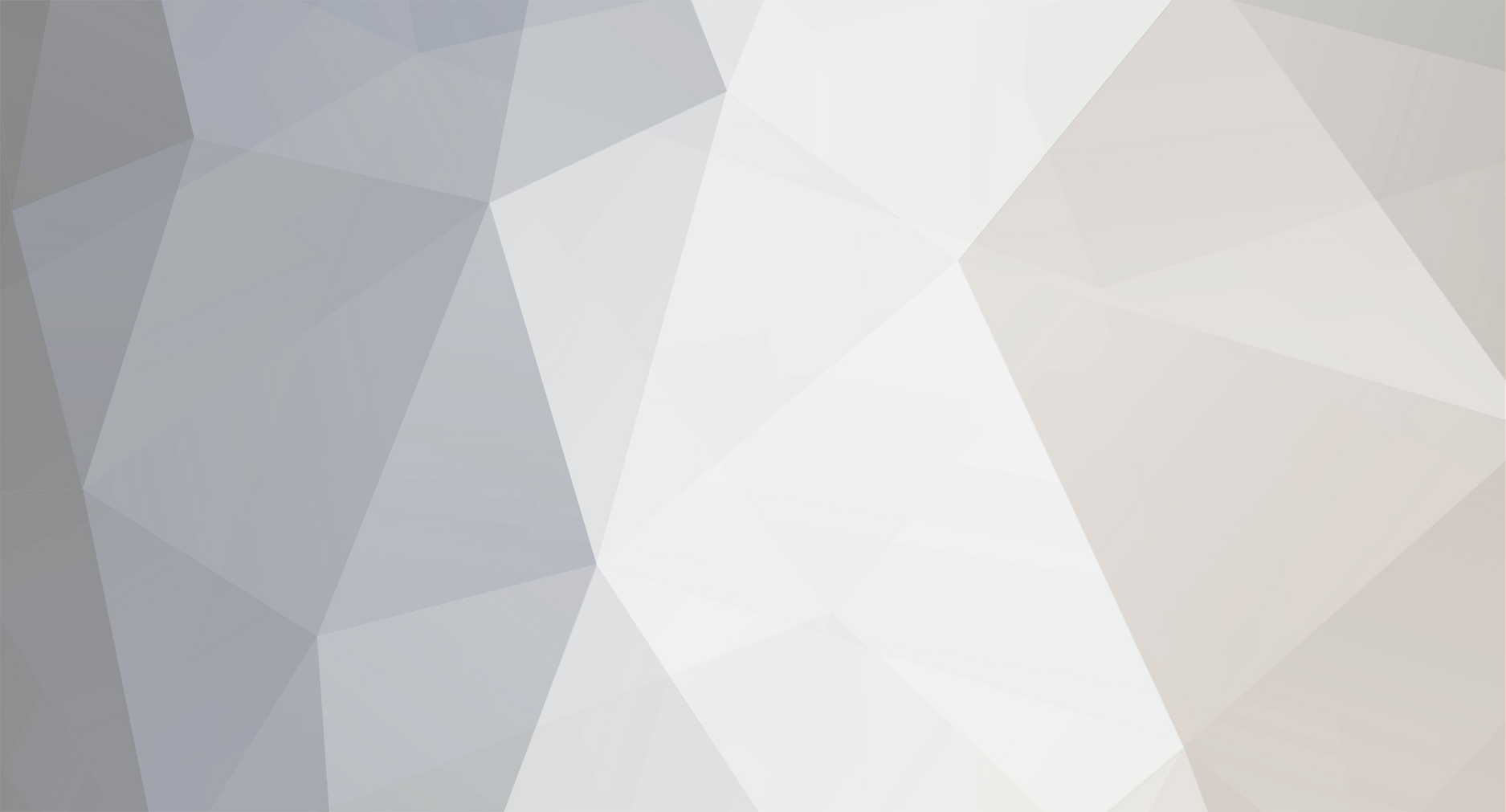
GTSBoy
Admin-
Posts
18,512 -
Joined
-
Days Won
288 -
Feedback
100%
Content Type
Profiles
Forums
Events
Gallery
Media Demo
Store
Everything posted by GTSBoy
-
Don't "upload" the pictures. Just copy the picture direct from somewhere (I usually am pasting screenshots or something else that I have on the clipboard as an image, not as a file" and just paste it direct into the post editor. Just like you were pasting it into a Word doc or something. You can't damage something if you lift it where you are supposed to. If you look carefully at the correct jacking points, you will see that they are reinforced right there. And nowhere else. That is where the "foot" of the factory jack is supposed to sit. That's why you need rubber pads with slots. 10mm might not be deep enough. Note also that the slots are not required if the pinchweld has already been slammed flat. You could just lift it at the correct spot with a flat pad, because the damage is already done. No point in making worse though, if it is recoverable. IF. Yes, that's called a chassis rail. You can lift carefully on these, if you spread the load. A decent block of wood is good. But keep in mind what I said before. Any time you start doing this sort of thing, you are off the normal path and into "be bloody careful", because it is obviously not stable. Dumb. The refinforcement is already there. See above.
-
Another Crank No start thread - r34 rb20 neo + t
GTSBoy replied to Sxnjeet's topic in R Series (R30, R31, R32, R33, R34)
Got spark? Got injector pulse? -
Note when Duncan says that, he means "when you're not using the correct lifting points on the sills, because you want to work on the sills. A 2 post hoist is not appropriate for everything anyway, and working on the sills is a good example of that, because the arms go under ths sills anyway. You're better off finding another way to support the car off the ground. Beyond that everything else D said is correct. Only the dedicated jacking points are the correct place to lift. Anywhere else is incorrect, extra caution and awareness must be used, etc etc.
-
Well, hydraulic lifters will get noisy if they are dirty/fouled in some way, and exactly how that manifests will depend on exactly what schmutz is where. There is a procedure on here somewhere for dismantling and soaking/cleaning them. Replacing them with new is about 50% of the work and about 5% of the money!
-
This seems problematic and unlikely at the same time. Vanilla RB2Xs have hydraulic lifters. They do have "zero" clearance, but only when running with oil pressure inside them. When not running, you should be able to compress them and obtain heaps of clearance. RB26s and Neos have solid lifters. They should have ~0.3mm and ~0.5mm on the inlet and exhaust respectively. If they have zero clearance then bad things are happening. With nothing else being wrong, it would mean that the valves would be held slightly (ever so slightly) open when they are supposed to be closed and it should have all sorts of problems when running, caused by leakage in/out through the valves. Or, zero clearance can indicate severe valve seat recession. None of it is good. Have you used a piece of hose as a stethoscope to try to localise the noise?
-
AC not coming from top vents
GTSBoy replied to Templim's topic in R Series (R30, R31, R32, R33, R34)
What HVAC actuator is under the steering wheel? Do you mean on the RHS of the centre console, immediately to the left of your shin? If so, then yes, it is probably that one, because that is the mode door actuator, and from what I know, it's still a pain in the arse to replace. I don't know about whole dash out, but you certainly have to rip into the centre console section. I don't know if it's covered in the workshop manual, as I haven't spent much time looking at those parts of it. (and by "the workshop manual, I mean the R32 GTR one, which is the most comprehensive one we have, and it should be similar enough between that and later cars to serve as a guide). -
VCT, yes.
-
Well, I was going to say, "Is the wastegate set up so that it is not leaking?" That's actually a different thing to what you're asking about. In theory, if you have allowed the two halves of the manifold to commmunicate (more than the stock manifold does - which is at least a little bit) then the negative effect should be apparent in delayed spool, not in outrigth power. OK, maybe just maybe, a badly set up twin scroll wastegate "crosstalk" might kill the top end, although it's hard to see how. What is happening with the original wastegate in the turbo? is it sealed off properly. If it's left flapping in the breeze, it will f**k everything up. If it is still there, and can be returned to service, I'd be capping off the external (presuming the two halves can and will be isolated from each other after doing so) and have a go with just the stock wastegate. I have an internal wastegate in my highflowed rear housing. The bigger opening and flapper should be fine to >250 rwkW. So there's not exactly a pressing reason to have the external. Done right, an external will give better results. Done wrong, it might just be possible to have worse results. Report back!
-
Potential MAP Reference Point
GTSBoy replied to Radical_Goodspeed's topic in Engines & Forced Induction
It might be fine. I was just saying that I wouldn't trust it without testing it. -
Potential MAP Reference Point
GTSBoy replied to Radical_Goodspeed's topic in Engines & Forced Induction
That's just a gauge, with a certain amount of electronic damping, and no-one cares if it is timely-accurate. I'd hesitate to use it for an ECU MAP input without knowing that it was a nice signal. Responsive but smooth. Not laggy. Not lumpy. -
Potential MAP Reference Point
GTSBoy replied to Radical_Goodspeed's topic in Engines & Forced Induction
Getting a decent signal from all 6 throats is a challenge. I don't know for sure, but I suspect that the stock balance tube is not ideal for it. I have done it on an ALFA 4 cylinder (about 35 years ago, so don't ask for too many details). We drilled 4x holes in the manifold runners, put in some fittings and ran hoses to a decent sized (I think it was about 20mm diameter) pipe that ran the length of the inlet manifold. So, it was quite a decent volume. There is a "tuning" balance to be found between the volume of the common plenum on such a thing and the diameter of the pipes running from it to the runners. You need the volume to be large enough to damp out the sharp spikes in pressure signal you get as each runner gets sucked on by its cylinder, but not so large that it becomes too slow to respond to actual changes in MAP. And you need the hoses to be small enough to transmit the signal quickly, but not so small that they delay the signal. You might have to have more than one go at it, if there isn't any actual success based wisdom to be had here. Hopefully there is. Anyway, I would not do it on only a couple of cylinders. I would also not care about "permanently modifying a part". Just bloody drill holes and make stuff better. There is nothing sacred about any GTR unless it is a genuine museum piece that you shouldn't be modifying at all anyway. -
ugently need expert / experienced opinion
GTSBoy replied to sunsetR33's topic in R Series (R30, R31, R32, R33, R34)
No, you cannot perma-bend hose once it is already made. -
ugently need expert / experienced opinion
GTSBoy replied to sunsetR33's topic in R Series (R30, R31, R32, R33, R34)
If it doesn't have a bunch of funky bends, then yes, you can just use straight hose. -
There are other crowds doing 25Neo conversion kits.
-
Nissan Gloria Hy34 issues
GTSBoy replied to OO Dan OO's topic in V Series (V35, V36, V37 & Infiniti)
Not familiar with that car at all....but that code is for the traction control. Does it have a 2nd throttle in series with the first, like the R34 Neos do, to make the traction control happen? -
Well, in that case it is either completely normal accel enrichment, or it is completely abnormal accel enrichment, caused by a problem that we will be unlikely to be able to guess at this distance, but which will turn out to be f**king weird.
-
V36 wreck (edited from V37 by mod)
GTSBoy replied to Pete_Repeat's topic in V Series (V35, V36, V37 & Infiniti)
That's it. Too rich for me. I'm out. If it does start to sell in pieces, I'll probably register an interest in the diff & axles, gearbox & tailshaft, and maybe the brakes. -
Is it oil smoke or fuel smoke? They smell different.
-
ugently need expert / experienced opinion
GTSBoy replied to sunsetR33's topic in R Series (R30, R31, R32, R33, R34)
I only use rubber also. I have an intense distrust of silicone for coolant. -
Never ending fuel pump drama
GTSBoy replied to Murray_Calavera's topic in Engines & Forced Induction
Clamp meter will probably tell you lies. PWM DC looks a bit like AC (because the voltage is going up and down rapidly), but it is not AC because the voltage never goes negative and the current never reverses direction. But because it looks like AC, and it is happening at high frequency, at can cause wierd reactive effects. Just be warned that you might learn things that are....confusing. Because they aren't necessarily real. -
Vcam is, by definition, a good thing. The reason the 25Neo is a better engine than the 26 is the VCT.
-
V36 wreck (edited from V37 by mod)
GTSBoy replied to Pete_Repeat's topic in V Series (V35, V36, V37 & Infiniti)
[knuckle to corner of eye] Awww. [/knuckle to corner of eye] -
V36 wreck (edited from V37 by mod)
GTSBoy replied to Pete_Repeat's topic in V Series (V35, V36, V37 & Infiniti)
My wife says we have a spare set. -
Never ending fuel pump drama
GTSBoy replied to Murray_Calavera's topic in Engines & Forced Induction
PWM quite literally just chops the ful 12V voltage on and off at whatever duty cycle you're running it at. If you're running it 100%, then it is on full voltage all the time, same as if there was no PWM. If you run it at 50% duty cycle, it is only seeing the full 12V half of the time. This is broadly equivalent to running it at 6V. But the crucial difference is that motors (and a lot of other loads) don't like being powered at low volts. They will either fail to start rotating, or draw a shit ton of current, or other undesirable things. But if you give them the full volts, and then a short period of no volts, and then some more full volts, then the times when they are seeing power they are seeing all the voltage, and they are happy. But you get the performance out of them as if they were only seeing that fraction of the full voltage. It is not really easy to answer your question about what flow you will get out of it at 50% duty cycle. I can tell you that it is not as simple as you think. For a start, that 460 L/h pump is not going to flow 460 when you're on boost. When you're on boost you will be somewhere down the sloping part of that red line. If you have 15 psi of boost, then the pump can only deliver about 95 gal/h, which is <380L/h. So your simple 50% on 460 = 230 wasn't going to work anyway. But also, it won't deliver 50% of 380 either, because when you devolt or PWM trim th epower being fed to the pump, it is not able to deliver flow or pressure in the same way. 50% duty cycle will probably produce <50% of the full voltage flow. The way to find out what duty cycle you need to run it at at low load (ie, at idle) is to idle it and turn the DC down until you start to lose fuel pressure, then turn it back up above that with some extra for safety. And then you do the same thing at full load, in case it doesn't need anywhere near 100% DC. And if you're careful/cautious/prudent, you will also do it at a couple of loads in between so you can shape the DC map against load. It might not be linear between the two end points. -
Turn signal wiring question
GTSBoy replied to OakvilleGTR's topic in R Series (R30, R31, R32, R33, R34)
Yes, multi relays needed, and possibly a diode. I'm not actually going to think about it though.