flow. So long as the air temperature does not exceed the capabilities of the temp sensor, etc, as I said in the above post, it will still work post turbo in hot air. But I'd be willing to bet that many such installations are far exceeding what the AFM should be exposed to and are probably actually quite dangerous in terms of tuning, because if things like air temp are being clipped at the max value, the AFM is not measuring properly. That's just like running an AFM up off the top of the 0-5V scale and "tuning" be simply adding more fuel at the top of the table. There's no actual flow measurement. That voltage could be any flow out of a range of possible flows once you go off the top. Same with clipping the max temperature, etc. I must stress though that I don't know what the max temp these things are able to work in is. A normal RTD is good for ~450°C, but if you don't need to go that high you would not ever calibrate its electronics to read that high. You'd use your available resolution more wisely. I'd expect the automotive guys to do that too, but it's a question of what max they'd choose. For their intended application, you'd not need any more than ~100°C, because you'd never expect the ambient air or even engine bay air to be that hot. They might use that, or they might use 150°C. I dunno. But in the absence of knowledge, a little more caution is better than just blindly charging ahead. So I'd be cautious. Carrying on from the discussion of where to put the AFM, as I said above, the best place would be before the turbo, but once things start becoming a little more extreme (like big 4" diameter turbo inlets, lack of room for a nice pipe to place the AFM in, etc) people get cornered into having to consider moving it post turbo. In that case, as I said in previous post and for the reasons of caution I said here, post cooler is the smart place.
-
I hate to shoot down your own faux science there, but let me assure you that there is no "laminar flow" in any such environment (automotive intake tract flow). The definition of laminar flow is the regime where the Reynolds Number is below 2000. With very low density and low viscosity fluids (ie, air) this is almost impossible to have unless the diameter is absolutely tiny, or the velocity is very very low. The Re will be many tens of thousands in any typical automotive intake tract, which is very very far into the turbulent flow regime (which starts at around Re=4000). It is turbulent. It is fully turbulent. There is no way to argue that it is not turbulent. What you are actually trying to describe is called "well developed flow". The Re is still way too high for the flow to be laminar, it is indeed fully turbulent. But, as you allude to, immediately after a bend or other flow disturbance you have flow which is disturbed in some way. Biased to the outside of a bend, full of swirl or tumble from some flow disturbance like a side port. But after some distance of totally straight pipe, these disturbances will settle out as the energy in the flow is redistributed through internal friction and inertial effects, the flow will resume a nice "fully developed" velocity profile. Which, in turbulent flow is a velocity profile that is fairly flat across most of the duct tapering off to zero only close to the walls. The velocity profile looks more like a cut off bullet, rather than the actual 22 bullet shaped velocity profile you see in true laminar flow. But here's the stinger. It takes at least 10 diameters of straight pipe for flow to start looking well developed. It really takes at least 20 diameters for it to be getting close to well developed. And aerodynamicists and other engineers working in this area would not consider anything less than about 40 diameters of straight pipe if they wanted an undisturbed flow profile to do work with. (There are ways to cheat this with flow straighteners of various sorts, but we will ignore these as they are not really that practical for automotive applications). The upshot? There's really not any length of straight pipe in the inlet tract of almost any car's engine that would get you anywhere near close to well developed. You'd be lucky to get 5 straight diameters. (You should place any typical flow meter at least 10D downstream from a disturbance and ideally at least 5D upstream from the next disturbance. If you can't get that many Ds either side, you're best bet is to divide the space in the same ratio, sorta 67/33 %ish, unless you are really short of diameters, then you lean towards biasing the available length to the upstream side, and be aware that your meter's accuracy will have compromises). Ultimately though, it does not matter a shit. Because we are not using the flow meter in a car to provide us with an actual total mass flow with output in kg/s. All we are using it for is an input signal to the ECU to measure load, and we tune against that load in an essentially dimensionless way. All we care about is the AFR reported in the exhaust. So it almost doesn't matter where the AFM is (unless it is outside its physical limits, like too hot, too much pressure, etc) - so long as the flow "shape" remains the same as it was tuned against, then it is good. I would still put the AFM in front of the turbo as first preference, because it is cold and clean, which is a big thing for hot wire anemometers. Next preference would be after the cooler, because at least it is "cold". May or may not be clean, as you say about oil sources. But at least it's cooler. And it is absolutely true that automotive AFMs are not intended to operate with really hot air like you will get straight out of a turbo. Neither the temperature sensors in them, the control algorithm of the heated wire, nor the electronics attached are intended to be exposed to ~100°C temps, let alone the >>100°C temps you will see at 20+ psi of boost.
-
That just sounds like lifters too. TAKE IT APART! Or at least take it to a decent mechanic.
-
Where did that CU come from? I presume it wasn't in the car, that you have obtained it along with the auto spoiler that you are installing. If so, I would not expect there to be any wiring/plugs for that system in the car.
-
Yeah, so, the obvious suspects for block noise are piston slap, gudgeons and rod bearings. Bit hard to say which it might be from here though. The video from inside the car sounds more like a spun bearing than piston slap. Hard to believe that it has been making that noise for 13000km without either it exploding (if it was a bearing) or you taking it apart to find out what the hell is wrong. There's no way that I would drive it if it sounded like that. The video from inside the engine bay sounds so much more like a stuck/collapsed lifter than anything from lower down. There's no way that I would drive it if it sounded like that.
-
R33 GTR vibrations issue over 160km/h
GTSBoy replied to Tomak's topic in Suspension, braking, tyres and drivetrain
But to continue the hijack.....the Neo has VCT, which any RB26 owner should feel bad about not having. In every other way the 26 head is at least as good as or better than the Neo. -
R34 basic info, fuel, oil, plugs, coolant etc in the US
GTSBoy replied to JC71's topic in General Maintenance
The stock fluid was Pine-o-kleen -
maxima a32 vq30 block into cima y33?
GTSBoy replied to KitsuneY33's topic in V Series (V35, V36, V37 & Infiniti)
FWD block VERY unlikely to have the same mounting positions cast into it as the RWD. Gearbox/starter quite possibly different too. I would not attempt it if I had to go and buy it, unless it was only $100. Question. Why is low comp on a single cylinder unfixable in Poland? It should be easy enough to get pistons, rings, valves, etc there, the same as anywhere else. Are you saying that there is no-one competent to repair engines in Poland? Or are you suggesting that the existing block is f**ked? -
And just to hit this one again....the difference between the 20 cams and the 25 cams is so small that the time, money and effort spent on the swap would be better spent buying 6" railway spikes to hammer into your own skull.
-
RB25DET idles weirdly after warming up
GTSBoy replied to GabRB26DETT's topic in R Series (R30, R31, R32, R33, R34)
I just had another look. There are 2 loom plugs on these TPSs, and the lower one appears to be connected. I have little direct experience with playing with these on vanilla RB25s. RB20s had a similar TPS, but the ECU used it differently. And the TPS on my 25Neo is essentially the same as vanilla 25, but I haven't had to mess with it. So I've forgotten which plug is which. You may have no real problem here, depending on what is disconnected. -
RB25DET idles weirdly after warming up
GTSBoy replied to GabRB26DETT's topic in R Series (R30, R31, R32, R33, R34)
It's idling at 600rpm. If anything, this is slightly low, not high. This is a major WTF!!!???!!??. The standard ECU needs the TPS. It cannot know you are at idle if it can't see ~0.45v coming back from the TPS. It also uses it elsewhere in the operational range to know about "accel pump" functionality, and so on. It won't be the IACV. As far as I can tell, it appears to be working. The way your tacho moves by small defined amounts looks like the idle speed is responding to the ECU changing the opening of teh IACV. -
Why do you think they are still for sale? I'd be hesitant to buy one even if I could be there to inspect it myself. Someone will eventually be buying all these cars. But at the prices that they are being passed in at (and maybe occasionally bought at) at auction in JP, they represent significant risk. They will be less risky if the price of known good 32 goes substantially higher than it is now, or if they are sold at somewhat lower prices. The big problem is that any car that has quite substantial problems needs a lot of additional cash thrown at it to turn it into the GTR that people actually want. A GTR with a stuffed transfer case, or munted interior, or crushed chassis rails, or rust, or 50 psi compression, or stuffed paint (or any of the dozen other things that could very easily and expensively be wrong) will require parts and work that are continually getting harder to find and pay for.
-
I've circled the spots where it can be a good idea to put a little sealant. The corners are always the leakiest. I should point out, that this is more true of the outside of the metal, where the other gasket runs, than it is true of the cam seal itself. I'm talking about a mere smear on the inside corner for the truly paranoid.
-
The broad answer is "no", to all the versions of your question.
-
RB25DET idles weirdly after warming up
GTSBoy replied to GabRB26DETT's topic in R Series (R30, R31, R32, R33, R34)
Let's start with the obvious. You, that is you, will have to work out where that noise is coming from. It is probably unrelated to your idle problem. It sounds like it might be the power steering pump, or something else rotating down there, simply because of how it appeared to get louder when you pointed the camera there. But the CAS is in the same general area, and it could be noisy/dying bearings or some other rubbing problem in there. But we can't find the source of the noise across the internet. Put some time and effort into working out where the noise is coming from. Do you know how to use a length of hose to find noises? Then the idle. I haven't seen such sudden, short, small changes in idle speed before. When my IACV is dirty/sticky and not responding to the ECU's drive signal properly, it will jump up to really high revs and behave much worse than that. Nonetheless, I would suggest that what you are seeing is the ECU responding to something changing (engine load caused by PS pump, possibly the rpm signal derived from the CAS) and simply driving the IACV more open/closed in response. -
Vile-side was ...... well, vile in each and every thing they ever did. Even to 20 year younger self.
-
You don't bog on top of paint. If you haven't flattened the panel enough prior to primer, then any low spots need more high fill primer.
-
Listen for the click?
-
R34 basic info, fuel, oil, plugs, coolant etc in the US
GTSBoy replied to JC71's topic in General Maintenance
Sigh. Us 93MON broadly equivalent to 98RON. -
From where? I think I recall telling you that there aren't really any still in the wild. All the ones in Japan were bought up by speculators and Americans until they could bring them in under the 25 yr rule.