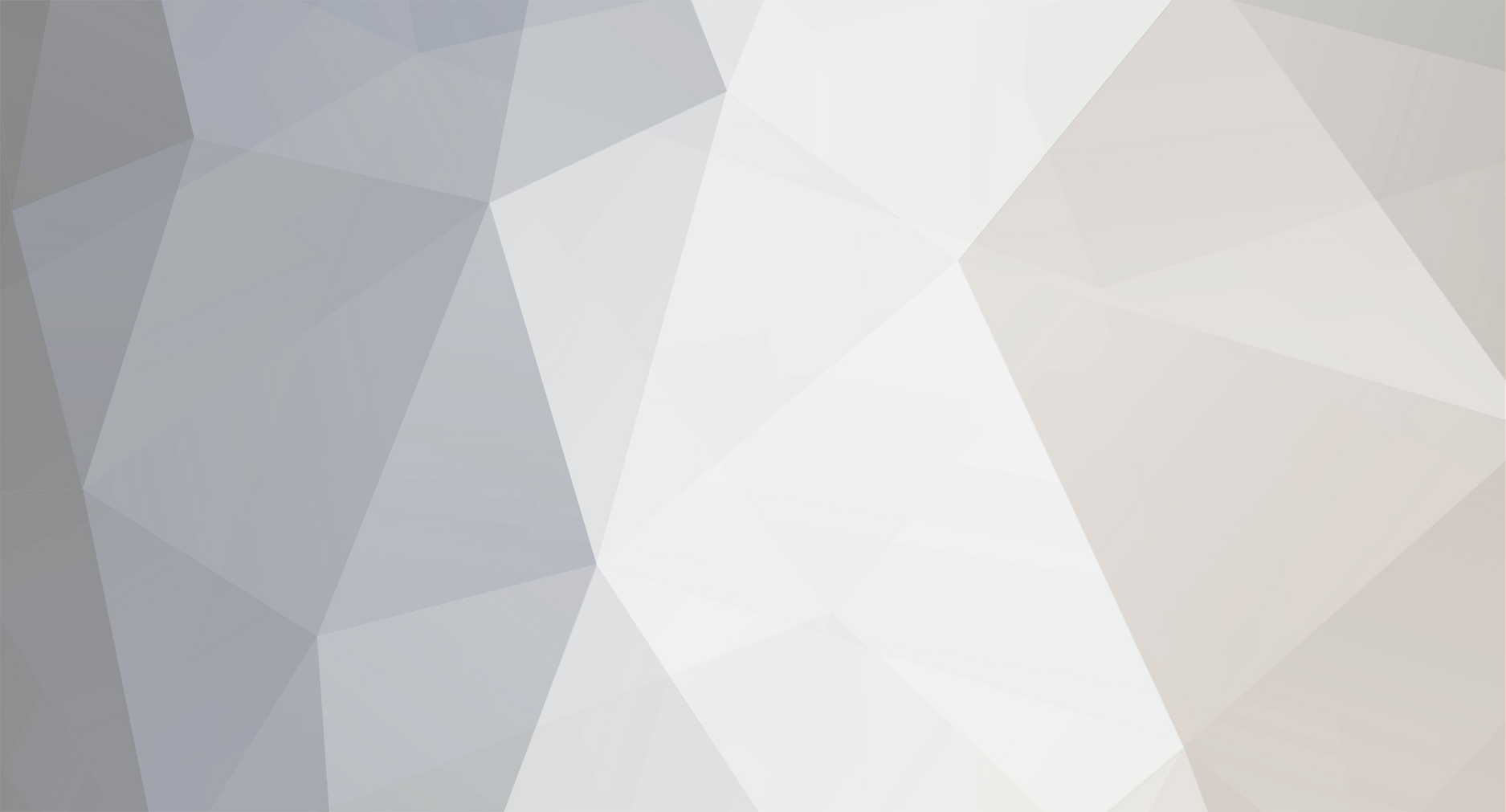
Warpspeed
Members-
Posts
875 -
Joined
-
Last visited
-
Feedback
100%
Content Type
Profiles
Forums
Events
Gallery
Media Demo
Store
Everything posted by Warpspeed
-
Excellent sydneykid. I would just like to add to your mention of variable inlet cam timing on the RB25. As sydneykid says the variable timing is there to meet emissions, it is not there for power. What Nissan have done is put in an inlet cam with fairly short duration. At idle the inlet cam is fully retarded to remove any troublesome valve overlap, that would degrade emission under high inlet manifold vacuum. At some low RPM, probably around 1200RPM (not sure ?) but well above idle, the inlet cam is fully advanced. This causes the inlet valve to close early, increasing the low end torque that is available. At a higher RPM (4,200 I believe) the inlet cam is again retarded. The later inlet valve closing increasing the top end torque and power. The thing to realise is that the inlet cam duration is still rather short, and moving the cam around is really a band aid solution. For good cylinder filling, really more duration is what is required. There must be something about the RB25 combination that has caused the Nissan engineers some real grief in having to go this extreme solution, to get it to pass emissions. Whatever the problem was, they do not seem to have had it with the RB26 engine, so there is no variable inlet cam timing. If it offered any performance advantage at all, you can bet it would have been used on the RB26 in a flash. The only other thing I can think of to mention with RB cams, is that the exhaust cam has the tang to drive the cam position sensor. The inlet cam has no tang. So you can use an exhaust cam in either position, but an inlet cam must always be used as an inlet cam. So if you are going to buy a whole bunch of various cams to mess about with, get yourself all exhaust cams if you can.
-
Steve, as far as I know there is no real way to calculate the various combinations of turbine size, back pressure, and camshaft specs. The only help I can give, and its not much, is to say that for every extra pound per square inch of pressure you can get rid of from the exhaust manifold, you will increase engine output by roughly one percent at the same boost level. Low exhaust back pressure is also a very good way of fighting the detonation demon. Let the heat escape out of the combustion chamber and down the pipe. A constipated engine will detonate far sooner than a free flowing engine, all else being the same. When you fit a larger turbo, and keep the boost the same, power will increase. This is due to the reduction in total exhaust back pressure. A larger more efficient compressor may have lower discharge temperatures, but if you run an intercooler, the effect on the engine will be absolutely minimal. (at identical boost level) Exhaust back pressure is made up of the drop across the exhaust turbine, plus the drop across the whole exhaust pipe length. We all know what a larger exhaust pipe can do for a turbo engine. But a larger exhaust turbine works the same way, but the effect can be even more dramatic. To figure out what is going on, you need to take some pressure readings. As for camshaft specs, it all depends on what you want and who you talk to. I cannot really give definite advice. But having said that, a longer duration exhaust cam will free up the engine considerably without losing any low end torque. It will make the engine feel more revvy. If you only change one cam, do the exhaust first. The only downside is that a longer exhaust duration shortens the power stroke, and lengthens the exhaust stroke (obviously). The effect is that it reduces pumping losses at full power, but reduces engine thermal efficiency at small throttle openings. The reason manufacturers do not use long duration exhaust cams is because it lowers light throttle cruise fuel economy slightly. This may be a big thing for them, but maybe not for you. A longer duration inlet cam shifts the power curve upward. If you keep fitting a series of longer duration inlet cams you will find that at first there is a slight increase in top end, and a slight decrease in bottom end. As you go more radical, the drop of at the bottom becomes very pronounced, with only a slight or zero top end increase. For a small turbo street engine, using the stock inlet cam, with about ten or fifteen degrees more duration on the exhaust side. this will liven things up more than you might expect, at half the cost. With a mid size turbo you might want to increase both cams the same, which is what most people do. Same with a monster turbo, two monster cams to go with it. Everyone has their own ideas about all of this, so I suggest you talk to as many people as possible. But someone elses idea of a good cam may turn out to be less than wonderful.
-
Steve, I do not have an RB25 rod to compare it to, so cannot say for sure. What I can tell you though, is that the RB26 crank, rods, and pistons will drop straight into an RB25 block without any other changes. This is a very good and cost effective modification. All three components are beefier, the compression ratio drops to a more boost friendly 8.5:1, and you keep the same engine number (hint). There seem to be a fair few wealthy people importing low mileage R34 GTRs, and as soon as they land, dropping a stroker kit into the engine. The very slightly used parts end up in the for sale section of this and other Forums fairly regularly. You should be able to get the lot for under a grand. But there are more people waking up to this now, so you need to be very quick indeed. The Nissan engines need to pass the strict Japanese emissions laws, and valve overlap is a fairly critical factor for idle and light throttle emmissions. If you look at just about any recent engine from anywhere, it will have zero or only very slight valve overlap. The design philosophy between the RB25 and RB26 is very different. The RB25 is made to have reasonably good low down off boost performance. You can see this with the higher compression, and longer intake runners. Think of it as a turbo assisted engine. On the other hand the RB26 has lower compression and very short intake runners, it is going to be a slug off boost, and it was designed that way. The turbos provide all the performance, it is a real no compromise high power turbo engine. How much valve overlap you can get away with depends on how high the exhaust back pressure is in the exhaust manifold. This in turn depends on exhaust turbine and housing size, and wastegate opening point. Fit a pressure gauge to your exhaust manifold before the turbo, and be in for a real surprise. Stockie engines might typically see twice boost pressure in the exhaust manifold. Winding up the boost actually makes this even worse. If you fit a high overlap cam to an engine like that, exhaust reversion is going to kill power. BUT if you fit a bigger turbo with a bigger exhaust turbine there will be less back pressure, unfortunately boost threshold rises at the same time. You can run more valve overlap with a bigger turbo. So little turbo, little cam. Big turbo big cam. You need to get the combination right. You can get to the stage where the turbo is so big there may be no boost at all below the extreme top end. But the exhaust back pressure may be lower than boost pressure at that point. You can really put a massive overlap cam into something like that, and the top end power would be unreal. But it would be just about undrivable. There might be no power at all up to a certain high RPM point, then it will just wheelspin up to the rev limiter in any gear. Sounds like fun, but you would not want to drive to work in it every day.
-
I have all the internals of an RB26 here with me now. The RB26 conrod looks to be 120mm long measured by eye with a steel ruler. It may actually be plus or minus maybe 1mm or so, but 120mm looks about right. The RB25 and RB26 blocks are interchangable as far as main internal dimensions go, so if you know the stroke lengths you can calculate rod ratios from that. I was hoping Pewee was going to give us some cam specs. Meggala has cam specs for some of the Nissan RB and SR engines on his website. Below are some of these thieved from Meggala. R33 RB25DET Inlet cam 240 degrees 7.8mm lift, lobe centre 120, timing 0-60ABDC Exhaust cam 240 degrees 7.8mm lift, lobe centre 117, timing 57BBDC-3ATDC overlap 3 R34 RB25DET Inlet cam 240 degrees 7.8mm lift, lobe centre 100, timing 20BTDC-40ABDC Exhaust cam 240 degrees, 7.8mm lift, lobe centre 117, timing 57BBDC-3ATDC overlap 23 R32 & R33 RB26DETT Inlet cam 240 degrees 8.58 lift, lobe centre 113, timing 7BTDC-53ABDC Exhaust cam 236 degrees, 8.58 lift, lobe centre 125, timing 63BBDC-7BTDC overlap 0 R34 RB26DETT Inlet cam 240 degrees 8.58 lift, lobe centre 117, timing 3BTDC-57ABDC Exhaust cam 236 degrees, 8.58 lift, lobe centre 121, timing 59BBDC-3BTDC overlap 0 It is a fairly well known trick to retard the GTR exhaust cam about 4 degrees to increase the overlap from 0 to 4 degrees. This helps the top end breating a tiny bit. If anyone can add anything to this please post some details. I am particularly interested in the variable inlet cam details on the RB25 if anyone has them.
-
I will have a go at answering your piston question. The thing about any highly stressed part is not how much metal there is, but where the metal is, and where the stresses are. The aerospace people are very good at designing very strong parts that are also light. The trick is that you can safely remove material from places where there is little stress. If you have ever examined a piston that has cracked due to detonation it is the ring lands between the rings that fractures. The ring grooves are rectangular in section, and the cracks start at the root of the ring groove, and goes through to the next ring groove. Usually a whole section of ring land breaks away and rattles around trapped between the rings. The way to make the ring lands stronger is to put more meat into the ring land. In other words place the rings further apart so the ring lands are wider. In most cases the crack does not go further into the body of the piston, but sometimes it will. So putting an oil cooling duct in the pison crown is probably not going to weaken the piston significantly. I have never seen a detonation fractured GTR piston, but I am unaware that there is a design problem here. If pistons were cracking through to the cooling duct, and it was a common fault, we would all have heard about it by now. I have actually broken a piston into two parts due to massive detonation (and my own stupidity), but I could not say that the piston design was in any way at fault. Design problems always show up as the same recurring fault. A one off failure is not a design problem.
-
Peewee, I am sure all you say is true. But why do you always just rubbish without offering anything constructive. People read these posts hoping to learn something new or interesting. So why not try and give facts, figures and explanations. If you have the knowlege and experience that you claim to have, share it with us. What exactly is it about the RB engine that you do not like. If you were going to re design it how would you do it and why?
-
Steve. Engine geometry is a fascinating subject in itself. If you start off with just the cylinder block, the distance between the head face and the crank centerline will be some fixed dimension. When you decide to fit crankshafts with various strokes to this same block, there are a few side effects to the internal geometry. The first thing is that at TDC the piston is always going to be at the top of the bore, level with the top of the block. At BDC it will be the stroke length down the bore. So what Xeron says about all the additional stoke length being at the bottom in a long stroke engine makes sense if you think about it. Carrying this a bit further, a longer stroke engine will have the crankpin higher at TDC, and lower at BDC than a shorter stroke engine. So it follows that If you use identical pistons the long stroke engine must have conrods shorter by half the increase in stroke length. This all assumes an identical block is used for all these changes in stroke. There will be a ratio of conrod length to crankshaft stroke, called the rod ratio. If the rods are 100mm long and the stroke is 50mm the rod ratio will be 2.0 If you increase the stroke, the new conrods might have to be 95mm, and the stroke 60mm, giving a new rod ratio of 1.58 As sydneykid says another way to do it might be to keep the same conrods in the long stroke engine, and move the piston pin 5mm higher up the piston. In this case there would be 100mm rods with the 60mm stroke giving a rod ratio of 1.66 The higher pison pin placement may not be physically possible, or it might require the ring package to be very high with close ring spacing. This will weaken the ring lands and make the piston more susceptible to detonaton damage. But it also might lead to a shorter and lighter piston as well. So whats the big deal with rod ratio ? Try to imagine an engine with the shortest possible conrods, at the 90 degree stroke points the conrods will be at an extreme angle to the bore. They might slope 45 degrees one way, and then slope 45 degrees the other way. (not actually possible, but you get the idea) Now imagine some very long conrods, maybe two metres long. The conrods will always be almost vertical throughout the entire stroke. Vertical downward pressure on the piston is going to try to wedge the piston against the side of the bore with the very short rod engine. The long rod engine will push straight down onto the vertical conrod putting almost no sidethrust onto the piston at all. This is more mecanically efficient, but very long conrods are going to make the engine block tall and heavy. So there has to be a compromise in this. Conrod ratio also has an effect on the motion of the piston in the bore. If the conrods are very long the piston moves almost in a perfect sinewave motion. Short conrods distort this, the piston moves faster during the top half of the stroke than the bottom half of the stroke. This is difficult to visualise, and almost impossible to put into words. But either get yourself an engine, or make a cardboard model, and plot piston position for each ten degrees of crank rotation. You will find that the piston almost stops dead for maybe thirty or forty degrees of crank rotation around BDC. The piston might move less than 1mm or 2mm. The bottom of the conrod swings in an arc on the piston pin, which corresponds to the arc of rotation of the crankpin. So the piston just stops for a while. At the top of the stroke, the piston rapidly decelerates and changes direction very suddenly with a short conrod engine. So the rod ratio has a dramatic effect on the piston motion in the bore. This has all sorts of side effects, and influences what happens on the induction stroke and power stroke, and also valve timing requirements.
-
Hi again Sydneykid. I knew you could add something really worthwhile, you always do. Have you ever tried putting an RB26 crank with some verrry long rods into one of your RB30DET motors ? The rod ratio would end up well over 2.0, I did work it out once, but cannot remember the exact rod ratio figure. I think it was Bill Sherwood on another thread said the Formula one guys are using a rod ratio of about 2.3 or something. The change in piston motion around TDC and BDC would be pretty dramatic. From what I have read huge rod ratios give better high RPM cylinder filling for a given cylinder head flow, and port volume. Any ideas on this ?
-
The GTR pistons have proved to be a very good design. I know nothing of MR2 pistons, I have only seen pictures. Also Mazda are now doing this as well on some turbo engines. The circular oil cooling gallary that runs behind the top ring and the two diagonal oil holes in the GTR piston are very clever design. I have looked at this for a long time, and I am stuffed if I know how they manufacture it in a cast piston. The oil squirter squirts oil straight up into one of these holes. The oil then runs around inside the hollow piston, and drains out of the opposite hole. A very ingenious and efficient way to remove heat from the piston crown. But Steve is right. You would make yourself more welcome I you added to the knowledge rather than slinging off at people and thier cars. If you piss off enough people the moderators might start to take an interest in you.
-
First I never said RB engines have good midrange, someone else here said that. But I challenge you to give actual dimensions for the good Formula one head, and the very poor RB head, to prove the 20% difference in valve to port ratio. I want actual figures, because I do not believe you. Yes I agree with you it is possible to overcam an engine. So what everyone knows that.
-
Yes Steve, I think Corky Bell mentions MEP in both his books. I find it interesting that it is the combination of MEP and RPM that give the final power figure. High RPM are going to put a lot more stress and wear on engine parts than high MEP. So if you can get 400BHP at 6,000 RPM with a turbo, it is going to be a lot kinder on the engine parts than 400BHP at 9,500 RPM normally aspirated. The turbo engine will have a far higher MEP (and torque output) because of the boost pressure. The formula for piston speed is: stroke in mm, multiplied by RPM, divided by 153. This gives you mean piston speed in feet per minute. This is the figure everyone uses. Maximum peak piston speed will be a lot higher. The main reason Formula one engines can reliably rev so high, is that the stroke length is very short. They get the required capacity from bore size and number of cylinders. Motorcycle engines also rev easily because the cylinders are small and the stroke is short. Some of them can reach crazy RPM without huge conrod stresses. I am not sure what the exact stroke length of the current V10 engines is, but I think it might be around 55mm. At 18,000 RPM the piston speed would be 6470 fpm. Well beyond a steel conrod, and getting pretty high even for an aluminium or titanium conrod.
-
Well Steve, I certainly do not claim to be an expert, but my beginners understanding of the stresses on engine parts are as follows. Maximum pressure loading on the piston will occur at around 20 degrees ATDC on the power stroke. It should rise to a smooth hump peak around this point. Thermal loading depends on all sorts of things, but if the engine tuning is correct there should be no hot spots, and the piston crown temperature should not be high enough to cause pre ignition or lower the structural strength of the piston material. Detonation is really the only way you are ever likely to kill a piston, assuming it was installed and clearanced properly. Conrods really only have two problems. Firstly the tensile (pulling apart) stress at TDC on the exhaust stroke is the highest stress the rod will see. This depends on piston weight and RPM. The cyclic tension and compression can eventually fatigue the rod to the point where fatigue cracks can begin. That is the reason they polish rods to help to eliminate surface imperfections where cracks can begin. The second problem is that the same tensile stress can stretch the big end bolts and cap out of shape. This can lead to bolt failure, or lubrication problems where the big end bearing can spin or burn. As the big end stretches, the sides pull inward and squeegee all the oil off the journal. This is RPM related as well. You only really require special rods if you are planning an increase of RPM well above stock. On a road car a piston speed of 4000 FPM should be the redline with steel rods. For drag racing, or where the engine will be regularly inspected and rebuilt, 4400 FPM might be as high as you would want to go. A large power increase, using stock RPM levels does not require special rods unless the original stock rods are rubbish, or boost levels are truly extreme. Usually the rod bolts are the weakest part of stock rods. Crankshaft bearings should not present any real problems, provided engine balance is reasonable. Beware of crankshaft torsional vibrations with six cylinder engines that have longish strokes. This can lead to crankshaft fatigue failure, and ring flutter problems causing blowby in the front cylinders. I am sure Sydney Kid will be able to add to this list. MEP is mean effective pressure. If you add up all the positive and negative pressures during the induction, compression, power, and exhaust strokes, you end up with a positive average pressure dominated by the power stroke. This average pressure can be thought of as what pushes down on the piston and produces output torque from the engine. If you know MEP, bore, and stroke you can easily calculate flywheel output torque. It is a figure of merit for an engine. There are two ways to gain more power, increase MEP or increase max power RPM. The reason I was asking Peewee what MEP his supertuned engines run that easily break pistons. I wanted to know if he could give me a figure, for peak pressure, and average pressure (MEP). If he can so easily break pistons, I would not want him to tune my engine thats for sure.
-
Peewee I have read through your post several times, and none of it makes any sense at all. It is in the English language I think, but none of the words seem to convey any meaning. Are you asking a question, or making a statement ? I cannot even think how to reply to such total rubbish. Are you completely stoned on something, or what ? Maybe someone else can understand what Peewee is on about, and respond to his post.
-
Peewee, what sort of peak cylinder pressures are you talking about that will break pistons ? Give me a pressure figure. I would also like to know the MEP of the engines that one of your good tunes can create that will break pistons.
-
Hey Peewee, you have just discovered the relationship between port area and valve area. This cutting edge technology was researched by R.G. Falls and S.W James in a thesis published in 1941 (at MIT). the title of the paper is "effect of diameter ratios on flow through inlet valves of internal combustion engines". Get a copy and read all about it. More work was done by Keith Duckworth for Cosworth on combustion chamber design. The current crop of four valve DOHC Japanese cylinder heads are the result of one hundred years of constant research and development by the best engineers available. All this work is public domain, there are no secrets here. Formula one engine designers do not have secret mathematics, they still operate under the laws of basic physics. Get real.
-
You are right Steve, detonation is what wrecks pistons. Usually it breaks the ring lands or sometimes even the top ring. Detonation is when the combustion process turns into an instantaneous explosion. The idea is that the combustion process creates a steady increase in pressure which smoothly pushes down the piston. There will be a critical combination of temperature and pressure where the mixture spontaneously explodes. This is the dreaded tink tink shock wave created by detonation. High octane fuels can stand more heat and pressure before they spontaneously explode. Excessive combustion chamber temperatures due to lean mixtures, or too high a compression ratio will do it as well as excessive boost pressures, or excessive ignition advance. There is a combination of factors, not just one factor. You cannot say that a certain engine will detonate with 10:1 compression, and not detonate with 9.8:1. Or that 14psi boost is o/k and 15psi is not. Or a certain particular weak air fuel ratio will detonate at full load. It is the combination that counts. If you have detonation you are going to have to change something to get rid of it. What is easiest or best to change depends on what you have. Usually there is something wrong with the engine tuning, and a proper dyno tune by an expert can put things right. But the higher boost you run, the less margin for error there is. Also remember that the fuel you buy may not always be up to the advertised octane standard it is supposed to be. So a bad load of fuel can destroy your engine if it is tuned right up to the detonation limit on best quality fuel.
-
I can understand how say a used cast iron exhaust manifold can be sand blasted and chemically cleaned inside and out prior to putting on the magic ceramic HPC coating. But what about a slightly used dump pipe or extractors ? How can they remove the black crap from inside a long twisty pipe ? I would assume only shiny new pipework can be internally coated with this stuff. The reason I ask, is that you might want to test several experimental exhaust systems on the dyno. Then when its all sorted out, get that system treated. But it will be full of black crap after testing.
-
I have discussed this topic in a fair bit of detail on previous threads on both SAU and SDU Forums, it might be worth your while doing a search using SUPERCHARGER or TWINCHARGE as key words. Another place to look is a thread I contributed to on the GT-R Register Bulletin Board (UK). Look under Technical/Turbos, in the archives there will be a thread titled "Supercharger as well?" http:www.gtr.co.uk/forum/upload/showthread.php?s=c2f334bb7c5525911d87eaa6 I lost my password and have not bothered to re-register on that Forum. For some strange reason my WARPSPEED handle has defaulted to someone called "ellisnc" whoever he might be ? But in response to my posts I am referred to as Warpspeed, and it is really me not ellisnc ! So ellisnc must be as baffled as I am ? For some reason the link does not come out as I typed it in, try gtr.co.uk/forum/upload/showthread.php?s=c2f334b7c5525911d87eaa6
-
Hey russ, thats great. What are you planning, come on now, make a full confession.
-
Hi russcb007. Steve is right about engine management, the airflow meter just sees more air, so adds more fuel. In fact the engine management self learning will slowly adapt and fully remap the ECU over the whole part throttle fuel map. Full throttle mapping at low RPM will not be that far out either, because it just adds more fuel automatically. It is not the same as say doubling the boost pressure with a stock turbo. Here the engine could go dangerously lean because either the injectors, airflow meter, or fuel pump may top out. The only problem you might encounter is that the ignition may be over advanced at low RPM. But even here most mechanical (turbo) distributors and ECUs employ boost retard on the ignition curve, or alternatively, the detonation sensor will retard the ignition. If your engine was originally n/a it will not have provision for boost retard of ignition timing, and you may have problems with overadvanced full throttle low RPM ignition. Supercharging a previously turbo engine in my experience has worked o/k every time for me. For best results a full dyno retune is required of course, but you are not likely to blow your motor just because you now have a lot of new low end boost pressure than you originally had with the turbo. Just removing a turbo and fitting a supercharger will radicaly change the engine characteristics, even with an identical boost level. A supercharger can never give that top end rush, but what you end up with is bulk low end and midrange grunt that slowly tapers off and dies right at the very top end. How badly this tapering off is, depends on a lot of factors, but you can get most or all of it back with some further engine work. Twincharging will give you absolutely everything you want, because you can set it up to behave as you desire. By changing pulley ratios, and turbine exhaust housing size you can make it act more like a supercharged engine, or more like a turbocharged engine. If cost and complexity does not frighten you, and you enjoy a challenge, go for it ! The easiest way to go about it is to first supercharge your engine, sort it all out and get it running right, then add a really large turbo in SERIES with the supercharger. Lancia and Nissan have both sold production twincharge systems. Both of these are series flow, where the turbo compressor and supercharger flow the same air. I have built a system like this myself, and would have no reservations about doing it again.
-
Just did a netsearch myself. It seems Jaguar introduced a supercharged 4.0 straight six in 1994, then replaced it with a 4.0 supercharged V8 in 1998, hence all the confusion. http://www.nsnews.com/issues98/w022398/testdriv.html
-
Hello Duncan. Now this is mighty interesting. I know Jaguar make a 4.0 (4.2) Litre V8, but I have here a Magazine article that gives details of the supercharged six as also being 4.0 Litres ? ? This article appears in Zoom April/May 1997 page 70, and briefly describes the following supercharged engines, Holden 3.8L V6, Mazda 2.3L 800M miller engine, Jaguar 4.0 six, and Mercedes SLK 2.3L supercharged. What it says, and I quote from directly Zoom........... The XJR uses a positive displacement Roots-type Eaton M90 blower - yes the same basic unit as the one on the Holdens ! The blower is driven at 2.5 times crankshaft speed (13,750rpm at the redline) and it boosts to a maximum of 0.7 Bar (10psi). A compression ratio of 8.5:1 is used and the valve timing is such that there is no overlap where both intake and exhaust valves are open at the same time. The 4 litre straight six has a mighty power output of 240kW (320bhp!) at 5,000 rpm and a peak torque of 512Nm at 3,050 rpm. If you buy the supercharger unit from Jaguar it will set you back by $2,970. End of quote................. I hear what you are saying Duncan, but now I am confused, anyone know more about this ?
-
Hi Steve. A four stroke engine only has an induction stroke every second revolution for each cylinder. So for each turn of the crank only three cylinders will be on an an induction stroke, or 1300cc of air per crankshaft revolution will be drawn into the engine, for an RB26 anyway. If a positive displacement supercharger also had a displacement of 1300cc of air per rev, there would be no boost if it turned at the exact same speed as the engine. There would be atmosperic pressure upstream and downstream of the blower. But if the blower pumps more air in, say 1.5 times as much, or 1950cc, then this air will be compressed so it fits into the volume of 1300cc that the engine will flow. The pressure will rise to 1.5 times atmospheric. This is 0.5 Bar boost, or 7.35 psi. This is all very theoretical, perfect engine, perfect blower, no pressure drops, no rotor leakage, and so on. What you end up actually getting, might be more or less boost on a real engine. But it is a good way to make a really quick rough guess as to how fast you might need to turn a certain blower on a certain engine to get somewhere near the boost you want. Yes, the Jag is a 4.0 Litre straight six, DOHC four valves per cylinder. I agree the new Holden M90 is a very good deal. I strongly suggest you make up a dummy blower first and see if it is going to fit before forking out $1600 though. I have never used one of these, and they look pretty bulky. Shorter drive snouts may be available from Eaton as a spare part, or it may be possible to fabricate something yourself if this is going to help to install it. You will need a flat, very strong surface to bolt the blower onto, and the mounting/manifold can be either steel or aluminium. Personally I prefer steel because it is easier to weld and work with, and I can do it all myself at home. Aluminium will need to be very thick, and probably will not end up any lighter in the end.
-
Some excellent cam design info MegaGTS4 in the second link. As far as blower size goes, it has more to do with required airflow than actual engine size. For instance a 5.0 litre engine with a 4,500 RPM redline might require about the same size blower as a 2.5 Litre engine that redlines closer to 9,000 RPM, at similar boost levels. For both engines the maximum blower speed might be 13,500 RPM, but the 5.0 litre engine would turn the blower at 3 times crank speed, the 2.5 Litre engine at 1.5 times crank speed. In my opinion an RB25/26 engine is not a typical production engine, it has far better top end breathing than a lot of similar capacity engines. If you look at the power levels produced by the M90 on larger engines at typical roots blower boost, maybe 7 to 10 psi, you might expect 150 to 200 Kw. This would be a reasonable power goal for an RB25/26 at those same boost levels as well. As a very rough guide, an RB26 will inhale 1300 cc worth of air each revolution. If you run 0.5 Bar boost (7.35psi), the blower must inhale 1950 cc worth of air per engine revolution. With a theoretical blower capacity of 1400cc per revolution, it must be driven at 1950/1400, or 1.39 times crank speed. There are going to be a lot of factors that influence the final boost you end up with, particularly exhaust back pressure. My first guess with an M90 on an RB25/26 would be to try a blower drive ratio of about 1.5 as a starting point. This would be a pretty comfortable compromise between blower leakage and maximum blower RPM. According to Eaton, the M62 is supposed to be a more appropriate size. It probably would be on an older 2.5 Litre two valve pushrod engine with lower redline.
-
I just realised that in an earlier post I said the SC14 was way too small, then in a later post that the SC14 and M90 are actually about the same size. Duh... In a sense it is true though. I perhaps should have said, the airflow at max reliable blower RPM for the SC14 is not going to be sufficient for your RB25DE. Example, SC14 fitted to Toyota 1G-GZE engine, 2.0 Litres probably driven around 1.1 crank speed, 160 Kw worth of airflow. Boost in the region of 8 psi, blower driven intermittently only. M90 fitted to Jaguar 4.0 Litre, driven continuously at 2.5 times crank speed, 230 Kw worth of airflow, boost level 10 psi. M90 fitted to Holden 3.8 Litre V6, driven at 1.8 times crank speed, boost 7 psi, 165 Kw worth of airflow.